A non-ironing fabric and a manufacturing process therefor
A manufacturing process and textile technology, applied in the field of non-ironing textiles and its manufacturing process, can solve the problems of high price, loss of natural fiber properties, relatively large loss of mechanical properties, etc., and achieve low price, good non-ironing performance, and good The effect of easy-care performance
- Summary
- Abstract
- Description
- Claims
- Application Information
AI Technical Summary
Problems solved by technology
Method used
Examples
Embodiment 1
[0024] (1) Wash the cotton fiber with clear water, dry it, and place it in a plasma device for processing. The discharge frequency of the plasma is 8000 Hz, and take it out for use after processing.
[0025] (2) Mix 2 g of citric acid, 1.5 g of acrylamide methyl starch, 1.5 g of carboxymethyl cellulose and deionized water, sonicate for 1 h at 500 W power, continue to add 1 g of sodium carbonate, 0.2 g of crosslinking agent, and 0.2 g of catalyst , and stirred for 30 minutes to obtain a non-ironing finishing solution.
[0026] (3) Dip the cotton fiber through the plasma treatment in the non-ironing finishing solution, two dips and two pricks, the scrapping rate is 60-80%, and the cotton fiber after the treatment is cleaned 2-3 times with flowing water. to dry.
[0027] (4) The processed cotton fiber, polyester fiber or hemp fiber is made into textile by existing spinning method and knitting process, pre-dried at 80°C, and baked at 110°C for 2 minutes to obtain a new type of no...
Embodiment 2
[0029] (1) Wash the cotton fiber with clear water, dry it, and place it in a plasma device for processing. The discharge frequency of the plasma is 8000 Hz, and take it out for use after processing.
[0030] (2) Mix 5 g of citric acid, 2 g of acrylamide methyl starch, 2 g of carboxymethyl cellulose and deionized water, sonicate for 2 hours at a power of 500 W, continue to add 1.5 g of sodium carbonate, 0.6 g of a crosslinking agent, and 0.5 g of a catalyst, Stir for 60 minutes to obtain a non-ironing finishing solution.
[0031] (3) Dip the cotton fiber through the plasma treatment in the non-ironing finishing solution, two dips and two pricks, the scrapping rate is 60-80%, and the cotton fiber after the treatment is cleaned 2-3 times with flowing water. to dry.
[0032] (4) The processed cotton fibers, polyester fibers or hemp fibers are made into textiles by the existing spinning method and knitting process, pre-dried at 90°C, and baked at 119°C for 5 minutes to obtain a ne...
Embodiment 3
[0034] (1) Wash the cotton fiber with clear water, dry it, and place it in a plasma device for processing. The discharge frequency of the plasma is 8000 Hz, and take it out for use after processing.
[0035] (2) Mix 0.3g of citric acid, 1.6g of acrylamide methyl starch, 1.6g of carboxymethyl cellulose and deionized water, ultrasonicate for 70min at 500W power, continue to add 1.1g of sodium carbonate, 0.3g of crosslinking agent, catalyst 0.3g, stirred for 35min to obtain a no-iron finishing solution.
[0036] (3) Dip the cotton fiber through the plasma treatment in the non-ironing finishing solution, two dips and two pricks, the scrapping rate is 60-80%, and the cotton fiber after the treatment is cleaned 2-3 times with flowing water. to dry.
[0037] (4) The processed cotton fibers, polyester fibers or hemp fibers are made into textiles by the existing spinning method and knitting process, pre-dried at 82°C, and baked at 111°C for 3 minutes to obtain a new type of non-ironin...
PUM
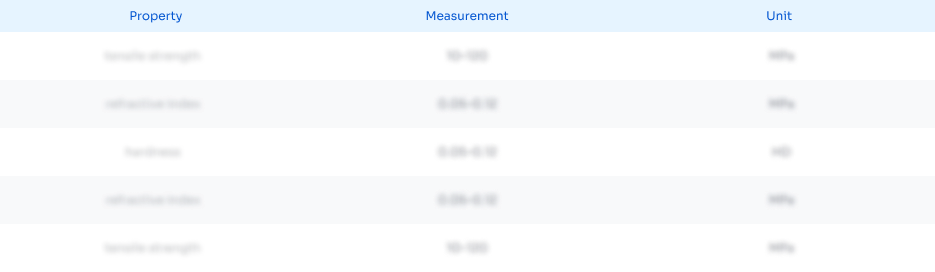
Abstract
Description
Claims
Application Information

- Generate Ideas
- Intellectual Property
- Life Sciences
- Materials
- Tech Scout
- Unparalleled Data Quality
- Higher Quality Content
- 60% Fewer Hallucinations
Browse by: Latest US Patents, China's latest patents, Technical Efficacy Thesaurus, Application Domain, Technology Topic, Popular Technical Reports.
© 2025 PatSnap. All rights reserved.Legal|Privacy policy|Modern Slavery Act Transparency Statement|Sitemap|About US| Contact US: help@patsnap.com