A high-temperature-resistant and anti-corrosion electric heating belt coating and its coating method
An electric heating band and high-temperature-resistant technology, which is applied in the direction of anti-corrosion coatings, fire-proof coatings, coatings, etc., can solve problems such as poor electrical insulation, loss of insulation ability, environmental debris pollution, etc., to avoid insulation aging and deterioration, and avoid coating Layer peeling, the effect of improving heat resistance and aging resistance
- Summary
- Abstract
- Description
- Claims
- Application Information
AI Technical Summary
Problems solved by technology
Method used
Examples
Embodiment 1
[0021] A method for coating a high-temperature-resistant and anti-corrosion electric heating belt coating, comprising the following steps:
[0022] Step 1. Weigh the silicone resin, add 2.0 times its weight of inorganic filler to the silicone resin, stir to obtain a mixture, then add a nano-modifier whose weight is 2.5% of the total weight of the mixture, and add 3 times the weight of the mixture weight of deionized water, stirred evenly, ball milled, filtered, and dried to obtain a powder, the powder was placed in a reaction kettle, and ethanol, glycerin and surfactant were added, and the reaction kettle was heated to 85°C under 1.3 atmospheric pressure , after reacting for 4 hours, stop heating, take out the material after standing for 2.5 hours, wash with deionized water, and dry to obtain a modified inorganic filler for subsequent use; the inorganic filler is composed of magnesium oxide, zinc oxide and aluminum oxide, magnesium oxide, The weight ratio of zinc oxide and alu...
Embodiment 2
[0026] A method for coating a high-temperature-resistant and anti-corrosion electric heating belt coating, comprising the following steps:
[0027] Step 1. Weigh the silicone resin, add 1.7 times its weight of inorganic filler to the silicone resin, stir to obtain a mixture, then add a nano-modifier whose weight is 1% of the total weight of the mixture, and add 2.0 times the weight of the mixture weight of deionized water, stirred evenly, ball milled, filtered, and dried to obtain a powder, the powder was placed in a reaction kettle, and ethanol, glycerin and surfactant were added, and the reaction kettle was heated to 75°C under 1.5 atmospheric pressure , after reacting for 4.5 hours, stop heating, take out the material after standing for 2 hours, wash with deionized water, and dry to obtain a modified inorganic filler for subsequent use; the inorganic filler is composed of magnesium oxide, zinc oxide and aluminum oxide, magnesium oxide, The weight ratio of zinc oxide and alu...
Embodiment 3
[0031] A method for coating a high-temperature-resistant and anti-corrosion electric heating belt coating, comprising the following steps:
[0032]Step 1. Weigh the silicone resin, add 1.5 times its weight of inorganic filler to the silicone resin, stir to obtain a mixture, then add a nano-modifier whose weight is 3% of the total weight of the mixture, and add 1.5 times the weight of the mixture weight of deionized water, stirred evenly, ball milled, filtered, and dried to obtain a powder, the powder was placed in a reaction kettle, and ethanol, glycerol and surfactant were added, and the reaction kettle was heated to 70°C under 1.2 atmospheric pressure , after reacting for 5 hours, stop heating, take out the material after standing for 3 hours, wash with deionized water, and dry to obtain a modified inorganic filler for subsequent use; the inorganic filler is composed of magnesium oxide, zinc oxide and aluminum oxide, magnesium oxide, oxide The weight ratio of zinc and alumin...
PUM
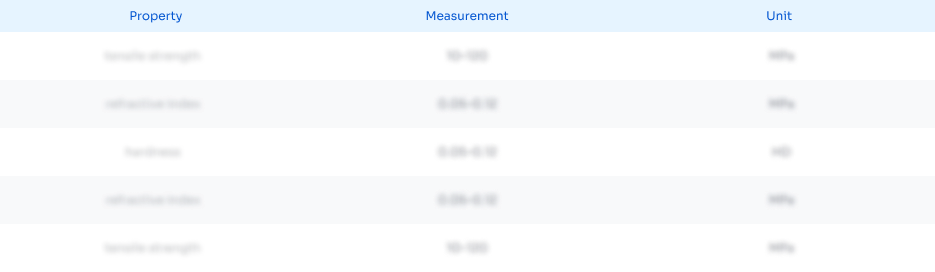
Abstract
Description
Claims
Application Information

- Generate Ideas
- Intellectual Property
- Life Sciences
- Materials
- Tech Scout
- Unparalleled Data Quality
- Higher Quality Content
- 60% Fewer Hallucinations
Browse by: Latest US Patents, China's latest patents, Technical Efficacy Thesaurus, Application Domain, Technology Topic, Popular Technical Reports.
© 2025 PatSnap. All rights reserved.Legal|Privacy policy|Modern Slavery Act Transparency Statement|Sitemap|About US| Contact US: help@patsnap.com