Glass steel tile back and production process thereof
A production process and glass fiber reinforced plastic technology, applied in the field of glass fiber reinforced plastic tile back and its production process, can solve the problems of low strength, poor corrosion resistance, etc., and achieve the effect of extending service life, excellent corrosion resistance and high temperature resistance, and long service life
- Summary
- Abstract
- Description
- Claims
- Application Information
AI Technical Summary
Problems solved by technology
Method used
Image
Examples
Embodiment 1
[0042] The production process of the glass fiber reinforced plastic tile back provided by the present embodiment comprises the following steps:
[0043] (1) carbon fiber 15Kg is mixed with non-alkali glass fiber 20Kg, basalt fiber 5Kg and is placed in the lower mold in the mold with tile back shape after being mixed, closes mold on described lower mold loam cake;
[0044] (2) Add iron powder 10Kg, dioctyl phthalate 10Kg, T31 epoxy resin curing agent 4Kg, decabromodiphenyl ether 10Kg, RX-80 resin 2Kg, carbon black 16Kg and quartz powder 20Kg to the molten The slurry is formed in 95Kg of epoxy resin, and then the slurry is injected into the mold through the glue injection port of the upper mold, kept at 110 ° C for 6 minutes, and demoulded to obtain a semi-finished product;
[0045] (3) After the semi-finished product is polished and deburred, the fiberglass tile back is obtained.
Embodiment 2
[0047] The production process of the glass fiber reinforced plastic tile back provided by the present embodiment comprises the following steps:
[0048] (1) carbon fiber 20Kg is mixed with non-alkali glass fiber 10Kg, basalt fiber 10Kg and placed in the lower mold in the mold with tile back shape after being mixed, closes the upper mold on described lower mold loam cake;
[0049] (2) 12.5Kg of copper powder, 6Kg of diisodecyl phthalate, 8Kg of amine-105 epoxy resin curing agent, 15Kg of tetrabromobisphenol A, 4,4'-bismaleimide diphenyl Add 1Kg of methane, 20Kg of carbon black and 20Kg of moissanite powder into 80Kg of molten epoxy resin to form a slurry, then inject the slurry into the mold through the injection port of the upper mold, and keep warm at 150°C Curing for 4 minutes, demoulding to obtain a semi-finished product;
[0050] (3) After the semi-finished product is polished and deburred, the glass fiber reinforced plastic tile back is obtained.
Embodiment 3
[0052] The production process of the glass fiber reinforced plastic tile back provided by the present embodiment comprises the following steps:
[0053] (1) carbon fiber 17Kg is mixed with non-alkali glass fiber 18Kg, basalt fiber 6.5Kg and placed in the lower mold in the mold with tile back shape after being mixed, closes mold on described lower mold loam cake;
[0054] (2) Add 8Kg of iron powder, 5Kg of copper powder, 9Kg of dibutyl phthalate, 5.8Kg of methyl ethyl ketone peroxide, 13Kg of microencapsulated red phosphorus, 1.4Kg of 203 resin, 30Kg of carbon black and 8Kg of quartz powder into Form a slurry in 100Kg of molten epoxy resin, then inject the slurry into the mold through the injection port of the upper mold, heat and solidify at 125°C for 8 minutes, and demould to obtain a semi-finished product;
[0055] (3) After the semi-finished product is polished and deburred, the fiberglass tile back is obtained.
PUM
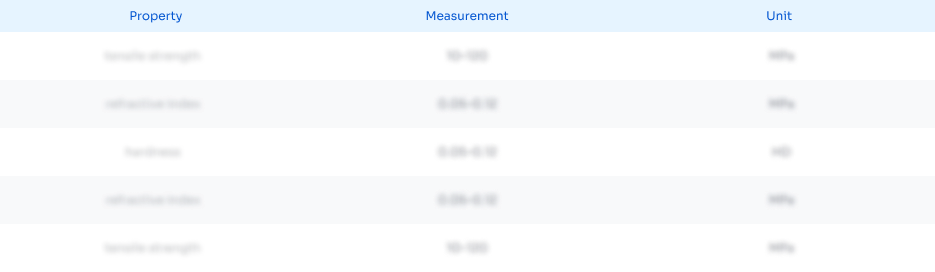
Abstract
Description
Claims
Application Information

- R&D Engineer
- R&D Manager
- IP Professional
- Industry Leading Data Capabilities
- Powerful AI technology
- Patent DNA Extraction
Browse by: Latest US Patents, China's latest patents, Technical Efficacy Thesaurus, Application Domain, Technology Topic, Popular Technical Reports.
© 2024 PatSnap. All rights reserved.Legal|Privacy policy|Modern Slavery Act Transparency Statement|Sitemap|About US| Contact US: help@patsnap.com