Recycling method for zinc smelting nickel and cobalt slag
A technology for smelting nickel-cobalt slag and zinc, which is applied in photography technology, instruments, photography auxiliary technology and other directions, can solve the problems of large one-time investment, high production cost, and the loss outweighs the gain, so as to simplify the production process, save the production cost, and reduce the amount of consumption. Effect
- Summary
- Abstract
- Description
- Claims
- Application Information
AI Technical Summary
Problems solved by technology
Method used
Image
Examples
Embodiment Construction
[0011] A method for recycling nickel and cobalt slag from zinc smelting, including purifying the nickel and cobalt slag and returning it to a stage of purification for reuse as zinc powder, recovering cadmium and canceling the pickling production of nickel and cobalt slag, and using an organic reagent to remove cobalt from the cobalt-containing solution after recovering copper and cadmium, etc. three parts.
[0012] The method is a new way of recycling nickel and cobalt slag, and can effectively reduce the consumption of purified zinc powder.
[0013] 1. In this method, the second-stage nickel-cobalt slag that is sent to cadmium recovery for pickling after protoplasmification is firstly sent to the first-stage purification to be used as zinc powder. The first-stage purification reduces the amount of zinc powder by more than 70%, and other control process conditions do not change. That is: the reaction temperature is 50-90°C, the reaction time is 1-3h, and the flow rate is 100-...
PUM
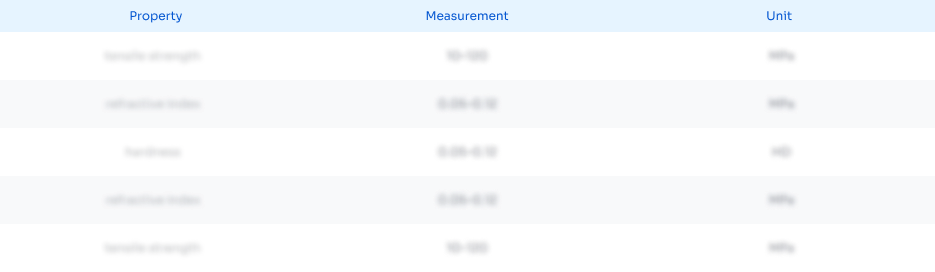
Abstract
Description
Claims
Application Information

- R&D
- Intellectual Property
- Life Sciences
- Materials
- Tech Scout
- Unparalleled Data Quality
- Higher Quality Content
- 60% Fewer Hallucinations
Browse by: Latest US Patents, China's latest patents, Technical Efficacy Thesaurus, Application Domain, Technology Topic, Popular Technical Reports.
© 2025 PatSnap. All rights reserved.Legal|Privacy policy|Modern Slavery Act Transparency Statement|Sitemap|About US| Contact US: help@patsnap.com