Filming agent used for treatment of wires processed by cold plastic deformation and preparing method thereof
A deformation processing and cold plasticity technology, applied in the direction of metal material coating process, etc., can solve the problems of low surface finish, many processes, low production efficiency, etc., and achieve short phosphating treatment time, good operation stability, and use management. simple effect
- Summary
- Abstract
- Description
- Claims
- Application Information
AI Technical Summary
Problems solved by technology
Method used
Image
Examples
Embodiment 1
[0031] Embodiment one: a kind of preparation method for the coating agent in cold plastic deformation processing wire processing, it is characterized in that completing according to the following steps:
[0032] (1) Take or measure the following raw materials according to parts by weight:
[0033]
[0034] Among them, 100 grams of zinc oxide, 100 grams of iron nitrate, 100 grams of zinc nitrate, 10 grams of nickel nitrate, 260 ml of 63% phosphoric acid, 170 ml of 98% nitric acid, and 100 ml of water.
[0035] (2) adding the zinc oxide weighed in the step (1) to the reactor, then injecting the water measured in the step (1) and stirring;
[0036] (3) Phosphoric acid and nitric acid measured in the step (1) are injected into the reactor respectively and stirred, and the material is reacted in the reactor;
[0037] (4) after above-mentioned reaction finishes, iron nitrate, nickel nitrate, zinc nitrate taken in the step (1) are injected in reactor, stir;
[0038] (5) After th...
Embodiment 2
[0040] Embodiment two: a kind of preparation method for the coating agent in cold plastic deformation processing wire processing, it is characterized in that completing according to the following steps:
[0041] (1) Take or measure the following raw materials according to parts by weight:
[0042]
[0043] Among them, 200 grams of zinc oxide, 50 grams of iron nitrate, 50 grams of zinc nitrate, 50 grams of nickel nitrate, 328 ml of 63% phosphoric acid, 136 ml of 98% nitric acid, and 150 ml of water.
[0044] (2) adding the zinc oxide weighed in the step (1) to the reactor, then injecting the water measured in the step (1) and stirring;
[0045] (3) Phosphoric acid and nitric acid measured in the step (1) are injected into the reactor respectively and stirred, and the material is reacted in the reactor;
[0046] (4) after above-mentioned reaction finishes, iron nitrate, nickel nitrate, zinc nitrate taken in the step (1) are injected in reactor, stir;
[0047] (5) After the ...
Embodiment 3
[0049] Embodiment three: according to the above-mentioned a kind of preparation method that is used for the coating agent in cold plastic deformation processing wire processing, it is characterized in that the raw material weight percentage content described in step (1) is:
[0050]
[0051] Among them, 150 grams of zinc oxide, 60 grams of iron nitrate, 80 grams of zinc nitrate, 20 grams of nickel nitrate, 328 ml of 63% phosphoric acid, 170 ml of 98% nitric acid, and 140 ml of water.
[0052] A reaction kettle used in the preparation process of a coating agent used in cold plastic deformation processing wire rod processing is made of stainless steel, and the inner surface of the reaction kettle is coated with an acid-resistant polyurethane paint coating.
[0053] The coating agents prepared in the above-mentioned Examples 1, 2, and 3 for cold plastic deformation processing of wire rods were used in practical applications, and the effects were compared with those of tradition...
PUM
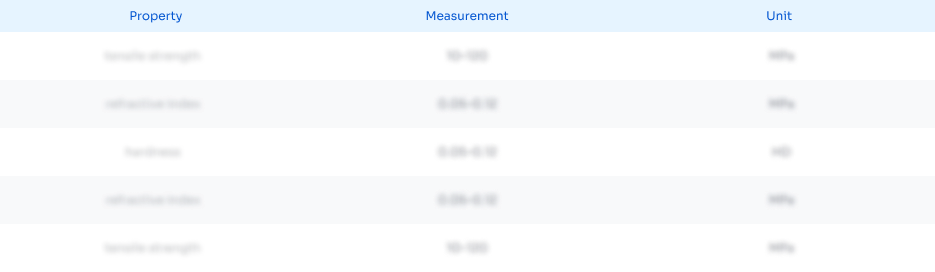
Abstract
Description
Claims
Application Information

- Generate Ideas
- Intellectual Property
- Life Sciences
- Materials
- Tech Scout
- Unparalleled Data Quality
- Higher Quality Content
- 60% Fewer Hallucinations
Browse by: Latest US Patents, China's latest patents, Technical Efficacy Thesaurus, Application Domain, Technology Topic, Popular Technical Reports.
© 2025 PatSnap. All rights reserved.Legal|Privacy policy|Modern Slavery Act Transparency Statement|Sitemap|About US| Contact US: help@patsnap.com