Low-odor, low-emission, high abrasion-resistant and high-temperature-resistant nylon and preparing method thereof
A technology with high temperature resistance and low emission, applied in the polymer field, it can solve the problems affecting the adhesion between the wear-resistant modifier and the high temperature resistant nylon matrix, the mechanical properties of the composite material, the viscosity and density of the composite material, etc. The effect of unaffected processing properties, excellent mechanical properties, and low water absorption
- Summary
- Abstract
- Description
- Claims
- Application Information
AI Technical Summary
Problems solved by technology
Method used
Examples
Embodiment 1
[0031] (1) Surface treatment of nano-silicon carbide: add nano-silicon carbide to a mixed solution composed of ammonia water and tetraethyl orthosilicate at a mass ratio of 2:1, and react at 60°C for 6 hours to obtain a mixed solution; Add 0.5% of the coupling agent γ-aminopropyl triethoxysilane to the liquid, react at 70°C for 2 hours, wash with deionized water repeatedly after centrifugation, and finally dry to obtain orthosilicon Nano-silicon carbide surface treated with ethyl acetate and coupling agent composite;
[0032] (2) Preparation of hydrophobic high temperature resistant odor adsorption masterbatch: 49 parts of nylon 6T, 15 parts of hydrophobic diatomaceous earth, 10 parts of hydrophobic activated carbon, 10 parts of acicular zeolite molecular sieve, 10 parts of zinc ricinoleate, polymer quarter 5 parts of ammonium salt grafted nano silica, 5,7-bis-(2,2-dimethylethyl)-3-(3,4-dimethylphenyl)-2-3hydrogen-benzo Add 0.1 part of furanone, 0.4 part of antioxidant H10, a...
Embodiment 2
[0036] (1) Surface treatment of nano-silicon carbide: Add nano-silicon carbide to a mixed solution composed of ammonia water and tetraethyl orthosilicate at a mass ratio of 2:1, and react at 50°C for 8 hours to obtain a mixed solution; The coupling agent γ-aminopropyltriethoxysilane with 1% of the mass of nano-silicon carbide was reacted at 80°C for 2 hours, washed repeatedly with deionized water after centrifugation, and finally dried to obtain ethyl orthosilicate and coupling Nano-silicon carbide with joint agent composite surface treatment;
[0037] (2) Preparation of hydrophobic high temperature resistant odor adsorption masterbatch: 49 parts of nylon 6T, 15 parts of hydrophobic diatomaceous earth, 10 parts of hydrophobic activated carbon, 10 parts of acicular zeolite molecular sieve, 10 parts of zinc ricinoleate, polymer quarter 5 parts of ammonium salt grafted nano silica, 5,7-bis-(2,2-dimethylethyl)-3-(3,4-dimethylphenyl)-2-3hydrogen-benzo Add 0.1 part of furanone, 0.4...
Embodiment 3
[0041](1) Surface treatment of nano-silicon carbide: add nano-silicon carbide to a mixed solution composed of ammonia water and tetraethyl orthosilicate at a mass ratio of 2:1, and react at 80°C for 5 hours to obtain a mixed solution; The 1.5% coupling agent γ-aminopropyltriethoxysilane of nano-silicon carbide mass was reacted at 70°C for 5 hours, washed repeatedly with deionized water after centrifugation, and finally dried to obtain ethyl orthosilicate and coupling Nano-silicon carbide with joint agent composite surface treatment;
[0042] (2) Preparation of hydrophobic high temperature resistant odor adsorption masterbatch: 49 parts of nylon 6T, 15 parts of hydrophobic diatomaceous earth, 10 parts of hydrophobic activated carbon, 10 parts of acicular zeolite molecular sieve, 10 parts of zinc ricinoleate, polymer quarter 5 parts of ammonium salt grafted nano silica, 5,7-bis-(2,2-dimethylethyl)-3-(3,4-dimethylphenyl)-2-3hydrogen-benzo Add 0.1 part of furanone, 0.2 part of co...
PUM
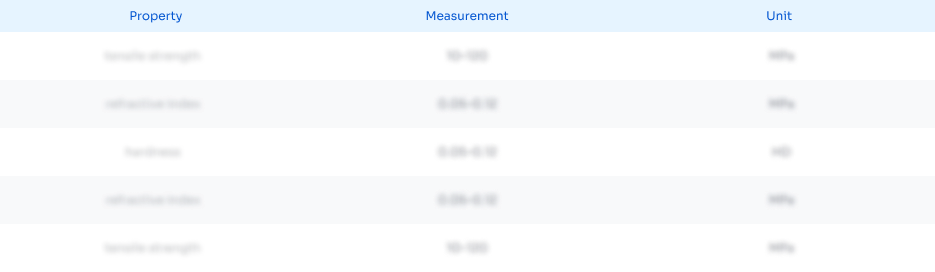
Abstract
Description
Claims
Application Information

- R&D
- Intellectual Property
- Life Sciences
- Materials
- Tech Scout
- Unparalleled Data Quality
- Higher Quality Content
- 60% Fewer Hallucinations
Browse by: Latest US Patents, China's latest patents, Technical Efficacy Thesaurus, Application Domain, Technology Topic, Popular Technical Reports.
© 2025 PatSnap. All rights reserved.Legal|Privacy policy|Modern Slavery Act Transparency Statement|Sitemap|About US| Contact US: help@patsnap.com