High temperature wear resistant alloy
A high-temperature wear-resistant alloy, heavy-duty transmission technology, which is used in the field of materials for making low-speed, heavy-duty transmission shaft supports, and can solve problems such as short service life
- Summary
- Abstract
- Description
- Claims
- Application Information
AI Technical Summary
Problems solved by technology
Method used
Examples
Embodiment Construction
[0006] The manufacturing process of this alloy is no different from that of general ferroalloys. The electric furnace is used for smelting, and the technological process is batching-melting-oxidation-slagging-reduction-oxygen blowing-casting-annealing. Ferro-molybdenum, nickel, and ferro-tungsten can be added with scrap steel or at the end of melting, and ferromanganese and ferrochrome can be added in the reduction stage. These processes are mature processes for smelting ferroalloys in general, and the content of various added elements is also standard. However, niobium steel, iron sulfur and trace rare earths are added to the furnace or added to the steel with the steel flow before being released from the furnace. After being made into a material, as long as the niobium content in the alloy accounts for 0.5-2% of the total weight of the alloy, and the sulfur content is 2.5-6%.
PUM
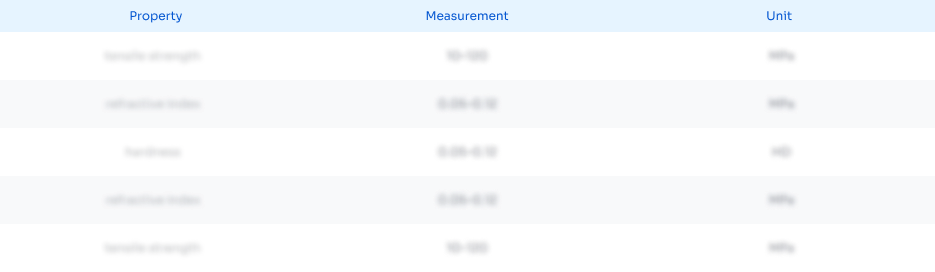
Abstract
Description
Claims
Application Information

- Generate Ideas
- Intellectual Property
- Life Sciences
- Materials
- Tech Scout
- Unparalleled Data Quality
- Higher Quality Content
- 60% Fewer Hallucinations
Browse by: Latest US Patents, China's latest patents, Technical Efficacy Thesaurus, Application Domain, Technology Topic, Popular Technical Reports.
© 2025 PatSnap. All rights reserved.Legal|Privacy policy|Modern Slavery Act Transparency Statement|Sitemap|About US| Contact US: help@patsnap.com