High temperature resistant air filtering material and preparation method thereof
An air filter material and technology of filter material, applied in the field of non-woven composite filter material, can solve the problems of fiber mesh compression resistance, insufficient compression resilience, high efficiency and low resistance, high temperature intolerant ultra-fine glass fiber material, etc. Bulkiness and anti-deformation ability, strengthen the bond strength, avoid the effect of delamination
- Summary
- Abstract
- Description
- Claims
- Application Information
AI Technical Summary
Problems solved by technology
Method used
Image
Examples
preparation example Construction
[0022] The present invention simultaneously provides a kind of preparation method of high temperature resistant air filter material, it is characterized in that comprising the following steps:
[0023] (1) Feed the glass raw material into the ultra-fine glass fiber production equipment 6, form the primary fiber 7 through melting and drawing, and the burner 8 ejects a high-temperature flame, and under the action of the air flow, the primary fiber 7 is drawn into 1-10 μm The superfine glass fiber 15, under the action of the draft negative pressure, is gathered on the web delivery curtain of the air-laid machine; at the same time, the high-temperature-resistant fiber raw material is fed into the cotton feeding box 9 through the driving roller 10, and then Under the action of the roller 13, it is further opened, and the airflow is introduced from the pipeline 11, and the high-temperature-resistant short fiber 12 is dispersed into the ultrafine glass fiber 15 by airflow transportati...
Embodiment 1
[0026] The high-temperature-resistant nonwoven fabric layer 1 is a needle-punched nonwoven fabric prepared from polyphenylene sulfide staple fibers, with a grammage of 100 g / m 2 . The high temperature-resistant short fiber intercalated ultrafine glass fiber nonwoven fabric layer 2 is a mixture of polyphenylene sulfide short fibers and ultrafine glass fibers, and the weight range is 200g / m 2 .
[0027](1) Feed the glass raw material into the ultra-fine glass fiber production equipment 6, and form the primary fiber 7 through melting and drawing. The burner 8 ejects a high-temperature flame, and under the action of the air flow, the primary fiber 7 is drawn into a 5 μm ultra-fine fiber. Fine glass fiber 15, under the action of draft negative pressure, gathers on the net conveying curtain of air-laid machine; At the same time, the polyphenylene sulfide fiber that length is 40mm, fineness is 20μm and has certain crimp passes driving roller 10 is fed into the cotton feeding box 9,...
Embodiment 2
[0031] The high-temperature-resistant nonwoven fabric layer 1 is a needle-punched nonwoven fabric prepared from polyimide staple fibers, with a grammage of 120 g / m 2 . The high-temperature-resistant short fiber intercalation ultrafine glass fiber nonwoven layer 2 is a mixture of polyimide short fiber and ultrafine glass fiber, and the weight range is 180g / m 2 .
[0032] (1) Feed the glass raw material into the ultra-fine glass fiber production equipment 6, and form the primary fiber 7 through melting and drawing. The burner 8 ejects a high-temperature flame, and under the action of the air flow, the primary fiber 7 is drawn into a 5 μm ultra-fine fiber. Fine glass fiber 15, under the effect of draft negative pressure, gathers on the net conveying curtain of air-laid machine; At the same time, the polyimide fiber that length is 45mm, fineness is 25μm and has certain crimp passes driving roller 10 is fed into the cotton feeding box 9, further opened under the action of the lic...
PUM
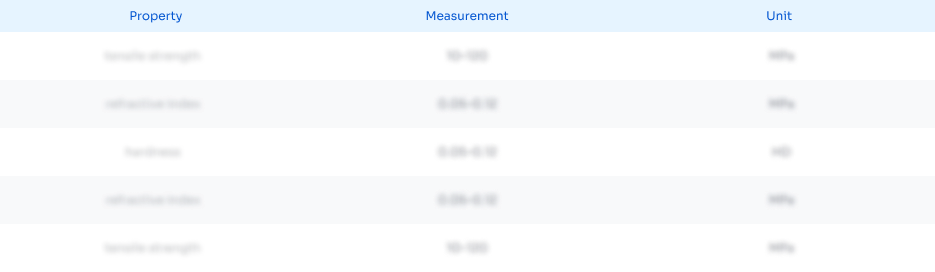
Abstract
Description
Claims
Application Information

- R&D
- Intellectual Property
- Life Sciences
- Materials
- Tech Scout
- Unparalleled Data Quality
- Higher Quality Content
- 60% Fewer Hallucinations
Browse by: Latest US Patents, China's latest patents, Technical Efficacy Thesaurus, Application Domain, Technology Topic, Popular Technical Reports.
© 2025 PatSnap. All rights reserved.Legal|Privacy policy|Modern Slavery Act Transparency Statement|Sitemap|About US| Contact US: help@patsnap.com