Boron nitride nanosheet-reinforced ceramic-based composite material and preparation method thereof
A composite material and nanosheet technology, which is applied in the field of boron nitride nanosheet reinforced ceramic matrix composites and its preparation, can solve the problems of boron nitride nanotubes that are difficult to synthesize in large quantities, hinder the effect of crack propagation, and poor high temperature stability. Achieve the effects of improving stress transfer efficiency, good product performance, and improving toughness
- Summary
- Abstract
- Description
- Claims
- Application Information
AI Technical Summary
Problems solved by technology
Method used
Image
Examples
Embodiment 1
[0047] Fused silica-based composites were prepared by hot-pressing sintering with boron nitride nanosheets as the reinforcing phase.
[0048] 1) Step: Weigh 0.06g of boron nitride nanosheets and 11.94g of fused silica powder with a balance, put them into a glass container and add 1000mL of distilled water to the container, and then use high-speed stirring and ultrasonic treatment for 8 hours to obtain uniformly dispersed suspension;
[0049] 2) step; the pH value of the two suspensions is adjusted to pH=3 by using a dilute solution of hydrochloric acid (1M), and the boron nitride nanosheet suspension is added dropwise to the fused silica suspension, while adding Still carry out high-speed stirring on the fused silica suspension to fully mix the two;
[0050] 3) step; then seal the obtained mixed solution and let it settle for 24 hours, remove the supernatant by vacuum filtration, and obtain the mixed powder after drying for 24 hours;
[0051] 4) Step: put the mixed powder in...
Embodiment 2
[0054] Fused silica-based composites were prepared by hot-pressing sintering with boron nitride nanosheets as the reinforcing phase.
[0055] 1) Step: Weigh 0.12g of boron nitride nanosheets and 11.88g of fused silica powder with a balance, put them into glass containers respectively, add 800mL of distilled water to the container, and then use high-speed stirring and ultrasonic treatment for 10 hours to obtain uniformly dispersed suspension;
[0056] 2) step; the pH value of the two suspensions is adjusted to pH=3 by using a dilute solution of hydrochloric acid (1M), and the boron nitride nanosheet suspension is added dropwise to the fused silica suspension, while adding Still carry out high-speed stirring on the fused silica suspension to fully mix the two;
[0057] 3) step: seal the obtained mixed solution and let it settle for 24 hours, remove the supernatant by vacuum filtration, and obtain the mixed powder after drying for 24 hours;
[0058] 4) Step: put the mixed powde...
Embodiment 3
[0061] Fused silica-based composites were prepared by hot-pressing sintering with boron nitride nanosheets as the reinforcing phase.
[0062] 1) Step: Weigh 0.18g of boron nitride nanosheets and 11.82g of fused silica powder with a balance, put them into a glass container and add 700mL of distilled water to the container, and then use high-speed stirring and ultrasonic treatment for 8 hours to obtain uniformly dispersed suspension;
[0063] 2) step; then adopt dilute hydrochloric acid solution (2M) to adjust the pH value of the two suspensions to pH=3.5, and add the boron nitride nanosheet suspension dropwise to the fused silica suspension, At the same time, the fused silica suspension is still stirred at high speed to fully mix the two;
[0064] 3) step; then seal the obtained mixed solution and let it stand for precipitation for 40 hours, and remove the supernatant liquid by vacuum filtration, and obtain the mixed powder after drying for 34 hours;
[0065] 4) Step: put the...
PUM
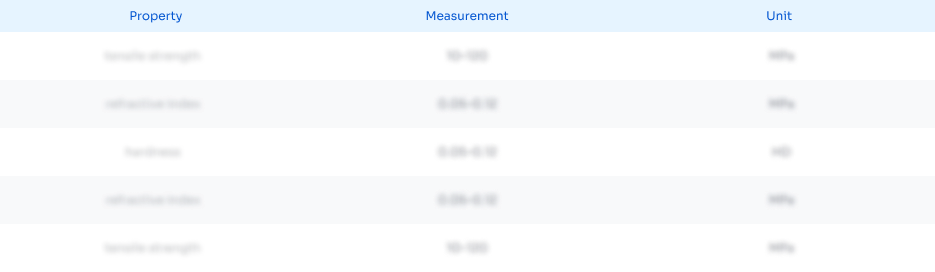
Abstract
Description
Claims
Application Information

- R&D
- Intellectual Property
- Life Sciences
- Materials
- Tech Scout
- Unparalleled Data Quality
- Higher Quality Content
- 60% Fewer Hallucinations
Browse by: Latest US Patents, China's latest patents, Technical Efficacy Thesaurus, Application Domain, Technology Topic, Popular Technical Reports.
© 2025 PatSnap. All rights reserved.Legal|Privacy policy|Modern Slavery Act Transparency Statement|Sitemap|About US| Contact US: help@patsnap.com