Titanium-iron alloy preparation method
A technology of titanium-iron alloy and vanadium-titanium magnetite, which is applied in the field of preparation of titanium-iron alloy, can solve the problems of high production cost and large aluminum consumption, and achieve the effect of reducing production cost and consumption
- Summary
- Abstract
- Description
- Claims
- Application Information
AI Technical Summary
Problems solved by technology
Method used
Image
Examples
Embodiment 1
[0021] The preparation method of the ferrotitanium alloy provided by the embodiment of the present invention 1 comprises the following steps:
[0022] (1) Carbothermal reaction
[0023] The vanadium-titanium magnetite is used as the raw material, and the coal powder is used as the reducing agent for mixing. Among them, the vanadium-titanium magnetite and coal powder are mixed according to the carbon ratio of 0.8, and then 1% bentonite is added to the mixture. Finally, mix well to form a mixture, mix the mixture with water and make pellets, wherein the mass ratio of the mixture to water is 1:0.08, put the formed wet pellets into a drying oven at 105°C for constant temperature drying, and the drying time is 5 hours. Put the dried balls obtained after drying into a heating furnace for constant temperature heating, the heating temperature is 1200°C, and the heating time is 10 minutes. The heated dry balls are taken out and airtightly cooled, and the cooled dry balls are crushed an...
Embodiment 2
[0039] The preparation method of the ferrotitanium alloy provided by the embodiment of the present invention 2 comprises the following steps:
[0040] (1) Carbothermal reaction
[0041] The vanadium-titanium magnetite is used as the raw material, and the coal powder is used as the reducing agent for mixing. Among them, the vanadium-titanium magnetite and coal powder are mixed according to the carbon ratio of 0.8, and then 1% bentonite is added to the mixture. Finally, mix well to form a mixture, mix the mixture with water and make pellets, wherein the mass ratio of the mixture to water is 1:0.08, put the formed wet pellets into a drying oven at 105°C for constant temperature drying, and the drying time is 5 hours. Put the dried balls obtained after drying into a heating furnace for constant temperature heating, the heating temperature is 1200°C, and the heating time is 10 minutes. The heated dry balls are taken out and airtightly cooled, and the cooled dry balls are crushed an...
Embodiment 3
[0052] The preparation method of the ferrotitanium alloy provided by the embodiment of the present invention 3 comprises the following steps:
[0053] (1) Carbothermal reaction
[0054] The vanadium-titanium magnetite is used as the raw material, and the coal powder is used as the reducing agent for mixing. Among them, the vanadium-titanium magnetite and coal powder are mixed according to the carbon ratio of 0.8, and then 1% bentonite is added to the mixture. After that, mix well to form a mixture, mix the mixture with water and make pellets, wherein the mass ratio of the mixture to water is 1:0.08, put the formed wet pellets into a drying oven at 105°C for constant temperature drying, and the drying time is 5 hours. Put the dried balls obtained after drying into a heating furnace for constant temperature heating, the heating temperature is 1200°C, and the heating time is 10 minutes. The heated dry balls are taken out and airtightly cooled, and the cooled dry balls are crushed...
PUM
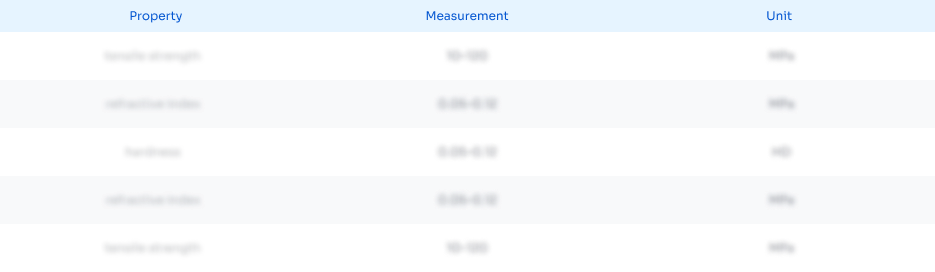
Abstract
Description
Claims
Application Information

- Generate Ideas
- Intellectual Property
- Life Sciences
- Materials
- Tech Scout
- Unparalleled Data Quality
- Higher Quality Content
- 60% Fewer Hallucinations
Browse by: Latest US Patents, China's latest patents, Technical Efficacy Thesaurus, Application Domain, Technology Topic, Popular Technical Reports.
© 2025 PatSnap. All rights reserved.Legal|Privacy policy|Modern Slavery Act Transparency Statement|Sitemap|About US| Contact US: help@patsnap.com