Enhanced thermoplastic starch composite material and preparation method thereof
A technology of enhanced thermoplastic and composite materials, applied in the field of thermoplastic polymer materials, can solve the problems of poor mechanical properties and thermal stability, and achieve the effects of reducing water absorption, reducing rigidity, improving mechanical properties and thermal stability
- Summary
- Abstract
- Description
- Claims
- Application Information
AI Technical Summary
Problems solved by technology
Method used
Image
Examples
example 1
[0026] Weigh 5kg of hemp fiber, put it into a pulverizer after natural air drying, and pass through a 100-mesh sieve. Put the sieved hemp fiber powder into a steam explosion tank, heat it to 200°C under a sulfur dioxide atmosphere, and then pour it into a steam explosion tank. Introduce steam until the pressure inside the tank is 1.9 MPa. After maintaining the pressure for 8 minutes, open the valve of the steam explosion tank to release the pressure. After releasing the pressure to normal pressure, filter to obtain filter residue A, and wash filter residue A with 80°C deionized water for 5 times to obtain steam explosion treatment. Hemp fiber powder after steam explosion treatment; Weigh 200g of hemp fiber powder after steam explosion treatment, soak in 600mL mass fraction of 10% hydrogen peroxide solution, react in 80°C constant temperature water bath for 2h, get mixed solution, and then use mass fraction of 5% sodium hydroxide solution to adjust the pH of the mixed solution t...
example 2
[0028] Weigh 3kg of hemp fiber, put it into a pulverizer after natural air drying, and pass through a 100-mesh sieve. Put the sieved hemp fiber powder into a steam explosion tank, heat it to 180°C under a sulfur dioxide atmosphere, and then pour it into a steam explosion tank. Introduce steam until the pressure inside the tank is 1.6 MPa. After maintaining the pressure for 5 minutes, open the valve of the steam explosion tank to release the pressure. After releasing the pressure to normal pressure, filter the filter residue A, and wash the filter residue A with 70°C deionized water for 3 times to obtain steam explosion treatment. Hemp fiber powder after steam explosion treatment; Weigh 100g of hemp fiber powder after steam explosion treatment, soak in 500mL mass fraction of 10% hydrogen peroxide solution, react in a 70°C constant temperature water bath for 1h to obtain a mixed solution, and then use a mass fraction of 5% sodium hydroxide solution to adjust the pH of the mixed s...
example 3
[0030] Weigh 4kg of hemp fiber, put it into a pulverizer after natural air drying, and pass through a 100-mesh sieve. Put the sieved hemp fiber powder into a steam explosion tank, heat it to 190°C under a sulfur dioxide atmosphere, and then pour it into a steam explosion tank. Introduce steam until the pressure inside the tank is 1.7MPa. After maintaining the pressure for 7 minutes, open the valve of the steam explosion tank to release the pressure. After releasing the pressure to normal pressure, filter the filter residue A, and wash the filter residue A 4 times with 75°C deionized water to obtain steam explosion treatment. Hemp fiber powder after steam explosion treatment; Weigh 150g of hemp fiber powder after steam explosion treatment, soak in 550mL mass fraction of 10% hydrogen peroxide solution, react in a 75°C constant temperature water bath for 1h to obtain a mixed solution, and then use the mass fraction of 5% sodium hydroxide solution to adjust the pH of the mixed solu...
PUM
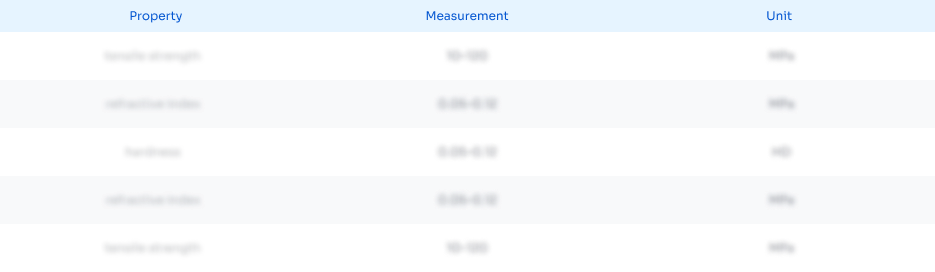
Abstract
Description
Claims
Application Information

- R&D
- Intellectual Property
- Life Sciences
- Materials
- Tech Scout
- Unparalleled Data Quality
- Higher Quality Content
- 60% Fewer Hallucinations
Browse by: Latest US Patents, China's latest patents, Technical Efficacy Thesaurus, Application Domain, Technology Topic, Popular Technical Reports.
© 2025 PatSnap. All rights reserved.Legal|Privacy policy|Modern Slavery Act Transparency Statement|Sitemap|About US| Contact US: help@patsnap.com