Paper pouring gate pipe component for casting cast steel
A sprue tube, paper-based technology, applied in the direction of casting molding equipment, casting molds, casting mold components, etc., to achieve tight connection, reduce labor intensity, and good moisture-proof and waterproof performance
- Summary
- Abstract
- Description
- Claims
- Application Information
AI Technical Summary
Problems solved by technology
Method used
Examples
Embodiment 1
[0051] Take 22.0% organic fiber [(old newspapers, old books, waste cartons, etc.) or wood pulp board by weighing according to the mass percentage. 】;
[0052] 8.0% inorganic fiber (glass fiber, aluminum silicate fiber, slag wool, rock wool, carbon fiber.); 52.0% inorganic sintered powder material (mullite, high alumina clay, attapulgite, montmorillonite, bentonite, high aluminum powder, quartz, volcanic rock, graphite.);
[0053] 13.0% inorganic thermosetting material (aluminum polyhydrogen phosphate, aluminum hydroxide, phosphoric acid, aluminum phosphate aluminum silicate.);
[0054] 2.0% binder (sodium silicate, alumina cement, gypsum, magnesium cement, silicate, phosphate, colloidal silica.);
[0055] 0.8% waterproof and moisture-proof agent (aluminum sulfate, polyvinyl alcohol, polypropylene, polyethylene.);
[0056] 1.2% enhancer and filter aid (silicate, phosphate, polyacrylamide, modified starch, carboxymethylcellulose talc, aluminum sulfate.);
[0057] 1% flux (so...
Embodiment 2
[0061] Take 20.0% organic fiber [(old newspapers, old books, waste cartons, etc.) or wood pulp board by weighing according to the mass percentage. 】;
[0062] 6.0% inorganic fiber (glass fiber, aluminum silicate fiber, slag wool, rock wool, carbon fiber.);
[0063] 58.0% inorganic sintered powder materials (mullite, high alumina clay, attapulgite, montmorillonite, bentonite, high alumina powder, quartz, volcanic rock, graphite.);
[0064] 11.0% Inorganic (organic) thermosetting materials aluminum polyhydrogen phosphate, aluminum hydroxide, phosphoric acid, aluminum phosphate aluminum silicate, phenolic resin. );
[0065] 2.0% binder (sodium silicate, alumina cement, gypsum, magnesium cement, silicate, phosphate, colloidal silica.);
[0066] 0.8% waterproof and moisture-proof agent (aluminum sulfate, polyvinyl alcohol, polypropylene, polyethylene.);
[0067] 1.2% enhancer and filter aid (silicate, phosphate, polyacrylamide, modified starch, carboxymethylcellulose talc, alum...
Embodiment 3
[0072] Take 22.0% organic fiber [(old newspapers, old books, waste cartons, etc.) or wood pulp board by weighing according to the mass percentage. 】;
[0073] 7.0% inorganic fiber (glass fiber, aluminum silicate fiber, slag wool, rock wool, carbon fiber.);
[0074] 51.0% inorganic sintered powder materials (mullite, high alumina clay, attapulgite, montmorillonite, bentonite, high alumina powder, quartz, volcanic rock, graphite.);
[0075] 14% inorganic (organic) thermosetting material (phenolic resin, aluminum polyhydrogen phosphate, aluminum hydroxide, phosphoric acid, aluminum phosphate, aluminum silicate.);
[0076] 3.0% binder (phenolic resin, modified starch, carboxymethyl fiber, polyvinyl alcohol, polyacrylamide, sodium silicate, alumina cement, silicate, phosphate, colloidal silica.);
[0077] 0.8% waterproof and moisture-proof agent (aluminum sulfate, polyvinyl alcohol, polypropylene, polyethylene.);
[0078] 1.2% enhancer and filter aid (silicate, phosphate, polyac...
PUM
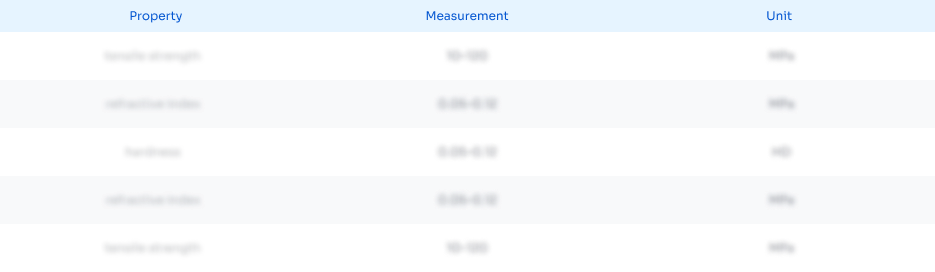
Abstract
Description
Claims
Application Information

- R&D Engineer
- R&D Manager
- IP Professional
- Industry Leading Data Capabilities
- Powerful AI technology
- Patent DNA Extraction
Browse by: Latest US Patents, China's latest patents, Technical Efficacy Thesaurus, Application Domain, Technology Topic, Popular Technical Reports.
© 2024 PatSnap. All rights reserved.Legal|Privacy policy|Modern Slavery Act Transparency Statement|Sitemap|About US| Contact US: help@patsnap.com