Method of low-temperature and low-pressure countercurrently leaching tellurium from copper anode mud
A copper anode slime and countercurrent leaching technology, applied in the direction of element selenium/tellurium, process efficiency improvement, etc., can solve the problems of limited promotion and application, low tellurium recovery rate, high corrosion resistance requirements, etc., to increase economic benefits , Solve the effect of low tellurium removal rate and reducing cycle accumulation
- Summary
- Abstract
- Description
- Claims
- Application Information
AI Technical Summary
Problems solved by technology
Method used
Image
Examples
Embodiment 1
[0025] The copper anode slime treated in this example contains Cu20.26% and Te2.01%. The treatment process and treatment effect are as follows:
[0026] (1) Wash the copper anode slime in a washing tank, the liquid-solid ratio is 4:1 by volume to mass ratio L / Kg, the temperature is 30°C, and the time is 0.8h; the washing slag contains 14.5% copper and 2.25% tellurium.
[0027] (2) Put the water-washed slag in the reaction kettle for one oxygen pressure acid leaching to remove copper, control the liquid-solid ratio by volume to mass ratio L / Kg to 5:1, the acidity of sulfuric acid is 200g / L, the temperature is 100°C, and the oxygen partial pressure is 1.2 MPa, time 0.5h; primary leaching slag contains 5.22% copper and 1.85% tellurium.
[0028] (3) Put the primary leaching residue in an autoclave for secondary leaching, control the liquid-solid ratio by volume to mass ratio L / Kg to 10:1, sulfuric acid acidity 200g / L, temperature 180°C, oxygen partial pressure 0.8MPa, time 1.5 h;...
Embodiment 2
[0031] The copper anode slime treated in this example contains Cu20.26% and Te2.01%. The treatment process and treatment effect are as follows:
[0032] (1) Wash the copper anode slime in a washing tank with a liquid-solid ratio of 5:1 by volume to mass ratio L / Kg at a temperature of 40°C for 0.5 hours; the washing slag contains 12.91% copper and 2.41% tellurium.
[0033] (2) Put the water-washed slag in the reaction kettle for oxygen pressure acid leaching to remove copper, control the liquid-solid ratio according to the volume and mass ratio L / Kg to 7:1, the acidity of sulfuric acid is 150g / L, the temperature is 120°C, and the oxygen partial pressure is 1MPa , time 1h; the first leaching slag contains 4.18% copper and 1.97% tellurium.
[0034] (3) Put the primary leaching residue in an autoclave for secondary leaching, control the liquid-solid ratio by volume to mass ratio L / Kg to 15:1, sulfuric acid acidity 250g / L, temperature 160°C, oxygen partial pressure 1.2MPa, time 1h ...
Embodiment 3
[0037] The copper anode slime treated in this example contains Cu20.26% and Te2.01%. The treatment process and treatment effect are as follows:
[0038] (1) Put the copper anode slime in the washing tank for washing, the liquid-solid ratio is 3:1 according to the volume-to-mass ratio L / Kg, the temperature is 50°C, and the time is 1h; the washing slag contains 15.27% copper and 2.17% tellurium.
[0039] (2) Put the water-washed slag in the reaction kettle for one oxygen pressure acid leaching to remove copper, control the liquid-solid ratio by volume to mass ratio L / Kg to 10:1, the acidity of sulfuric acid is 100g / L, the temperature is 130°C, and the oxygen partial pressure is 0.5 MPa, time 1.5h; primary leaching slag contains 4.76% copper and 1.59% tellurium.
[0040] (3) Put the primary leaching residue in an autoclave for secondary leaching, control the liquid-solid ratio by volume to mass ratio L / Kg to 8:1, sulfuric acid acidity 150g / L, temperature 120°C, oxygen partial pre...
PUM
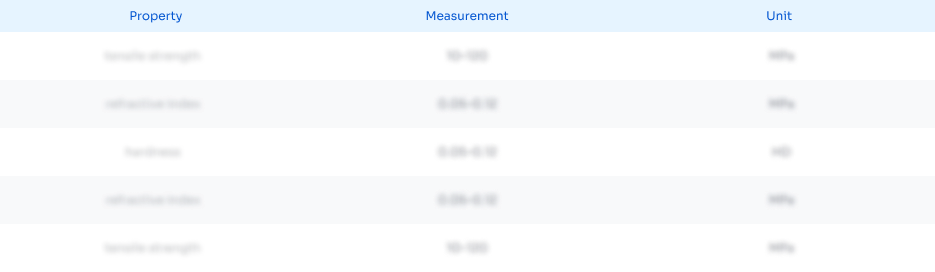
Abstract
Description
Claims
Application Information

- R&D
- Intellectual Property
- Life Sciences
- Materials
- Tech Scout
- Unparalleled Data Quality
- Higher Quality Content
- 60% Fewer Hallucinations
Browse by: Latest US Patents, China's latest patents, Technical Efficacy Thesaurus, Application Domain, Technology Topic, Popular Technical Reports.
© 2025 PatSnap. All rights reserved.Legal|Privacy policy|Modern Slavery Act Transparency Statement|Sitemap|About US| Contact US: help@patsnap.com