Iron-rich high-entropy alloy powder material for 3D printing and preparation method thereof
A high-entropy alloy and 3D printing technology, which is applied in metal processing equipment, additive processing, transportation and packaging, etc., can solve the problems of multiple processes and high energy consumption in the two-step atomization method, and achieve high sphericity and oxygen content Low, consistent quality results
- Summary
- Abstract
- Description
- Claims
- Application Information
AI Technical Summary
Problems solved by technology
Method used
Image
Examples
Embodiment 1
[0029] Firstly, 35.85 kg of Fe ingot, 8.66 kg of Al ingot, 16.69 kg of Cr ingot, 18.92 kg of Co ingot, 13.19 kg of Ni ingot and 6.69 kg of Ni-B alloy were weighed. Then place them in the device schematic in order of melting point from low to high. figure 1 In the intermediate frequency induction furnace 1, the vacuum degree is 1×10 -3Mpa, filled with 1.02 atmospheres of argon, the melting power is 180KW, smelting for 60 minutes, vacuum refining for 10 minutes, then preheating the tundish 4 and draft tube 3 between the medium frequency induction furnace 2 and the atomizer 5 to 700°C , pour the refined liquid into the tundish, turn on the high-pressure argon gas to start atomization, at this time, the argon gas pressure is 3.5MPa, the air velocity is 300m / s, and the metal liquid passes through the tundish at a flow rate of 10Kg / min from a hole diameter of 5.0mm The leaking hole flows out and meets the intersection of supersonic argon gas through the annular gap atomizer to beco...
Embodiment 2
[0032] Firstly, 41.13 kg of Fe ingot, 7.95 kg of Al ingot, 15.32 kg of Cr ingot, 17.36 kg of Co ingot, 12.08 kg of Ni ingot and 6.17 kg of Ni-B alloy were weighed. Then place them in the device schematic in order of melting point from low to high. figure 1 In the intermediate frequency induction furnace 1, the vacuum degree is 1.5×10 -3 Mpa, filled with 1.02 atmospheres of argon, the melting power is 190KW, smelting for 55 minutes and then vacuuming and refining for 12 minutes; then preheat the tundish and draft tube between the medium frequency induction furnace and the atomizer to 700 ° C, and the refined The liquid is poured into the tundish, and the high-pressure argon gas is turned on to start atomization. At this time, the pressure of the argon gas is 3.5MPa, the air velocity is 310m / s, and the metal liquid flows out through the tundish at a flow rate of 11Kg / min from the hole with a diameter of 5.0mm. , passing through the annular gap atomizer and meeting the intersect...
Embodiment 3
[0034] Weigh 45.6 kg of Fe ingot, 7.34 kg of Al ingot, 14.15 kg of Cr ingot, 16.04 kg of Co ingot, 11.41 kg of Ni ingot and 5.40 kg of Ni-B alloy. Then place them in the device schematic in order of melting point from low to high. figure 1 In the intermediate frequency induction furnace 1, the vacuum degree is 1.2×10 -3 Mpa, filled with 1.02 atmospheres of argon, the melting power is 200KW, smelting for 50 minutes and then vacuuming and refining for 15 minutes; then preheat the tundish and draft tube between the medium frequency induction furnace and the atomizer to 700 ° C, and the refined The liquid is poured into the tundish, and the high-pressure argon gas is turned on to start atomization. At this time, the argon gas pressure is 3.5MPa, the air velocity is 320m / s, and the metal liquid flows out through the tundish at a flow rate of 12Kg / min from the hole with a diameter of 5.0mm. , passing through the annular gap atomizer and meeting the intersection point of supersonic ...
PUM
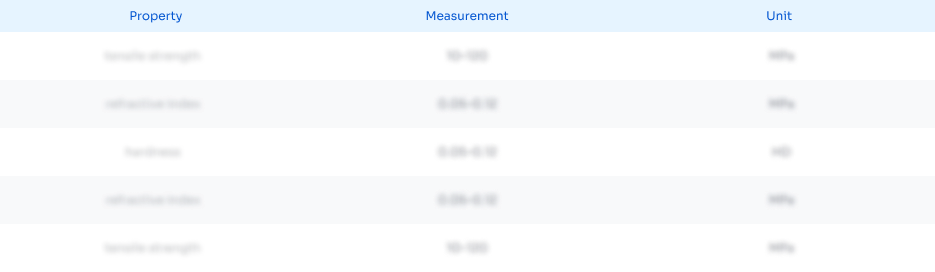
Abstract
Description
Claims
Application Information

- Generate Ideas
- Intellectual Property
- Life Sciences
- Materials
- Tech Scout
- Unparalleled Data Quality
- Higher Quality Content
- 60% Fewer Hallucinations
Browse by: Latest US Patents, China's latest patents, Technical Efficacy Thesaurus, Application Domain, Technology Topic, Popular Technical Reports.
© 2025 PatSnap. All rights reserved.Legal|Privacy policy|Modern Slavery Act Transparency Statement|Sitemap|About US| Contact US: help@patsnap.com