Grain boundary diffusion method for neodymium-iron-boron magnet
A grain boundary diffusion, NdFeB technology, applied in magnetic objects, magnetic materials, inductance/transformer/magnet manufacturing, etc., can solve the problem of incremental discount of coercive force, reduce remanence, improve uniformity, improve The effect of magnet coercivity
- Summary
- Abstract
- Description
- Claims
- Application Information
AI Technical Summary
Problems solved by technology
Method used
Examples
Embodiment 1
[0025] Grain boundary powder Nd of low melting point rare earth alloy 70 Cu 30 It is prepared by rare earth alloy powder metallurgy process (quick solidification-hydrogen breaking-high energy ball milling), and the average powder particle size is 2.5μm. 1wt% Nd 70 Cu 30 Incorporation (PrNd) 30 Fe bal Al 0.1 Cu 0.1 Zr 0.1 B main phase alloy powder, mixed evenly, oriented in a magnetic field to form a rough magnet, put into a vacuum sintering furnace for sintering at 1050°C, and tempering at 900°C+500°C for 4 hours.
Embodiment 2
[0027] The composition ratio of the main phase alloy is (PrNd) 30 Fe bal Al 0.1 Cu 0.1 Zr 0.1 B, made by quick-setting process, followed by hydrogen breaking and jet milling, the average powder particle size is 3.5μm. Orientation molding in a magnetic field to make a rough magnet, put it into a vacuum sintering furnace and sinter at 1050°C, process it into a sample column with a thickness of 1.6cm, and electrophoresis coat a layer of low melting point rare earth alloy Nd on the surface of the sintered rough magnet. 70 Cu 30 , after vacuum drying, put them in a sintering furnace for tempering heat treatment at 900°C+500°C, and the tempering time is 4h.
Embodiment 3
[0029] Grain boundary powder Nd of low melting point rare earth alloy 70 Cu 30 It is prepared by rare earth alloy powder metallurgy process (quick solidification-hydrogen breaking-high energy ball milling), and the average powder particle size is 2.5μm. 1wt% Nd 70 Cu 30 Incorporation (PrNd) 30 Fe bal Al 0.1 Cu 0.1 Zr 0.1 B main phase alloy powder, mixed evenly, oriented in a magnetic field to form a rough magnet, put into a vacuum sintering furnace and sintered at 1050°C respectively, processed into a sample column with a thickness of 1.6cm, electrophoretic coating on the surface of the sintered rough magnet Coated with a layer of low melting point rare earth alloy Nd 70 Cu 30 , after vacuum drying, put them in a sintering furnace for tempering heat treatment at 900°C+500°C, and the tempering time is 4h.
[0030] The comparison of magnetic properties of the magnets prepared in Comparative Example 1, Example 1, Example 2, and Example 3 is shown in Table 1.
[0031] T...
PUM
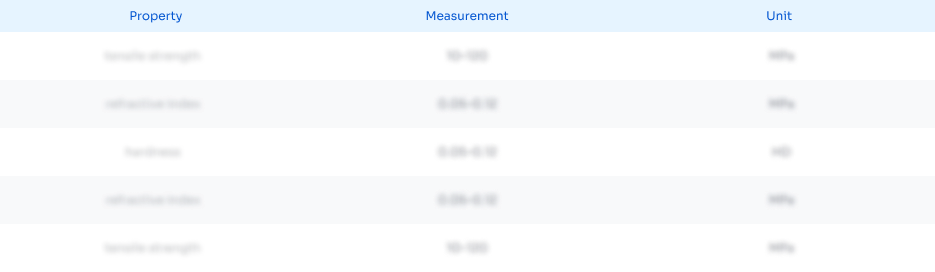
Abstract
Description
Claims
Application Information

- R&D
- Intellectual Property
- Life Sciences
- Materials
- Tech Scout
- Unparalleled Data Quality
- Higher Quality Content
- 60% Fewer Hallucinations
Browse by: Latest US Patents, China's latest patents, Technical Efficacy Thesaurus, Application Domain, Technology Topic, Popular Technical Reports.
© 2025 PatSnap. All rights reserved.Legal|Privacy policy|Modern Slavery Act Transparency Statement|Sitemap|About US| Contact US: help@patsnap.com