High-temperature alloy for heat-resisting cushion block and heat-resisting cushion block for steel rolling heating furnace
A high-temperature alloy and heating furnace technology, which is applied in the field of high-temperature alloy materials, can solve the problems that the service life cannot be effectively guaranteed, wear, and affect the service life, so as to improve high-temperature oxidation resistance and high-temperature build-up resistance, and good tissue stability Performance and high temperature compression creep resistance, anti-corrosion or wear effect
- Summary
- Abstract
- Description
- Claims
- Application Information
AI Technical Summary
Problems solved by technology
Method used
Image
Examples
Embodiment 1
[0023] A kind of heat-resistant pad for steel rolling heating furnace, according to the chemical composition of the superalloy used in the heat-resistant pad designed by the present invention, it includes the following components in weight percentage: C 0.05%, Si 0.5%, Mn 0.5%, Cr 26%, Ni 13%, W 1.5%, Mo 1%, Nb 0.5%, Ce 0.02%, Zr 0.02%, Fe 0.01%, the rest is Co and unavoidable impurities. The alloy material with the above ratio is melted in a vacuum induction furnace, wherein Zr and Ce are added during the second alloying treatment, then poured into an ingot mold, and cooled to obtain a master alloy ingot. Then the master alloy ingot was put into a vacuum induction furnace for rapid remelting, poured into the mold shell, and finally the vacuum was broken to take out the mold to obtain the 1# test piece.
Embodiment 2
[0025] A kind of heat-resistant spacer for steel rolling heating furnace, according to the chemical composition of the superalloy used in the heat-resistant spacer designed by the present invention, it includes the following components in weight percentage: C 0.12%, Si 0.9%, Mn 0.6%, Cr 28.5%, Ni 14.5%, W 1.9%, Mo 1.3%, Nb 0.8%, Ce 0.08%, Zr 0.06%, Fe 4%, the rest is Co and unavoidable impurities. The alloy material with the above ratio is melted in a vacuum induction furnace, wherein Zr and Ce are added during the second alloying treatment, then poured into an ingot mold, and cooled to obtain a master alloy ingot. Then the master alloy ingot was put into a vacuum induction furnace for rapid remelting, poured into the mold shell, and finally the vacuum was broken to take out the mold to obtain the 2# test piece.
Embodiment 3
[0027]A kind of heat-resistant spacer for steel rolling heating furnace, according to the chemical composition of the superalloy for heat-resistant spacer designed in the present invention, it comprises following composition by weight percentage: C 0.16%, Si 1.2%, Mn 0.9%, Cr 29.5%, Ni 15%, W 2.4%, Mo 1.5%, Nb 1.1%, Ce 0.12%, Zr 0.04%, Fe 2%, the rest is Co and unavoidable impurities. The alloy material with the above ratio is melted in a vacuum induction furnace, wherein Zr and Ce are added during the second alloying treatment, then poured into an ingot mold, and cooled to obtain a master alloy ingot. Then the master alloy ingot was put into a vacuum induction furnace for rapid remelting, poured into the mold shell, and finally the vacuum was broken to take out the mold to obtain the 3# test piece.
PUM
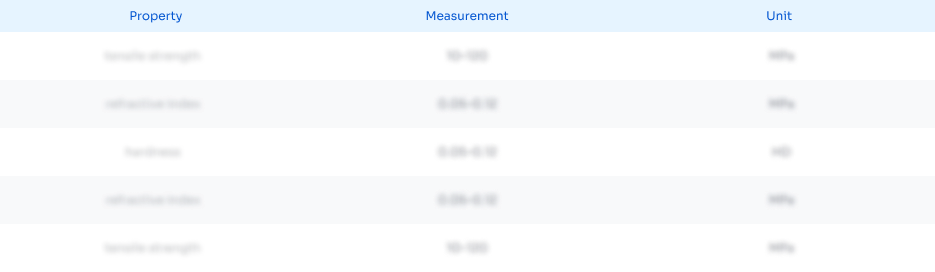
Abstract
Description
Claims
Application Information

- Generate Ideas
- Intellectual Property
- Life Sciences
- Materials
- Tech Scout
- Unparalleled Data Quality
- Higher Quality Content
- 60% Fewer Hallucinations
Browse by: Latest US Patents, China's latest patents, Technical Efficacy Thesaurus, Application Domain, Technology Topic, Popular Technical Reports.
© 2025 PatSnap. All rights reserved.Legal|Privacy policy|Modern Slavery Act Transparency Statement|Sitemap|About US| Contact US: help@patsnap.com