Silane treating agent and method for preparing silane treating agent
A technology of silane treatment agent and silane coupling agent, applied in the direction of metal material coating process, can solve the problems of harsh process conditions, environmental pollution, workpiece rust, etc., achieve good salt spray performance, simple use, and reduce energy consumption Effect
- Summary
- Abstract
- Description
- Claims
- Application Information
AI Technical Summary
Problems solved by technology
Method used
Image
Examples
Embodiment 1
[0046] The composition and dosage of the silane treatment agent of Example 1 are as follows:
[0047]
[0048] Add 20 parts of ethanol to 300 parts of water, slowly add 45 parts of aminopropyltrimethoxysilane while stirring, stir for about half an hour to completely dissolve, then add 8 parts of glycerin and 2 parts of sodium tricarboxylate successively, and stir After half an hour, add 8 parts of water-based acrylic resin, stir and mix, and add 617 parts of water to obtain the silane treatment agent.
[0049] Application of silane treatment agent: At room temperature, put the iron parts cleaned with oil stains into the silane treatment agent, soak for 1.5 minutes, take it out, and put it into the oven to dry to promote film formation. The drying temperature is 100 degrees.
Embodiment 2
[0051] The composition and dosage of the silane treatment agent of Example 2 are as follows:
[0052]
[0053] Add 18 parts of ethanol to 300 parts of water, slowly add 50 parts of aminopropyltrimethoxysilane while stirring, stir for about half an hour to completely dissolve, then add 10 parts of glycerin and 3 parts of sodium tricarboxylate in sequence, and stir After half an hour, add 10 parts of water-based acrylic resin, stir and mix, and add 609 parts of water to obtain the silane treatment agent.
[0054] Application of silane treatment agent: At room temperature, put the iron parts cleaned with oil stains into the silane treatment agent, soak for 1.5 minutes, take it out, and put it into the oven to dry to promote film formation. The drying temperature is 100 degrees.
Embodiment 3
[0056] The composition and dosage of the silane treatment agent of Example 3 are as follows:
[0057]
[0058]
[0059] Add 18 parts of ethanol to 300 parts of water, slowly add 45 parts of aminopropyltrimethoxysilane while stirring, stir for about half an hour until it is completely dissolved, then add 10 parts of glycerin and 2 parts of boric acid in sequence, and stir for half an hour. Then add 8 parts of water-based acrylic resin, stir and mix, and add 617 parts of water to obtain the silane treatment agent.
[0060] Application of silane treatment agent: At room temperature, put the iron parts cleaned with oil stains into the silane treatment agent, soak for 1.5 minutes, take it out, and put it into the oven to dry to promote film formation. The drying temperature is 100 degrees.
PUM
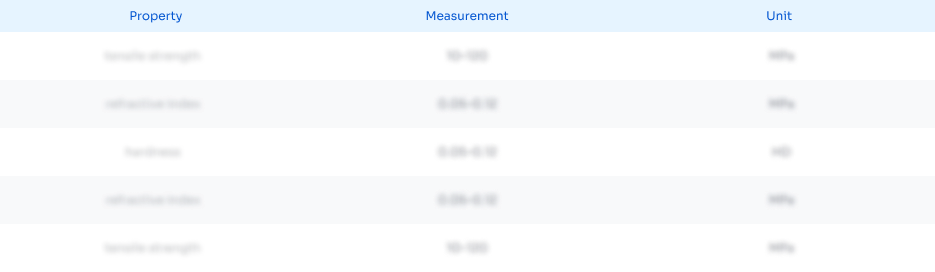
Abstract
Description
Claims
Application Information

- Generate Ideas
- Intellectual Property
- Life Sciences
- Materials
- Tech Scout
- Unparalleled Data Quality
- Higher Quality Content
- 60% Fewer Hallucinations
Browse by: Latest US Patents, China's latest patents, Technical Efficacy Thesaurus, Application Domain, Technology Topic, Popular Technical Reports.
© 2025 PatSnap. All rights reserved.Legal|Privacy policy|Modern Slavery Act Transparency Statement|Sitemap|About US| Contact US: help@patsnap.com