Method for preparing hydrophobic porous oil-water separation material
A technology of oil-water separation and hydrophobicity, which is applied in the field of material processing, can solve the problems of poor adsorption performance and unsustainable use of materials, and achieve the effect of improving surface roughness and excellent hydrophobicity
- Summary
- Abstract
- Description
- Claims
- Application Information
AI Technical Summary
Problems solved by technology
Method used
Examples
example 1
[0020] According to the mass ratio of 1:1, the sliced paraffin and liquid paraffin were stirred and mixed, and heated in a water bath at 65°C for 2 hours to obtain molten paraffin, and then weighed 45 parts of obsidian, 25 parts of pitch rock and 15 parts of turpentine in parts by weight. Perlite, stirred and mixed and placed in a ball mill tank, ball milled at 200r / min for 3 hours, passed through a 200-mesh sieve to obtain ball mill powder, according to the mass ratio of 1:3, put the ball mill powder and molybdenum disulfide powder on two sides of the quartz tube pipeline respectively On the side, seal the quartz tube and evacuate to 3Pa, heat up to 450°C, stop vacuuming and pass argon into the quartz tube, control the argon flow rate to 45mL / min, keep warm for 25min, then let it cool down to room temperature , stop feeding argon, collect the modified particles, mix the modified particles with molten paraffin at a mass ratio of 1:2, heat in an oven at 65°C for 6 hours, stir ...
example 2
[0022] According to the mass ratio of 1:1, the sliced paraffin and liquid paraffin were stirred and mixed, and heated in a water bath at 68°C for 2 hours to obtain molten paraffin. Then, in parts by weight, 46 parts of obsidian, 28 parts of pitch rock and 18 parts of turpentine were weighed. Perlite, stirred and mixed and placed in a ball mill tank, ball milled at 250r / min for 4 hours, passed through a 200-mesh sieve to obtain ball mill powder, according to the mass ratio of 1:3, put the ball mill powder and molybdenum disulfide powder on two sides of the quartz tube pipeline respectively On the side, seal the quartz tube and evacuate to 4Pa, heat up to 500°C, stop vacuuming and pass argon into the quartz tube, control the argon flow rate to 48mL / min, keep warm for 28min, and then let it cool down to room temperature , stop feeding argon, collect the modified particles, mix the modified particles with molten paraffin at a mass ratio of 1:2, heat in an oven at 68°C for 7 hours...
example 3
[0024]According to the mass ratio of 1:1, the sliced paraffin and liquid paraffin were stirred and mixed, and heated in a water bath at 70°C for 3 hours to obtain molten paraffin. Then, in parts by weight, 50 parts of obsidian, 30 parts of pitch rock and 20 parts of turpentine were weighed. Perlite, stirred and mixed and placed in a ball mill tank, ball milled at 300r / min for 5h, passed through a 200 mesh sieve to obtain ball mill powder, according to the mass ratio of 1:3, the ball mill powder and molybdenum disulfide powder were placed on two sides of the quartz tube pipeline respectively On the side, seal the quartz tube and evacuate to 5Pa, heat up to 550°C, stop vacuuming and pass argon into the quartz tube, control the argon flow rate to 50mL / min, keep warm for 30min, and then let it cool down to room temperature , stop feeding argon, collect the modified particles, mix the modified particles with molten paraffin at a mass ratio of 1:2, heat in an oven at 70°C for 8 hou...
PUM
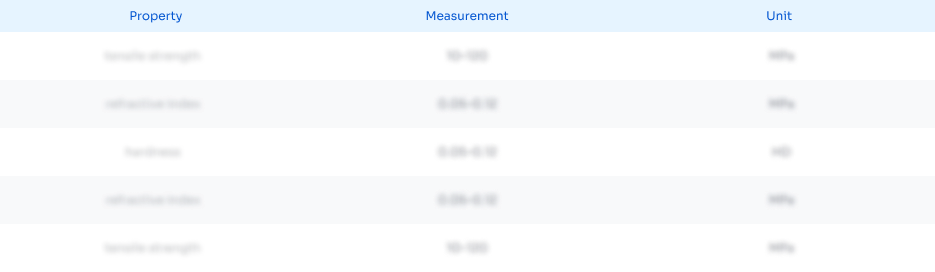
Abstract
Description
Claims
Application Information

- R&D Engineer
- R&D Manager
- IP Professional
- Industry Leading Data Capabilities
- Powerful AI technology
- Patent DNA Extraction
Browse by: Latest US Patents, China's latest patents, Technical Efficacy Thesaurus, Application Domain, Technology Topic, Popular Technical Reports.
© 2024 PatSnap. All rights reserved.Legal|Privacy policy|Modern Slavery Act Transparency Statement|Sitemap|About US| Contact US: help@patsnap.com