Wet-type fine polishing wheel and preparation method thereof
A fine polishing and wet technology, applied in the direction of grinding/polishing equipment, manufacturing tools, metal processing equipment, etc., can solve the problems of operator injury, weak self-sharpening, low elasticity, etc., and achieve super sharpness and wear resistance High degree, high elasticity and flexibility, simple preparation process
- Summary
- Abstract
- Description
- Claims
- Application Information
AI Technical Summary
Problems solved by technology
Method used
Image
Examples
preparation example Construction
[0029] A preparation method of a wet fine polishing wheel of the present invention comprises the following steps:
[0030] S1: mixing polyvinyl alcohol and distilled water in a mass ratio of 1:5, and dissolving in a water bath for 20 to 30 minutes to obtain an aqueous polyvinyl alcohol solution;
[0031] S2: Add abrasive to the polyvinyl alcohol aqueous solution, and stir evenly;
[0032] S3: add polyurethane prepolymer, epoxy modified silicone resin, catalyst and pore-forming agent to the mixed solution obtained in S2, stir evenly, and leave it to react in the mold for 10-15 minutes;
[0033] S4: curing at 50~90℃ for 2~4h;
[0034] S5: Take out the sponge-like solid obtained by curing, and perform drilling, cutting, grinding and fine grinding on it as required to obtain a finished wet polishing wheel.
[0035]Specifically, the abrasive is nano-diamond with a particle size of 0.5-10 nm. 所述的聚氨酯预聚体为TDI或者MDI的聚氨酯预聚体,可选用Bayhydur305、Bayhydur2655、Bayhydur401-7、BayhydurT0607、Bayhydu...
Embodiment 1
[0041] A kind of preparation method of wet fine polishing wheel of the present embodiment, comprises the steps:
[0042] S1: Mix 90g of polyvinyl alcohol with 450g of distilled water, dissolve in a water bath at 70°C for 20 minutes, and use a stirrer to obtain an aqueous solution of polyvinyl alcohol at a speed of 400r / min;
[0043] S2: Add 55g of nano-diamonds to the polyvinyl alcohol aqueous solution, and use a disperser to stir evenly in a 30°C water bath at a speed of 400r / min;
[0044] S3: Add 100g polyurethane prepolymer (Bayhydur305), 10g epoxy-modified silicone resin, 8g stannous octoate, 2g dibutyltin dilaurate, 5g n-pentane and 5g silicone oil to the mixed solution obtained in S2, at 30 Mix evenly in a water bath at ℃, and react for 10 minutes under stirring with a mixer at a speed of 400r / min;
[0045] S4: curing the gel solution obtained in S3 at 70°C for 2 hours;
[0046] S5: Take out the solidified spongy solid, and perform drilling, cutting, grinding, and fine...
Embodiment 2
[0049] A kind of preparation method of wet fine polishing wheel of the present embodiment, comprises the steps:
[0050] S1: Mix 110g of polyvinyl alcohol with 550g of distilled water, dissolve in a water bath at 90°C for 30 minutes, and use a stirrer to obtain an aqueous solution of polyvinyl alcohol at a speed of 600r / min;
[0051] S2: Add 65g of nano-diamonds to the polyvinyl alcohol aqueous solution, and use a disperser to stir evenly in a 60°C water bath at a speed of 600r / min;
[0052] S3: Add 120g polyurethane prepolymer (Bayhydur401-7), 15g epoxy-modified silicone resin, 12g stannous octoate, 3g dibutyltin dilaurate, 6g n-pentane, 4g silicone oil and Mix 5g of starch evenly in a water bath at 60°C, and react for 15min while stirring with a mixer at a speed of 500r / min;
[0053] S4: curing the gel solution obtained in S3 at 50°C for 4 hours;
[0054] S5: Take out the solidified spongy solid, and perform drilling, cutting, grinding, and fine grinding on it as required ...
PUM
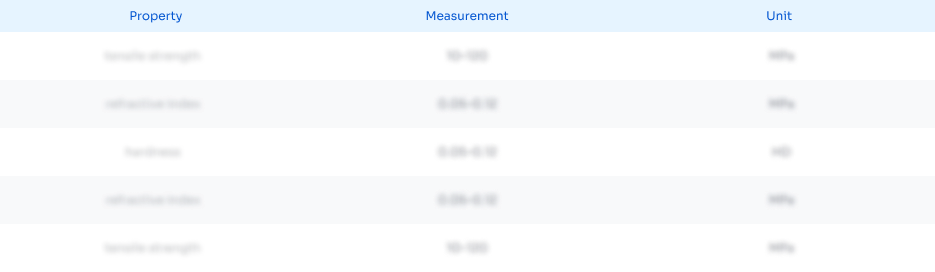
Abstract
Description
Claims
Application Information

- R&D Engineer
- R&D Manager
- IP Professional
- Industry Leading Data Capabilities
- Powerful AI technology
- Patent DNA Extraction
Browse by: Latest US Patents, China's latest patents, Technical Efficacy Thesaurus, Application Domain, Technology Topic, Popular Technical Reports.
© 2024 PatSnap. All rights reserved.Legal|Privacy policy|Modern Slavery Act Transparency Statement|Sitemap|About US| Contact US: help@patsnap.com