Manufacturing method of polyester fiber for industry
A polyester fiber and manufacturing method technology, applied in the field of textile fiber manufacturing, can solve the problems of high strength and high modulus of difficult materials, large molding shrinkage, poor dimensional stability, etc., and achieve increased flexibility and movement ability, high strength and Modulus, effect of excellent impact resistance
- Summary
- Abstract
- Description
- Claims
- Application Information
AI Technical Summary
Problems solved by technology
Method used
Examples
Embodiment 1
[0027]Embodiment 1: a kind of manufacture method of industrial polyester fiber, adopt following steps:
[0028] A) According to the number of parts by mass, 1 part of organic calcium carbonate whiskers with a characteristic parameter diameter of 0.5um and a length of 5um, 1 part of organic wollastonite nanoacicular fibers with an aspect ratio of 14:0.5, and 1 part Organic barium sulfate nanopowder, mixed with 65 parts of ethylene glycol, 8 parts of 1,3-propanediol, 8 parts of 1,4-butanediol, 6 parts of p-hydroxybenzoic acid and 0.1 part of sodium germanate, the mixed solution was at 70 ℃ stirring ball mill airtight grinding reaction for 2 hours to obtain a high-strength and high-modulus compound alcohol solution, which is kept at 70 ℃ for use;
[0029] B) According to the number of parts by mass, 1 part of organic magnesium hydroxide whisker with a characteristic parameter diameter of 0.2um and a length of 10um, 1 part of 800 mesh mica powder, 10 parts of polyethylene glycol P...
Embodiment 2
[0032] Embodiment 2: a kind of manufacture method of industrial polyester fiber, adopt following steps:
[0033] A) According to the number of parts by mass, 1.5 parts of organic calcium carbonate whiskers whose characteristic parameters are 1.75um in diameter and 17.5um in length, 1.5 parts of organic wollastonite nanoacicular fibers with an aspect ratio of 15:1, 1.5 parts Parts of organic barium sulfate nanopowder, 70 parts of ethylene glycol, 6 parts of 1,3-propanediol, 6 parts of 1,4-butanediol, 5 parts of p-hydroxybenzoic acid, 0.2 parts of sodium germanate are mixed, and the mixed solution is in 70°C stirring ball mill airtight grinding reaction for 3 hours to obtain a high-strength and high-modulus complex alcohol solution, keep it warm at 70°C for use;
[0034] B) According to the number of parts by mass, 1.5 parts of organic magnesium hydroxide whiskers with a characteristic parameter diameter of 2.6um and a length of 17.5um, 1.5 parts of 800 mesh mica powder, 9 parts...
Embodiment 3
[0037] Embodiment 3: a kind of manufacture method of industrial polyester fiber, adopt following steps:
[0038] A) According to the number of parts by mass, 2 parts of organic calcium carbonate whiskers whose characteristic parameters are 3um in diameter and 20um in length, 2 parts of organic wollastonite nanoacicular fibers with an aspect ratio of 16:1.5, 2 parts of organic Mix barium sulfate nanopowder with 75 parts of ethylene glycol, 5 parts of 1,3-propanediol, 5 parts of 1,4-butanediol, 4 parts of p-hydroxybenzoic acid, and 0.3 parts of sodium germanate. The mixed solution is kept at 70°C Stir the ball mill to grind in a sealed manner for 4 hours to obtain a high-strength and high-modulus complex alcohol solution, which is kept at 70°C for use;
[0039] B) According to the number of parts by mass, 2 parts of organic magnesium hydroxide whiskers with a characteristic parameter diameter of 5um and a length of 25um, 2 parts of 800 mesh mica powder, 8 parts of polyethylene g...
PUM
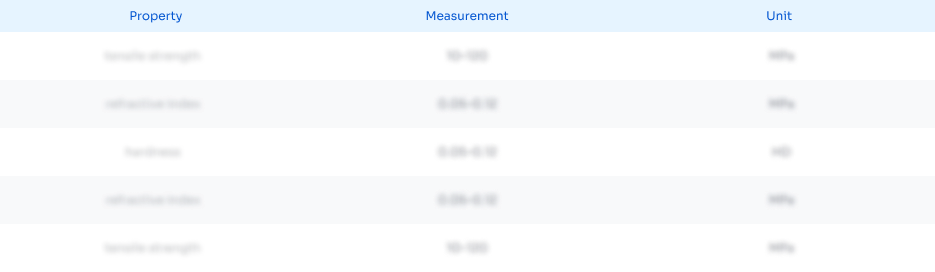
Abstract
Description
Claims
Application Information

- Generate Ideas
- Intellectual Property
- Life Sciences
- Materials
- Tech Scout
- Unparalleled Data Quality
- Higher Quality Content
- 60% Fewer Hallucinations
Browse by: Latest US Patents, China's latest patents, Technical Efficacy Thesaurus, Application Domain, Technology Topic, Popular Technical Reports.
© 2025 PatSnap. All rights reserved.Legal|Privacy policy|Modern Slavery Act Transparency Statement|Sitemap|About US| Contact US: help@patsnap.com