Method for recycling textile wastewater to prepare submicron calcium-based rigid material
A sub-micron textile wastewater technology, applied in textile industrial wastewater treatment, chemical instruments and methods, water/sewage multi-stage treatment, etc., can solve solid waste TA problems such as poor purity, no reuse value, and poor dehydration
- Summary
- Abstract
- Description
- Claims
- Application Information
AI Technical Summary
Problems solved by technology
Method used
Image
Examples
Embodiment 1
[0026] Step 1: Adjust the pH value of the waste water to 10, add basic aluminum chloride, stir at a speed of 400 rpm for 10 minutes, and then slowly stir at a speed of 100 rpm for 20 minutes, filter the suspension through cinders, and filter the filtrate through activated carbon device to obtain clear liquid.
[0027] Step 2: add sulfuric acid to the clear liquid, adjust the pH to 3.5, precipitate terephthalic acid (TA), and obtain TA emulsion;
[0028] Step 3: TA emulsion and calcium hydroxide slurry are reacted in an ultrasonically enhanced tubular reactor, and the output is separated from solid and liquid. After drying at 150°C, the filter cake can be used as a functional additive for rubber and plastic materials, and the filtrate is discharged. Enter the biochemical treatment system, and discharge or reuse after further treatment reaches the standard.
[0029] The molar ratio of TA to calcium hydroxide is 1:1.
[0030] The applied frequency of the ultrasonic wave is 55KH...
Embodiment 2
[0034] The difference between embodiment 2 and embodiment 1 is:
[0035] In step 1, adjust the pH value of the wastewater to 11, add basic aluminum chloride, stir at 800 rpm for 3 minutes, and then slowly stir at 300 rpm for 10 minutes.
[0036] In step 2, sulfuric acid was added to the clear liquid to adjust the pH to 4.2.
[0037] The molar ratio of TA to calcium hydroxide is 1:1.1.
[0038] The ultrasonic wave is applied at a frequency of 75KHz and a power of 600W.
[0039] The CODcr detection of the effluent filtrate of step 3 was carried out by the method of test 1, and the results are shown in Table 1.
Embodiment 3
[0041] The difference between embodiment 3 and embodiment 1 is:
[0042] In step 1, adjust the pH value of the waste water to 10.5, add basic aluminum chloride, stir at a speed of 600 rpm for 7 minutes, and then slowly stir at a speed of 200 rpm for 15 minutes.
[0043] In step 2, sulfuric acid was added to the clear liquid to adjust the pH to 4.0.
[0044] The molar ratio of TA to calcium hydroxide is 1:1.05.
[0045] The applied frequency of the ultrasonic wave is 65KHz, and the power is 500W.
[0046] The CODcr detection of the effluent filtrate of step 3 was carried out by the method of test 1, and the results are shown in Table 1.
PUM
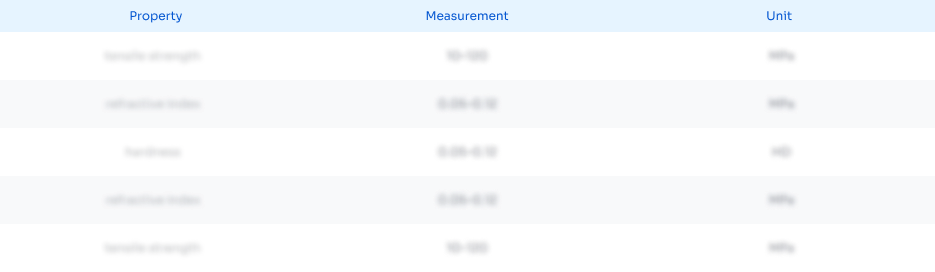
Abstract
Description
Claims
Application Information

- R&D Engineer
- R&D Manager
- IP Professional
- Industry Leading Data Capabilities
- Powerful AI technology
- Patent DNA Extraction
Browse by: Latest US Patents, China's latest patents, Technical Efficacy Thesaurus, Application Domain, Technology Topic, Popular Technical Reports.
© 2024 PatSnap. All rights reserved.Legal|Privacy policy|Modern Slavery Act Transparency Statement|Sitemap|About US| Contact US: help@patsnap.com