Heat treatment process method and manufacturing process method for thin-film resistor
A technology of thin film resistors and process methods, which is used in resistor manufacturing, resistors, and coating resistor materials, etc., can solve the problem of poor resistance change rate, large resistance deviation, product resistance to over-stress and over-electricity exposed to high temperature The problem of poor fatigue performance, etc., achieves the effect of good resistance accuracy consistency, improved overcurrent resistance performance, and high pass rate
- Summary
- Abstract
- Description
- Claims
- Application Information
AI Technical Summary
Problems solved by technology
Method used
Image
Examples
Embodiment 1
[0055] see figure 1 , an embodiment of the present invention provides a thin film resistance heat treatment process, the thin film resistance heat treatment process comprising:
[0056] Step S101: using a heat treatment box to heat the thin film resistance to a first temperature point, and maintaining the first temperature point for a preset heating time.
[0057] For example, use a heat treatment box to heat the thin film resistance to 390-450 degrees Celsius, and maintain the temperature at 390-450 degrees Celsius for 2h-7h. Of course, the first temperature point can be 390 degrees Celsius or 425 degrees Celsius or 450 degrees Celsius, and there is no limit here, as long as it is between 390 and 450 degrees Celsius, the heating time can be 2h, 4.5h or 7h, and there is no limit here , as long as it is within the range of 2h ~ 7h.
[0058] Step S102: After a preset heating time, at least one second temperature point is used to cool down the thin film resistor for a preset co...
Embodiment 2
[0071] see image 3 , the embodiment of the present invention also provides a thin film resistor manufacturing process method, the thin film resistor manufacturing process method includes:
[0072] Step S301: Prepare electrodes on a ceramic substrate by printing.
[0073] Step S302: printing an insulating barrier layer on a part of the ceramic substrate.
[0074] Step S303: Sputtering a resistive material with a certain resistivity onto the remaining exposed area of the ceramic substrate by magnetron sputtering to prepare an initial thin film resistor.
[0075] Step S304: performing heat treatment on the initial thin film resistor by using the above thin film resistor heat treatment process.
[0076] Step S305: removing the insulating barrier layer.
[0077] For example, the insulating barrier layer is washed off with clean water.
[0078] Step S306: performing laser trimming on the initial thin film resistance.
[0079] Step S307: Encapsulating the initial thin film re...
PUM
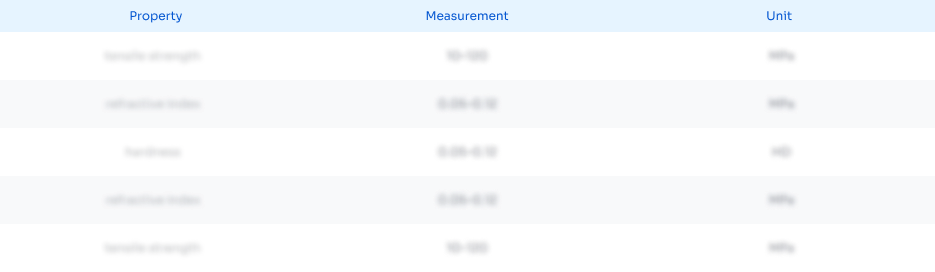
Abstract
Description
Claims
Application Information

- Generate Ideas
- Intellectual Property
- Life Sciences
- Materials
- Tech Scout
- Unparalleled Data Quality
- Higher Quality Content
- 60% Fewer Hallucinations
Browse by: Latest US Patents, China's latest patents, Technical Efficacy Thesaurus, Application Domain, Technology Topic, Popular Technical Reports.
© 2025 PatSnap. All rights reserved.Legal|Privacy policy|Modern Slavery Act Transparency Statement|Sitemap|About US| Contact US: help@patsnap.com