Synthesis method of molybdenum disulfide/carbon nano composite material
A composite material, molybdenum disulfide technology, applied in chemical instruments and methods, nanotechnology, nanotechnology, etc., can solve the problems that the product performance is difficult to meet the application requirements, and the preparation steps are cumbersome.
- Summary
- Abstract
- Description
- Claims
- Application Information
AI Technical Summary
Problems solved by technology
Method used
Image
Examples
Embodiment 1
[0010] Embodiment 1, configure 0.25M (NH 4 ) 6 Mo 7 o 24 4H 2 O solution 40ml, then add 2g of potassium humate, and then configure 0.5M HNO 3 Solution 100ml. Under the condition of magnetic stirring, the (NH 4 ) 6 Mo 7 o 24 4H 2 The mixed solution of O and refined potassium humate was slowly added dropwise to HNO 3 in solution. After the above turbid liquid is left to stand, suck out the water in the upper layer, then freeze-dry the precipitate, take 1g of freeze-dried potassium humate-molybdic acid precursor and 10g of anhydrous sodium sulfate in a mass ratio of 1:10 Mix and grind, then roast in an Ar gas atmosphere at 600°C for 3 hours at a temperature gradient of 10°C / min, cool down to room temperature naturally, then wash the sample five times with water and ethanol, and finally store the sample in ethanol , drying at 50°C to obtain molybdenum sulfide / carbon nanocomposites
Embodiment 2
[0011] Embodiment 2, configure 0.25M (NH 4 ) 6 Mo 7 o 24 4H 2 O solution 40ml, then add 2g of potassium humate, and then configure 0.5M HNO 3 Solution 100ml. Under the condition of magnetic stirring, the (NH 4 ) 6 Mo 7 o 24 4H 2 The mixed solution of O and refined potassium humate was slowly added dropwise to HNO 3 in solution. After the above turbid liquid is left to stand, suck out the water in the upper layer, then freeze-dry the precipitate, take 1g of freeze-dried potassium humate-molybdic acid precursor and 10g of anhydrous sodium sulfate in a mass ratio of 1:10 Mix and grind, then roast in an Ar gas atmosphere at 700°C for 3 hours at a temperature gradient of 10°C / min, cool down to room temperature naturally, wash the sample five times with water and ethanol, and finally store the sample in ethanol , and dried at 50°C to obtain molybdenum sulfide / carbon nanocomposites.
Embodiment 3
[0012] Embodiment 3, configure 0.25M (NH 4 ) 6 Mo 7 o 24 4H 2 O solution 40ml, then add 2g of potassium humate, and then configure 0.5M HNO 3 Solution 100ml. Under the condition of magnetic stirring, the (NH 4 ) 6 Mo 7 o 24 4H 2 The mixed solution of O and refined potassium humate was slowly added dropwise to HNO 3 in solution. After the above turbid liquid is left to stand, suck out the water in the upper layer, then freeze-dry the precipitate, take 1g of freeze-dried potassium humate-molybdic acid precursor and 10g of anhydrous sodium sulfate in a mass ratio of 1:10 Mix and grind, then roast in an Ar gas atmosphere at 800°C for 3 hours at a temperature gradient of 10°C / min, cool down to room temperature naturally, and then wash the sample five times with water and ethanol, respectively, and finally store the sample in ethanol , and dried at 50°C to obtain molybdenum sulfide / carbon nanocomposites.
[0013] Potassium humate used in the above experiments was purcha...
PUM
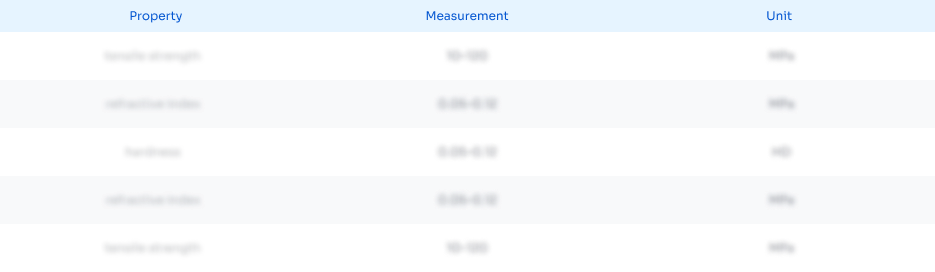
Abstract
Description
Claims
Application Information

- R&D
- Intellectual Property
- Life Sciences
- Materials
- Tech Scout
- Unparalleled Data Quality
- Higher Quality Content
- 60% Fewer Hallucinations
Browse by: Latest US Patents, China's latest patents, Technical Efficacy Thesaurus, Application Domain, Technology Topic, Popular Technical Reports.
© 2025 PatSnap. All rights reserved.Legal|Privacy policy|Modern Slavery Act Transparency Statement|Sitemap|About US| Contact US: help@patsnap.com