A kind of high-strength glass fiber yarn and its preparation method and application
A technology of glass fiber yarn and glass fiber, which is applied in the field of high-strength glass fiber yarn and its preparation, can solve the problems of high elongation at break, low elastic modulus, and low tensile strength, and achieve high tensile strength, High elastic modulus and low production cost
- Summary
- Abstract
- Description
- Claims
- Application Information
AI Technical Summary
Problems solved by technology
Method used
Examples
Embodiment 1
[0017] In the embodiment of the present invention, a high-strength glass fiber yarn is composed of the following raw materials in parts by weight: 35 parts of glass fiber, 8 parts of mercaptoethanol, 1 part of polyethylene glycol monomethyl ether, hydroxyethylidene diphosphonic acid 3 parts, 16 parts of polydimethyldiallylammonium chloride.
[0018] Mercaptoethanol and deionized water were prepared into a mercaptoethanol solution with a mass concentration of 5%, and polyethylene glycol monomethyl ether and absolute ethanol were prepared into a polyethylene glycol monomethyl ether solution with a mass concentration of 15%. Put the glass fiber into the mercaptoethanol solution, raise the temperature to 75°C under the protection of nitrogen, and heat and stir at this temperature for 40min, then slowly add polydimethyldiallylammonium chloride dropwise at a rate of 10 drops per minute After the speed dropwise addition, raise the temperature to 95°C, and heat and stir at this temper...
Embodiment 2
[0020] In the embodiment of the present invention, a high-strength glass fiber yarn is composed of the following raw materials in parts by weight: 43 parts of glass fiber, 16 parts of mercaptoethanol, 8 parts of polyethylene glycol monomethyl ether, hydroxyethylidene diphosphonic acid 10 parts, 24 parts of polydimethyldiallylammonium chloride.
[0021] Mercaptoethanol and deionized water were prepared into a mercaptoethanol solution with a mass concentration of 10%, and polyethylene glycol monomethyl ether and absolute ethanol were prepared into a polyethylene glycol monomethyl ether solution with a mass concentration of 25%. Put the glass fiber into the mercaptoethanol solution, raise the temperature to 85°C under the protection of nitrogen, and heat and stir at this temperature for 50min, then slowly add polydimethyldiallylammonium chloride dropwise at a rate of 15 drops per minute After the speed dropwise addition, raise the temperature to 100°C, and heat and stir at this t...
Embodiment 3
[0023] In the embodiment of the present invention, a high-strength glass fiber yarn is composed of the following raw materials in parts by weight: 37 parts of glass fiber, 10 parts of mercaptoethanol, 3 parts of polyethylene glycol monomethyl ether, hydroxyethylidene diphosphonic acid 5 parts, 18 parts of polydimethyldiallylammonium chloride.
[0024] Mercaptoethanol and deionized water were prepared into a mercaptoethanol solution with a mass concentration of 8%, and polyethylene glycol monomethyl ether and absolute ethanol were prepared into a polyethylene glycol monomethyl ether solution with a mass concentration of 20%. Put the glass fiber into the mercaptoethanol solution, raise the temperature to 80°C under the protection of nitrogen, and heat and stir at this temperature for 45min, then slowly add polydimethyldiallylammonium chloride dropwise at a rate of 12 drops per minute After the speed dropwise addition, raise the temperature to 98°C, and heat and stir at this temp...
PUM
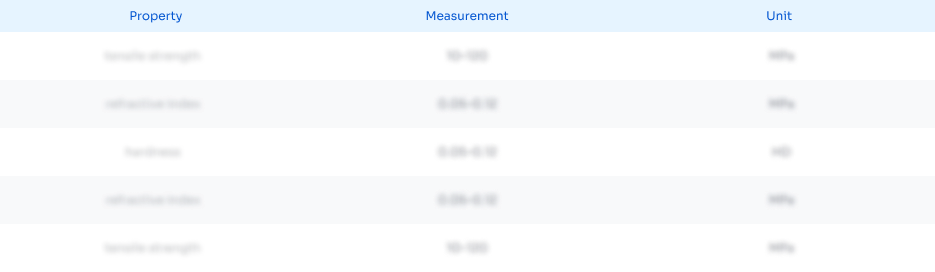
Abstract
Description
Claims
Application Information

- R&D
- Intellectual Property
- Life Sciences
- Materials
- Tech Scout
- Unparalleled Data Quality
- Higher Quality Content
- 60% Fewer Hallucinations
Browse by: Latest US Patents, China's latest patents, Technical Efficacy Thesaurus, Application Domain, Technology Topic, Popular Technical Reports.
© 2025 PatSnap. All rights reserved.Legal|Privacy policy|Modern Slavery Act Transparency Statement|Sitemap|About US| Contact US: help@patsnap.com