Ceramic substrate copper cladding low-temperature connection method for power module
A technology for ceramic substrates and power modules, applied in welding media, welding equipment, welding/welding/cutting items, etc., can solve problems such as low yield, lower surface flatness requirements, narrow process window, etc., to improve service life, The effect of lowering the connection temperature and reducing the residual stress
- Summary
- Abstract
- Description
- Claims
- Application Information
AI Technical Summary
Problems solved by technology
Method used
Image
Examples
Embodiment 1
[0019] (1) Grind the surface of AlN ceramics with 1000# and 1500# diamond sand discs in turn, and polish the surface of oxygen-free copper with 800#, 1000# and 2000# sandpaper in turn, and then put the polished samples into acetone Ultrasonic cleaning for 15 minutes;
[0020] (2) Put Ag powder, Cu powder, Sn powder, Ti powder, and organic binder into a ball mill tank for mechanical ball milling of active solder paste. The mass fraction of Ag is 10%, the mass fraction of Cu is 20%, the mass fraction of Sn is 65%, the mass fraction of Ti is 5%, the mass ratio of organic binder to metal powder is 1:6, and the mechanical ball milling time for 6 hours;
[0021] (3) Coat 50 μm of active solder paste on the surface of AlN ceramics, then attach 0.3 mm thick oxygen-free copper to AlN, with solder paste in the middle, and apply a pressure of 15 MPa above the oxygen-free copper. Put the assembled sample into the brazing furnace, evacuate to 5×10-3Pa, then heat to 750ºC at a rate of 15º...
Embodiment 2
[0023] (1) Use 1000# and 1500# diamond sand discs in sequence to Al 2 o 3 The ceramic surface is polished, and the oxygen-free copper surface is polished with 800#, 1000# and 2000# sandpaper in sequence, and then the polished sample is ultrasonically cleaned in acetone for 20 minutes;
[0024] (2) Put Ag powder, Cu powder, Sn powder, Ti powder, and organic binder into a ball mill tank for mechanical ball milling of active solder paste. The mass fraction of Ag is 5%, the mass fraction of Cu is 30%, the mass fraction of Sn is 61%, the mass fraction of Ti is 4%, the mass ratio of organic binder to metal powder is 1:4, and the mechanical ball milling time for 8 hours;
[0025] (3) Coat 100μm of active solder paste on the surface of Al2O3 ceramics, then attach 0.5mm thick oxygen-free copper to Al2O3, with solder paste in the middle, and apply 15MPa pressure above the oxygen-free copper. Put the assembled sample into the brazing furnace, evacuate to 2×10-3Pa, then heat to 720ºC a...
Embodiment 3
[0027] (1) Grind the surface of AlN ceramics with 1000# and 1500# diamond sand discs in turn, and polish the surface of oxygen-free copper with 800#, 1000# and 2000# sandpaper in turn, and then put the polished samples into acetone Ultrasonic cleaning for 20 minutes;
[0028] (2) Put Ag powder, Cu powder, Sn powder, Ti powder, and organic binder into a ball mill tank for mechanical ball milling of active solder paste. The mass fraction of Ag is 5%, the mass fraction of Cu is 30%, the mass fraction of Sn is 61%, the mass fraction of Ti is 4%, the mass ratio of organic binder to metal powder is 1:4, and the mechanical ball milling time for 8 hours;
[0029] (3) Coat 100 μm of active solder paste on the surface of AlN ceramics, then attach 0.3 mm thick oxygen-free copper to AlN, with solder paste in the middle, and apply a pressure of 15 MPa above the oxygen-free copper. Put the assembled sample into the brazing furnace, evacuate to 5×10-3Pa, then heat to 720ºC at a rate of 20º...
PUM
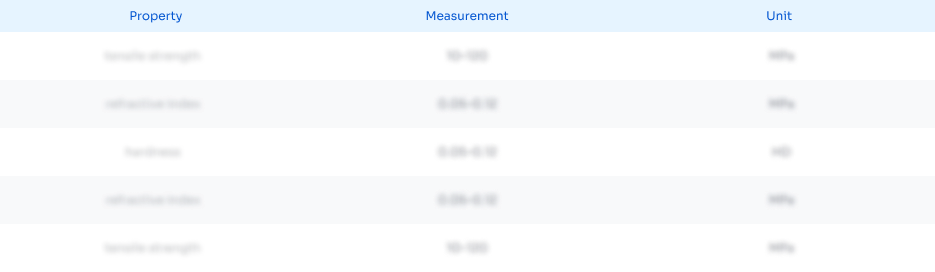
Abstract
Description
Claims
Application Information

- R&D
- Intellectual Property
- Life Sciences
- Materials
- Tech Scout
- Unparalleled Data Quality
- Higher Quality Content
- 60% Fewer Hallucinations
Browse by: Latest US Patents, China's latest patents, Technical Efficacy Thesaurus, Application Domain, Technology Topic, Popular Technical Reports.
© 2025 PatSnap. All rights reserved.Legal|Privacy policy|Modern Slavery Act Transparency Statement|Sitemap|About US| Contact US: help@patsnap.com