A kind of manufacturing method of resin plug hole circuit board
A manufacturing method and resin plug hole technology, applied in the directions of printed circuit manufacturing, printed circuits, printed circuits, etc., can solve the problems of low production efficiency, high production cost, long process, etc., to improve the quality, shorten the production cycle, and strengthen the depth. effect of ability
- Summary
- Abstract
- Description
- Claims
- Application Information
AI Technical Summary
Problems solved by technology
Method used
Examples
Embodiment
[0027] The manufacturing method of a resin plugged circuit board shown in this embodiment includes the following processing steps in sequence: material cutting→inner layer circuit making→pressing→drilling→copper sinking→full board electroplating→filling resin→sanding Belt grinding plate 1 → mask hole pattern → cover hole and reduce copper → abrasive belt grinding plate 2 → sink copper 2 → full plate electroplating 2 → outer layer circuit production → solder mask → silk screen characters → surface treatment → forming, the specific steps are as follows:
[0028] a. Cutting: cut out the core board according to the panel size 520mm×620mm, and the thickness of the core board is 1.2mm H / H;
[0029] b. Inner layer circuit production (negative film process): Inner layer graphics transfer, use a vertical coating machine to coat photosensitive film, the thickness of the photosensitive film is controlled to 8 μm, use a fully automatic exposure machine, and use a 5-6 grid exposure ruler (2...
PUM
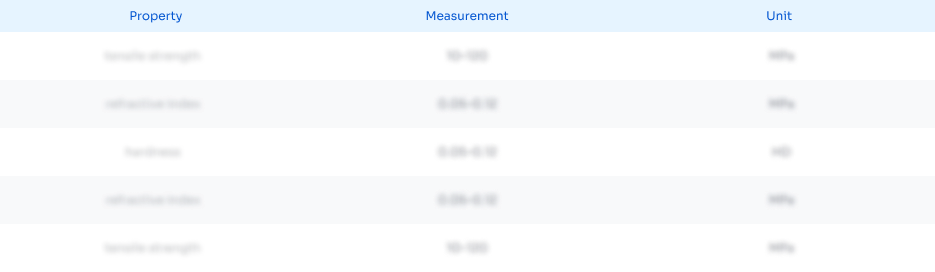
Abstract
Description
Claims
Application Information

- Generate Ideas
- Intellectual Property
- Life Sciences
- Materials
- Tech Scout
- Unparalleled Data Quality
- Higher Quality Content
- 60% Fewer Hallucinations
Browse by: Latest US Patents, China's latest patents, Technical Efficacy Thesaurus, Application Domain, Technology Topic, Popular Technical Reports.
© 2025 PatSnap. All rights reserved.Legal|Privacy policy|Modern Slavery Act Transparency Statement|Sitemap|About US| Contact US: help@patsnap.com