Modified polyurethane-acrylate water-based woodware emulsion and preparation method thereof
A technology of acrylate and wood emulsion, applied in polyurea/polyurethane coatings, coatings, etc., to achieve the effects of improving water resistance, improving comprehensive performance, and improving medium resistance
- Summary
- Abstract
- Description
- Claims
- Application Information
AI Technical Summary
Problems solved by technology
Method used
Image
Examples
Embodiment 1
[0025]
[0026]
[0027] 1) Preparation of polyurethane prepolymer
[0028] Isophorone diisocyanate and polycaprolactone diol were vacuum dehydrated and dried at 50°C for 0.5h for use, and the isophorone Phorone diisocyanate, polycaprolactone diol, methyl acrylate, and acrylic acid monomer, the speed is 200rpm, and 2g of catalyst dibutyltin dilaurate is added, and the temperature is raised to 70°C to react for 0.5h, and then the hydrophilic expansion agent is added. Chain agent dimethylolbutyric acid, internal crosslinking agent trimethylolpropane, and epoxy resin were polymerized at 70°C for 1.5h, then cooled to room temperature, and a silane coupling agent solution containing 5 parts of water was added dropwise, controlled at After 0.5h of dropwise addition, triethylamine was added to neutralize at room temperature for 20min; finally, the rotational speed was increased to 1500rpm, and 41.675 parts of deionized water was slowly added dropwise to disperse, and the titrat...
Embodiment 2
[0032]
[0033]
[0034] 1) Preparation of polyurethane prepolymer
[0035] Isophorone diisocyanate and polycaprolactone diol were dehydrated and dried under vacuum at 60°C for 0.8h for use, and the isophorone Phorone diisocyanate, polycaprolactone diol, methyl acrylate, and acrylic acid monomer, the rotation speed is 280rpm, and 1g of catalyst dibutyltin dilaurate is added, and the temperature is raised to 80°C to react for 0.6h, and then the hydrophilic expansion agent is added. Chain agent dimethylolbutyric acid, internal crosslinking agent trimethylolpropane, and epoxy resin were polymerized at 80°C for 1.6h, then cooled to room temperature, and a silane coupling agent solution containing 9.455 parts of water was added dropwise, controlled at After 0.8h of dropwise addition, triethylamine was added to neutralize at room temperature for 24min; finally, the rotating speed was increased to 1750rpm, and 39.385 parts of deionized water was slowly added dropwise to dispers...
Embodiment 3
[0039]
[0040]
[0041] 1) Preparation of polyurethane prepolymer
[0042]Isophorone diisocyanate and polycaprolactone diol were dehydrated and dried under vacuum at 70°C for 1 hour to be used, and the isophorone Alone diisocyanate, polycaprolactone diol, methyl acrylate, and acrylic acid monomer, the rotation speed is 350rpm, and 2g of catalyst dibutyltin dilaurate is added, and the temperature is raised to 90°C for 1 hour, and then the hydrophilic chain extender is added Dimethylolbutyric acid, internal crosslinking agent trimethylolpropane, and epoxy resin are polymerized at 90°C for 2 hours, then cooled to room temperature, and silane coupling agent solution containing 10 parts of water is added dropwise, controlled at 1 hour. After completion, add triethylamine to neutralize at room temperature for 30 minutes; finally increase the rotation speed to 2000rpm at a stirring rate, slowly add 43.84 parts of deionized water to disperse, and control the titration time to 1...
PUM
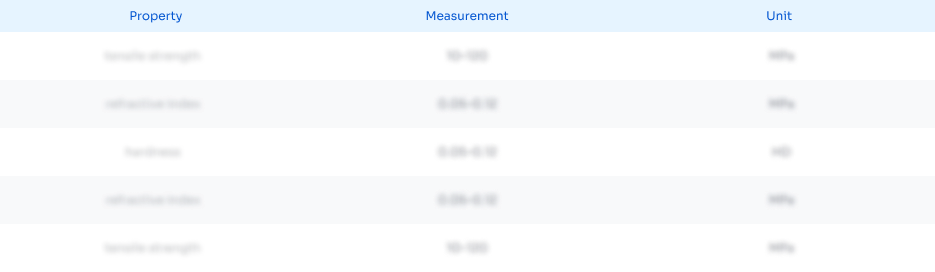
Abstract
Description
Claims
Application Information

- R&D Engineer
- R&D Manager
- IP Professional
- Industry Leading Data Capabilities
- Powerful AI technology
- Patent DNA Extraction
Browse by: Latest US Patents, China's latest patents, Technical Efficacy Thesaurus, Application Domain, Technology Topic, Popular Technical Reports.
© 2024 PatSnap. All rights reserved.Legal|Privacy policy|Modern Slavery Act Transparency Statement|Sitemap|About US| Contact US: help@patsnap.com