Preparation method of metal coated PVC (Polyvinyl Chloride) sectional material for improving plasticity
A plasticity and metal film technology, applied in the direction of rosin adhesives, adhesives, etc., can solve the problems of uneven bonding between metal and PVC, difficult continuous production, and poor adhesion of adhesives, so as to achieve plasticity Strong, solves the effect of easy aging, uniform and strong bonding
- Summary
- Abstract
- Description
- Claims
- Application Information
AI Technical Summary
Problems solved by technology
Method used
Examples
Embodiment 1
[0036] The preparation of the PVC profile with aluminum film on the surface to improve plasticity, the thickness of the aluminum film is 0.3mm, the steps are as follows:
[0037] (1) Mixing: 100kg SG-5 PVC resin powder, 10kg light calcium carbonate, 3.5kg calcium zinc stabilizer, 0.8kg stearic acid, 0.5kg calcium stearate, 0.5kg PE wax, 6kg CPE, 3kg of anti-impact ACR, 1kg of processing aid type ACR and 5kg of titanium dioxide were mixed in a high-speed mixer and the temperature was controlled at 120°C. After reaching the temperature, it was transferred to a cold mixer to cool to 40°C and discharged to obtain a mixed material;
[0038] (2) Extrusion of PVC profiles, vacuum cooling and shaping: Put the compounded materials into a 65-type conical twin-screw extruder to melt and extrude, and the temperature of the extruder is controlled at 160-205°C; after vacuum cooling and shaping, Get PVC profiles;
[0039] (3) Coating the surface of the aluminum film with hot melt adhesive: ...
Embodiment 2
[0043] The preparation of PVC profiles with a copper-clad film on the surface to improve plasticity, the thickness of the copper film is 2mm, the steps are as follows:
[0044] (1) Mixing: 100kg SG-4 PVC resin powder, 12kg active calcium carbonate, 3.8kg calcium zinc stabilizer, 0.5kg stearic acid, 0.3kg calcium stearate, 0.6kg PE wax, 3kg CPE, 3kg Impact-resistant ACR, 0.8kg of processing aid type ACR and 4kg of titanium dioxide were mixed in a high-speed mixer and controlled at a temperature of 125°C. After reaching the temperature, it was transferred to a cold mixer to cool to 45°C and discharged to obtain a mixed material;
[0045] (2) Extrusion of PVC profiles, vacuum cooling and shaping: Put the compounded materials into an 80-type conical twin-screw extruder to melt and extrude, and the temperature of the extruder is controlled at 165-200°C; after vacuum cooling and shaping, Get PVC profiles;
[0046] (3) Coating the surface of the copper film with hot melt adhesive: M...
Embodiment 3
[0050] The preparation of the PVC profiles coated with stainless steel film on the surface to improve plasticity, the thickness of the stainless steel film is 6mm, the steps are as follows:
[0051] (1) Mixing: 100kg SG-5 type PVC resin powder, 25kg active calcium carbonate, 5kg organotin stabilizer, 0.5kg stearic acid, 0.5kg calcium stearate, 1.2kg PE wax, 10kg CPE, 5kg anti Punch ACR, put 3kg of processing aid type ACR and 8kg of titanium dioxide into a high-speed mixer and mix and control the temperature at 135°C. After reaching the temperature, transfer to a cold mixer to cool to 30°C and discharge to obtain the mixed material;
[0052] (2) Extrusion of PVC profiles, vacuum cooling and shaping: Put the compounded materials into a 90-type parallel twin-screw extruder to melt and extrude, and the temperature of the extruder is controlled at 180-205°C; after vacuum cooling and shaping, the obtained PVC profiles;
[0053] (3) Coating the surface of stainless steel film with h...
PUM
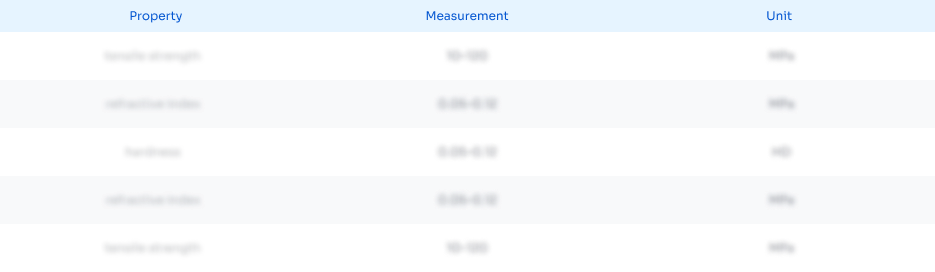
Abstract
Description
Claims
Application Information

- R&D
- Intellectual Property
- Life Sciences
- Materials
- Tech Scout
- Unparalleled Data Quality
- Higher Quality Content
- 60% Fewer Hallucinations
Browse by: Latest US Patents, China's latest patents, Technical Efficacy Thesaurus, Application Domain, Technology Topic, Popular Technical Reports.
© 2025 PatSnap. All rights reserved.Legal|Privacy policy|Modern Slavery Act Transparency Statement|Sitemap|About US| Contact US: help@patsnap.com