Preparation method of anti-cracking autoclaved brick
An autoclaved brick and anti-cracking technology, applied in the field of autoclaved bricks, can solve the problems of poor compressive strength and easy cracking, achieve good compression and crack resistance, not easy to crack or break, and save cultivated land resources
- Summary
- Abstract
- Description
- Claims
- Application Information
AI Technical Summary
Problems solved by technology
Method used
Image
Examples
Embodiment 1
[0018] A preparation method of an anti-cracking autoclaved brick, comprising the steps of:
[0019] S1. Mix the modified chlorinated polyethylene glycol 400, fly ash, kaolin, and water evenly, add cement, water reducer, and curing agent, mix evenly, and press to form a premix;
[0020] S2. Sending the premix into the autoclaved room for curing to obtain anti-cracking autoclaved bricks.
Embodiment 2
[0022] A preparation method of an anti-cracking autoclaved brick, comprising the steps of:
[0023] S1. Mix 40 parts of modified chlorinated polyethylene glycol 400, 100 parts of fly ash, 20 parts of kaolin, and 20 parts of water in parts by weight, and add 10 parts of cement, 4 parts of water reducer and 1 part of curing agent. Uniform, compression molding, compression pressure is 24MPa, compression time is 4h, obtains premix;
[0024] S2. Send the premixed material into the autoclave room for curing for 20 hours, the steam pressure is 4 MPa, and the steam temperature is 220° C. to obtain anti-cracking autoclaved bricks.
Embodiment 3
[0026] A preparation method of an anti-cracking autoclaved brick, comprising the steps of:
[0027] S1. Mix 60 parts of modified chlorinated polyethylene glycol 400, 80 parts of fly ash, 30 parts of kaolin, and 15 parts of water in parts by weight, and add 20 parts of cement, 2 parts of water reducer and 2 parts of curing agent to mix Uniform, compression molding, compression pressure is 20MPa, compression time is 8h, obtains premix;
[0028] Modified chlorinated polyethylene glycol 400 is prepared by the following process: mix chlorinated polyethylene glycol 400 and oxidized starch, ultrasonically disperse, add sodium hydroxide and sodium lignosulfonate when the temperature rises, stir under nitrogen protection, cool, adjust The pH value of the system is neutral, and modified chlorinated polyethylene glycol 400 is obtained;
[0029] S2. Send the premixed material into the autoclave room for curing for 12 hours, the steam pressure is 6 MPa, and the steam temperature is 200° C...
PUM
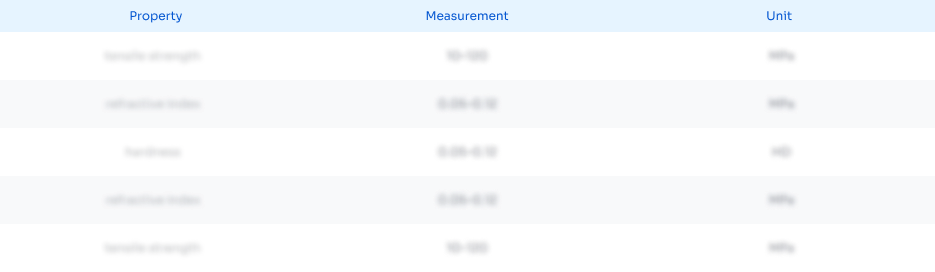
Abstract
Description
Claims
Application Information

- Generate Ideas
- Intellectual Property
- Life Sciences
- Materials
- Tech Scout
- Unparalleled Data Quality
- Higher Quality Content
- 60% Fewer Hallucinations
Browse by: Latest US Patents, China's latest patents, Technical Efficacy Thesaurus, Application Domain, Technology Topic, Popular Technical Reports.
© 2025 PatSnap. All rights reserved.Legal|Privacy policy|Modern Slavery Act Transparency Statement|Sitemap|About US| Contact US: help@patsnap.com