Synthesizing method for glufosinate-ammonium ammonium salt
A synthesis method and the technology of ammonium phosphonate, which are applied in the field of synthesis of ammonium glufosinate ammonium salt, can solve the problems of unsuitability for industrialized production, pollution and personal injury, difficulty in industrialized production, etc., and achieve production safety, easy operation, less loss, and benefit The effect of separation and purification
- Summary
- Abstract
- Description
- Claims
- Application Information
AI Technical Summary
Problems solved by technology
Method used
Image
Examples
Embodiment 1
[0036] Step 1, the preparation of dimethyl methyl phosphite: take 64g of anhydrous methanol, first pass 34g of ammonia gas into the anhydrous methanol under the condition of 10°C, then cool it down to below 10°C, Add 117g of methyl phosphorus dichloride dropwise to anhydrous methanol with ammonia gas. During the dropping process, control the temperature at 15°C. Less than 1% (reaction time about 1h), that is, dimethyl methyl phosphite;
[0037] Step 2, the preparation of methyl methoxyphosphonopropionate: mix 86g of methyl acrylate and 80g of anhydrous methanol, then heat the dimethyl methylphosphite prepared in step 1 to 50°C, Add a mixed solution of methyl acrylate and anhydrous methanol dropwise at 50-60°C, and control the dropping time for 1h. After the dropwise addition, keep warm at 60-65°C for 1h, and distill off excess methanol and by-products under reduced pressure. After methyl ether, methyl methoxyphosphonopropionate is obtained;
[0038] Step 3, the preparation o...
Embodiment 2
[0042] Step 1, the preparation of dimethyl methyl phosphite: take 64g of anhydrous methanol, first pass 34g of ammonia gas into the anhydrous methanol under the condition of 7°C, at this time, the temperature is below 10°C, Add 117g of methyl phosphorus dichloride dropwise to the anhydrous methanol, and control the temperature at 12°C during the dropwise addition. % (reaction time about 1h), that is, dimethyl methyl phosphite;
[0043] Step 2, the preparation of methyl methoxyphosphonopropionate: mix 86g of methyl acrylate and 80g of anhydrous methanol, then heat the dimethyl methylphosphite prepared in step 1 to 50°C, Add a mixed solution of methyl acrylate and anhydrous methanol dropwise at 50-60°C, and control the dropping time for 70 minutes. After the dropwise addition is completed, keep the temperature at 60-65°C for 70 minutes, and distill off excess methanol and by-products under reduced pressure. After methyl ether, methyl methoxyphosphonopropionate is obtained;
[...
Embodiment 3
[0048] Step 1, the preparation of dimethyl methyl phosphite: take 64g of anhydrous methanol, first pass 34g of ammonia gas into the anhydrous methanol under the condition of 14°C, then cool it down to below 10°C, Add 117g of methyl phosphorus dichloride dropwise to anhydrous methanol with ammonia gas. During the dropping process, control the temperature at 18°C. Less than 1% (reaction time about 1h), that is, dimethyl methyl phosphite;
[0049] Step 2, the preparation of methyl methoxyphosphonopropionate: mix 86g of methyl acrylate and 80g of anhydrous methanol, then heat the dimethyl methylphosphite prepared in step 1 to 50°C, Add a mixed solution of methyl acrylate and anhydrous methanol dropwise at 50-60°C, and control the dropping time for 50 minutes. After the dropwise addition is completed, keep the temperature at 60-65°C for 50 minutes, and distill off excess methanol and by-products under reduced pressure. After methyl ether, methyl methoxyphosphonopropionate is obtai...
PUM
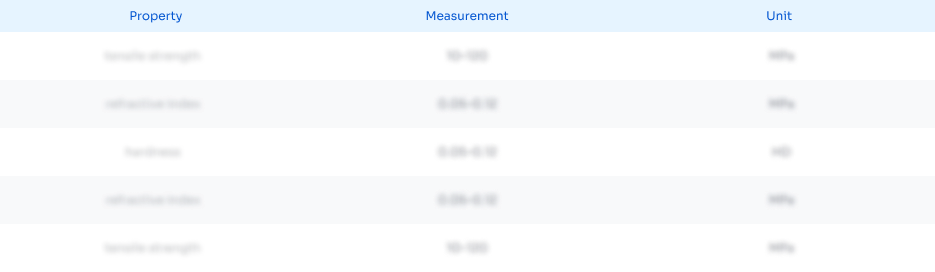
Abstract
Description
Claims
Application Information

- R&D Engineer
- R&D Manager
- IP Professional
- Industry Leading Data Capabilities
- Powerful AI technology
- Patent DNA Extraction
Browse by: Latest US Patents, China's latest patents, Technical Efficacy Thesaurus, Application Domain, Technology Topic, Popular Technical Reports.
© 2024 PatSnap. All rights reserved.Legal|Privacy policy|Modern Slavery Act Transparency Statement|Sitemap|About US| Contact US: help@patsnap.com