Porous ceramic and manufacturing process thereof
A technology of porous ceramic and low-temperature ceramic glaze powder, applied in the field of ceramic production, can solve problems such as damage to the health of users, scorched chemical substances, large thermal expansion coefficient, etc., and achieves lower defective rate, lower sintering temperature, and strong adsorption function. Effect
- Summary
- Abstract
- Description
- Claims
- Application Information
AI Technical Summary
Problems solved by technology
Method used
Examples
Embodiment 1
[0028] A kind of porous ceramics, its preparation process is as follows:
[0029] (1) Weigh each raw material in proportion, including 5% silicon carbide, 18% pottery clay, 8% mullite, 9% cordierite, 1% wollastonite, 2% spodumene, 17% low-temperature ceramic glaze powder, Mix 35% bamboo charcoal and 5% sawdust evenly and dry in an oven at 100°C for 20 hours;
[0030] (2) adding the dried raw materials to the drum mill, the weight ratio of the raw materials to the ball stones is 1:1.2, adding 0.5% oleic acid of the raw material mass as a grinding aid, and mixing by ball milling for 8 hours;
[0031] (3) cross 120 mesh sieves, so that the remaining amount of raw materials on the sieve is 0.2%, get the raw materials obtained by sieving for subsequent use;
[0032] (4) Take by weighing 20% paraffin of the total mass of raw materials and put it into a wax bucket, add oleic acid or beeswax with 5% paraffin quality, and heat to 100° C. to form a wax slurry;
[0033] (5) Slowly ad...
Embodiment 2
[0037] A kind of porous ceramics, its preparation process is as follows:
[0038](1) Weigh each raw material in proportion, including 8% silicon carbide, 12% pottery clay, 12% mullite, 15% cordierite, 5% wollastonite, 5% spodumene, 15% low-temperature ceramic glaze powder, Mix 20% bamboo charcoal and 8% sawdust evenly and dry in an oven at 120°C for 15 hours;
[0039] (2) Add the dried raw materials to the drum mill, the weight ratio of the raw materials to the ball stone is 1: 1.5, add 0.5% oleic acid of the raw material mass as a grinding aid, and mix in the ball mill for 12 hours;
[0040] (3) cross 100 mesh sieves, so that the remaining amount of raw materials on the sieve is 0.2%, get the raw materials obtained by sieving for subsequent use;
[0041] (4) Take by weighing 35% of the total mass of raw material paraffin and put it into a wax bucket, add oleic acid or beeswax with 5% of paraffin wax quality, and heat to 120°C to form wax slurry;
[0042] (5) Slowly add the ...
Embodiment 3
[0046] A kind of porous ceramics, its preparation process is as follows:
[0047] (1) Weigh each raw material in proportion, including 8% silicon carbide, 10% clay, 18% mullite, 20% cordierite, 8% wollastonite, 8% spodumene, 8% low-temperature ceramic glaze powder, Mix 10% bamboo charcoal and 10% sawdust evenly and dry in an oven at 150°C for 2 hours;
[0048] (2) adding the dried raw materials to the drum mill, the weight ratio of the raw materials to the ball stones is 1:2.0, adding 0.5% oleic acid of the raw material mass as a grinding aid, and mixing by ball milling for 20 hours;
[0049] (3) cross 100 mesh sieves, so that the remaining amount of raw materials on the sieve is 0.2%, get the raw materials obtained by sieving for subsequent use;
[0050] (4) Take by weighing 60% of the total mass of raw material paraffin and put it into a wax bucket, add oleic acid or beeswax with 5% of paraffin wax quality, and heat to 160°C to form wax slurry;
[0051] (5) Slowly add the ...
PUM
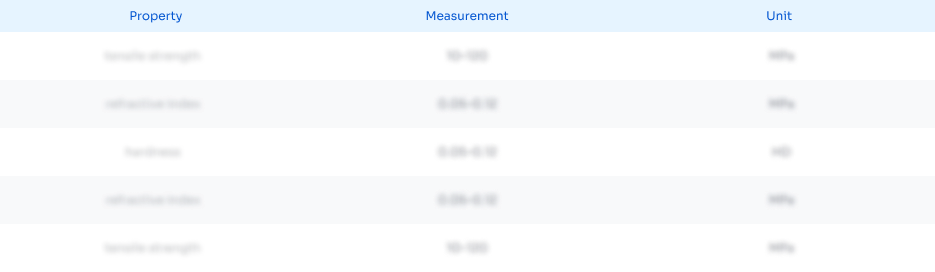
Abstract
Description
Claims
Application Information

- R&D
- Intellectual Property
- Life Sciences
- Materials
- Tech Scout
- Unparalleled Data Quality
- Higher Quality Content
- 60% Fewer Hallucinations
Browse by: Latest US Patents, China's latest patents, Technical Efficacy Thesaurus, Application Domain, Technology Topic, Popular Technical Reports.
© 2025 PatSnap. All rights reserved.Legal|Privacy policy|Modern Slavery Act Transparency Statement|Sitemap|About US| Contact US: help@patsnap.com