Titanium alloy surface processing process
A surface treatment, titanium alloy technology, applied in the direction of metal processing equipment, manufacturing tools, abrasives, etc., can solve the problems of incomplete removal of stubborn scales, improved surface wear resistance, rough surface, etc., to improve oxidation resistance and Creep performance, surface hardness improvement, surface smooth effect
- Summary
- Abstract
- Description
- Claims
- Application Information
AI Technical Summary
Problems solved by technology
Method used
Examples
Embodiment 1
[0019] A titanium alloy surface treatment process, comprising the following steps:
[0020] (1) Sand blasting: Put the titanium alloy workpiece into an environment with a relative humidity of 60% and a temperature of 50°C for 2 hours. The abrasive is cast iron sand with a particle size of 1.2mm and 0.5mm. The injection pressure when using 1.2mm abrasive 0.55MPa, and then use 0.5mm abrasive for the second injection, the injection pressure is 0.66MPa, the distance between the nozzle and the titanium alloy surface is maintained at 120mm, and the angle between the injection direction and the normal line of the titanium alloy workpiece surface is controlled at 25°;
[0021] (2) Chemical treatment: Soak the sandblasted workpiece in a solution prepared by mixing ethylenediaminetetraacetic acid, triethanolamine, sodium fluorosilicate and water for 30 minutes;
[0022] (3) Rough polishing: Roughly polish the soaked workpiece with 100-mesh sand on a polishing machine;
[0023] (4) Pier...
Embodiment 2
[0030] A titanium alloy surface treatment process, comprising the following steps:
[0031] (1) Sand blasting: Put the titanium alloy workpiece into an environment with a relative humidity of 68% and a temperature of 54°C for 2 hours. The abrasive is cast iron sand with a particle size of 1.2mm and 0.5mm. The injection pressure when using 1.2mm abrasive 0.58MPa, and then use 0.5mm abrasive for the second injection, the injection pressure is 0.69MPa, the distance between the nozzle and the titanium alloy surface is maintained at 120mm, and the angle between the injection direction and the normal line of the titanium alloy workpiece surface is controlled at 25°;
[0032] (2) Chemical treatment: Soak the sandblasted workpiece in a solution prepared by mixing ethylenediaminetetraacetic acid, triethanolamine, sodium fluorosilicate and water for 30 minutes;
[0033] (3) Rough polishing: Roughly polish the soaked workpiece with 100-mesh sand on a polishing machine;
[0034] (4) Pier...
Embodiment 3
[0041] A titanium alloy surface treatment process, comprising the following steps:
[0042] (1) Sand blasting: Put the titanium alloy workpiece into an environment with a relative humidity of 64% and a temperature of 52°C for 2 hours. The abrasive is cast iron sand with a particle size of 1.2mm and 0.5mm. The injection pressure when using 1.2mm abrasive 0.56MPa, and then use 0.5mm abrasive for the second injection, the injection pressure is 0.68MPa, the distance between the nozzle and the titanium alloy surface is maintained at 120mm, and the angle between the injection direction and the normal line of the titanium alloy workpiece surface is controlled at 25°;
[0043] (2) Chemical treatment: Soak the sandblasted workpiece in a solution prepared by mixing ethylenediaminetetraacetic acid, triethanolamine, sodium fluorosilicate and water for 30 minutes;
[0044] (3) Rough polishing: Roughly polish the soaked workpiece with 100-mesh sand on a polishing machine;
[0045] (4) Pier...
PUM
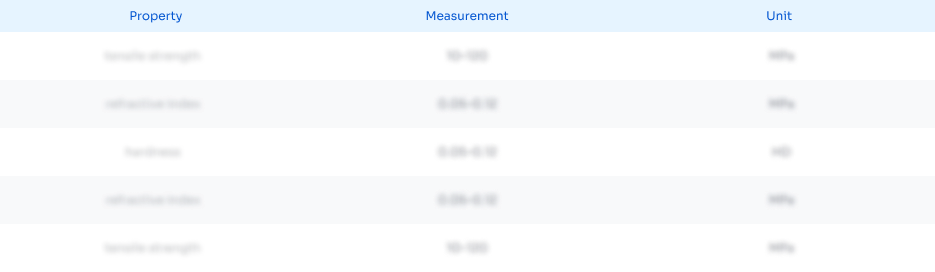
Abstract
Description
Claims
Application Information

- R&D
- Intellectual Property
- Life Sciences
- Materials
- Tech Scout
- Unparalleled Data Quality
- Higher Quality Content
- 60% Fewer Hallucinations
Browse by: Latest US Patents, China's latest patents, Technical Efficacy Thesaurus, Application Domain, Technology Topic, Popular Technical Reports.
© 2025 PatSnap. All rights reserved.Legal|Privacy policy|Modern Slavery Act Transparency Statement|Sitemap|About US| Contact US: help@patsnap.com