Thin spray powder coating and preparation method thereof
A technology of powder coating and thin spraying, which is applied in the direction of powder coating, polyester coating, epoxy resin coating, etc. It can solve the problems of affecting product quality, appearance and product function, increasing the labor intensity of staff, and decreasing the leveling degree of exposed bottom, etc. problem, to achieve the effects of shortening the baking time, strong charged particles, and reducing energy consumption
- Summary
- Abstract
- Description
- Claims
- Application Information
AI Technical Summary
Problems solved by technology
Method used
Image
Examples
Embodiment 1
[0057] Add the required raw materials for synthesizing 150kg epoxy resin in the reactor, add 0.1kg leveling agent in the reaction process, obtain the modified resin raw material; Mix the modified resin raw material with 24kg triglycidyl isocyanurate, 25kg iron yellow , 0.8kg calcium sulfate, 0.05kg brightening agent and 0.05kg benzoin are mixed and then added to the twin-screw extruder, such as Figure 1-3 As shown, the two screws of the twin-screw extruder are divided into feeding section 1, homogenizing section 2 and mixing section 3 along the material direction, and the screw in feeding section 1 is provided with threads, and the thread lead angle of the threads is 45 degrees; The screw rod of the uniform material section 2 is provided with a first screw monolith 4, the first screw monolith 4 is composed of two symmetrical teeth 40, the respective two teeth of the adjacent two first screw monoliths 4 are connected The angle between the lines is 45 degrees, and a plurality o...
Embodiment 2
[0060] Add the raw materials required for synthesizing 50kg phenolic resin in the reactor, add 2kg leveling agent in the reaction process to obtain the modified phenolic resin raw material; add the required raw materials for synthesizing 50kg propylene resin in another reactor, add in the reaction process 2kg leveling agent to obtain modified acrylic resin raw material; 34kg toluene diisocyanate, 2kg aluminum powder, 40kg talcum powder, 2kg brightening agent, 2kg benzoin, 2kg toughening agent, 2kg electrostatic agent, 2kg texture agent, 2kg alumina C , 2kg of defoamer and 2kg of cross-linking agent are mixed and added to the twin-screw extruder. The two screws of the twin-screw extruder are divided into a feeding section, a homogenizing section and a mixing section along the material direction. The screw in the feeding section Threads are provided, and the lead angle of the threads is 45 degrees; the screw of the uniform material section is provided with a first screw single pi...
Embodiment 3
[0063] Add the raw materials required for synthesizing 30kg of silicone resin in the reaction kettle, add 1kg of leveling agent in the reaction process to obtain the modified silicone resin raw material; add the required raw materials for synthesizing 30kg of polyurethane in another reaction kettle, during the reaction process Add 1kg leveling agent to obtain the modified polyurethane raw material; add the required raw materials for synthesizing 30kg fluorocarbon resin in the third reaction kettle, add 1kg leveling agent in the reaction process to obtain the modified fluorocarbon resin raw material; Glycidyl acrylate, 25kg dicyandiamide, 20kg bronze powder (pearlescent pigment), 15kg bentonite, 15kg barium sulfate, 1kg brightening agent, 1kg benzoin, 1kg hardening agent, 1kg matting agent, 1kg smooth degassing agent, 1kg Plasticizer and 1kg of micropowder wax additives are mixed and added to the twin-screw extruder. The two screws of the twin-screw extruder are divided into a f...
PUM
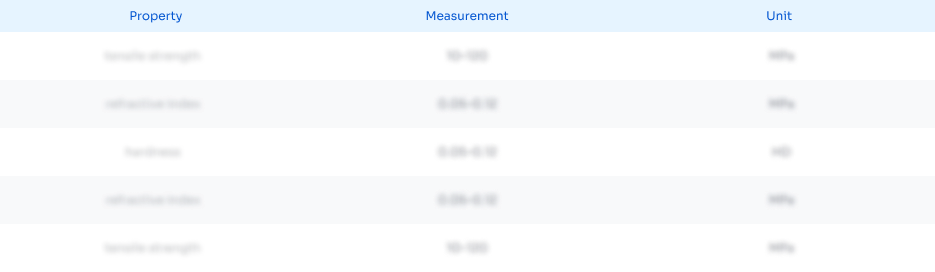
Abstract
Description
Claims
Application Information

- Generate Ideas
- Intellectual Property
- Life Sciences
- Materials
- Tech Scout
- Unparalleled Data Quality
- Higher Quality Content
- 60% Fewer Hallucinations
Browse by: Latest US Patents, China's latest patents, Technical Efficacy Thesaurus, Application Domain, Technology Topic, Popular Technical Reports.
© 2025 PatSnap. All rights reserved.Legal|Privacy policy|Modern Slavery Act Transparency Statement|Sitemap|About US| Contact US: help@patsnap.com