ABS/carbon fiber composite material suitable for 3D printing
A composite material, 3D printing technology, applied in the field of 3D printing, can solve the problems of difficult processing, heavy processing odor, high material cost, and achieve the effect of improving comprehensive mechanical properties, increasing material compatibility, and broad market prospects.
- Summary
- Abstract
- Description
- Claims
- Application Information
AI Technical Summary
Problems solved by technology
Method used
Examples
Embodiment 1
[0016] (1) A composite material suitable for 3D printing, comprising the following parts by weight: PLA: 40.0 parts; ABS: 40.0 parts; carbon fiber: 20.0 parts; ABS high-glue powder: 8 parts; compatibilizer: 0.2 parts; Agent: 0.4 part; Described compatibilizer comprises maleic acid phenol graft macromolecule, is formed by the terpolymer (SAG) of styrene, acrylonitrile, glycidyl methacrylate copolymerization; One or two or more compatibilizers in the terpolymer formed by copolymerization of vinegar, butadiene and styrene copolymer are used together.
[0017] (2) The compatibilizer maleic acid grafted polymer includes maleic acid grafted ABS.
[0018] (3) heat stabilizer is one or more in phosphite esters, calcium zinc stabilizer; Described lubricant is one or more in ethylene bis stearic acid amide, zinc stearate, calcium stearate Several kinds; the dispersant is one or more of sodium methylene bis-naphthalene sulfonate, stearic acid, and oxidized polyethylene wax.
Embodiment 2
[0020] (1) A composite material suitable for 3D printing, comprising the following components by weight: PLA: 45.0 parts; ABS: 45.0 parts; carbon fiber: 10.0 parts; ABS high-glue powder: 4 parts; compatibilizer: 0.2-5.0 parts ; Auxiliary agent: 0.1-2.0 parts; The compatibilizer includes maleic acid phenol grafted macromolecules, a terpolymer (SAG) formed by copolymerization of styrene, acrylonitrile, glycidyl methacrylate; One or two or more compatibilizers in the terpolymer formed by copolymerization of methyl methacrylate, butadiene and styrene copolymer are used together.
[0021] (2) The maleic acid grafted polymer includes maleic acid grafted ABS.
[0022] (3) The auxiliary agent includes one or more mixtures of lubricant, nucleating agent, dispersant, thermal oxygen stabilizer;
[0023] (4) The thermal oxygen stabilizer is one or more compounds of hindered phenols, phosphites, and calcium-zinc stabilizers; the lubricant is 0.2 parts of calcium stearate and 0.4 parts of ...
PUM
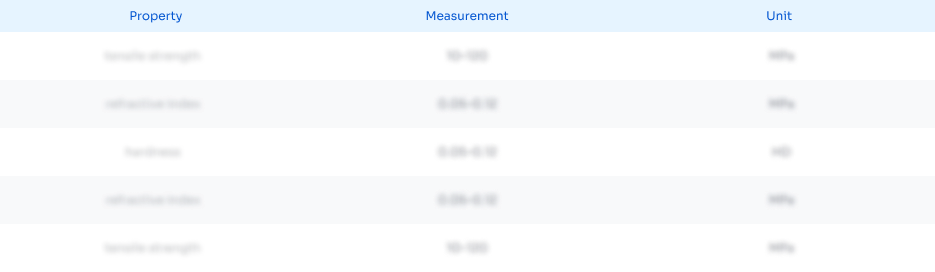
Abstract
Description
Claims
Application Information

- R&D
- Intellectual Property
- Life Sciences
- Materials
- Tech Scout
- Unparalleled Data Quality
- Higher Quality Content
- 60% Fewer Hallucinations
Browse by: Latest US Patents, China's latest patents, Technical Efficacy Thesaurus, Application Domain, Technology Topic, Popular Technical Reports.
© 2025 PatSnap. All rights reserved.Legal|Privacy policy|Modern Slavery Act Transparency Statement|Sitemap|About US| Contact US: help@patsnap.com