Hard alloy material
A technology of cemented carbide and tungsten carbide alloy, which is applied in the field of composite materials, can solve the problems of cemented carbide, such as reduced hardness, compression resistance, shortened service life, and single composition, so as to achieve good hardness, improve high temperature resistance and The effect of toughness, excellent high temperature resistance and corrosion resistance
- Summary
- Abstract
- Description
- Claims
- Application Information
AI Technical Summary
Problems solved by technology
Method used
Image
Examples
Embodiment 1
[0017] A kind of cemented carbide material, comprises the raw material of following weight part:
[0018] 12 parts of titanium carbide, 5 parts of titanium nitride, 4 parts of tantalum carbide, 3 parts of boron carbide, SiC-Al 2 o 3 -Y 2 o 3 30 parts of nanocomposite powder, 18 parts of nickel-based tungsten carbide alloy powder, and 7 parts of Co60 cobalt-based alloy powder.
[0019] The preparation steps of above-mentioned cemented carbide material are as follows:
[0020] Put the above raw materials into the grinder according to the above ratio for mixing and grinding. The speed of the grinder is 100r / min, and the grinding time is 2.5h. After grinding, press at 510MPa, and sinter at 650°C for 30min in an argon atmosphere. , to be naturally cooled, that is, cemented carbide materials.
Embodiment 2
[0022] A kind of cemented carbide material, comprises the raw material of following weight part:
[0023] 13 parts of titanium carbide, 6 parts of titanium nitride, 5 parts of tantalum carbide, 3 parts of boron carbide, SiC-Al 2 o 3 -Y 2 o 3 32 parts of nanocomposite powder, 18 parts of nickel-based tungsten carbide alloy powder, and 8 parts of Co60 cobalt-based alloy powder.
[0024] The preparation steps of above-mentioned cemented carbide material are as follows:
[0025] Put the above materials into a grinder according to the above proportions for mixing and grinding. The speed of the grinder is 100r / min, and the grinding time is 3h. After grinding, press at 520MPa, and sinter at 700°C for 25min in an argon atmosphere. After natural cooling, the cemented carbide material is obtained.
[0026] The technical parameter of the cemented carbide material that the present invention makes is as follows:
[0027]
PUM
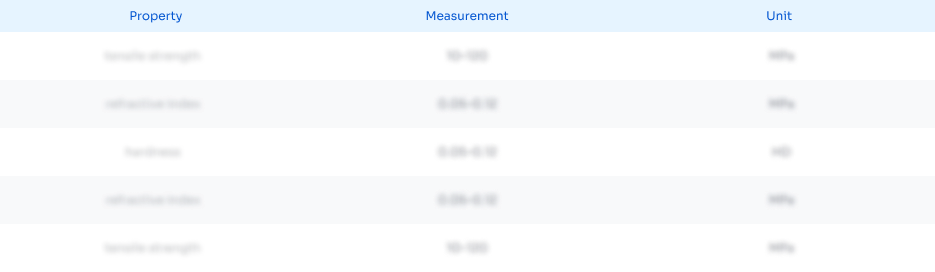
Abstract
Description
Claims
Application Information

- R&D
- Intellectual Property
- Life Sciences
- Materials
- Tech Scout
- Unparalleled Data Quality
- Higher Quality Content
- 60% Fewer Hallucinations
Browse by: Latest US Patents, China's latest patents, Technical Efficacy Thesaurus, Application Domain, Technology Topic, Popular Technical Reports.
© 2025 PatSnap. All rights reserved.Legal|Privacy policy|Modern Slavery Act Transparency Statement|Sitemap|About US| Contact US: help@patsnap.com