Smelting method based on nickel-based heat-resistance alloy
A smelting method and a nickel-based heat-resistant technology, applied in the field of alloy smelting methods, can solve the problems of high manufacturing cost, complex manufacturing, and poor heat resistance of alloys, and achieve the goals of reducing heat treatment deformation, increasing life, and improving lateral performance Effect
- Summary
- Abstract
- Description
- Claims
- Application Information
AI Technical Summary
Problems solved by technology
Method used
Examples
Embodiment 1
[0018] A smelting method based on a nickel-based heat-resistant alloy, the specific steps are as follows:
[0019] Step A, the preparation of molten steel, put quantitative metal nickel, metal chromium, metal cobalt, niobium iron, vanadium iron, titanium iron in the EAF electric arc furnace, heat to high temperature until each metal melts;
[0020] Step B, the removal of molten steel impurities, first adjust the temperature and refine the molten steel produced in step A for a period of time, then add electrolytic aluminum and ferroboron for sufficient stirring to carry out deoxidation treatment;
[0021] Step C, pouring of molten steel, put the molten alloy steel produced in step B into the LF ladle furnace to cool for a period of time, and then pour it into the shaping mold with exothermic agent added at the riser;
[0022] Step D, alloy phase transformation treatment, place the casted alloy in step C at a temperature of 1280°C-1300°C for 24-30h, and after the alloy is anneal...
Embodiment 2
[0026] In the preparation of molten steel in step A, the weight percentages are: 0.01-0.03% nickel, 19.5-21% chromium, 0.02-0.03% cobalt, 0.01-1.5% niobium, 0.2-0.6% vanadium, 1.5-3.0% titanium %, S≤0.02, P≤0.02, and the balance is unavoidable impurities. The high temperature in step A is 2800°C-3000°C. In the process of removing impurities in the molten steel in step B, 2% by weight electrolytic aluminum and 0.005% by weight ferroboron are added for sufficient stirring. In step B, the deoxidation process in the removal of molten steel impurities is as follows: add 0.5-0.8% Mn and 1-2% Si by weight in molten steel to carry out pre-deoxidation, thin slag on the surface of molten steel After formation, charcoal powder is added for final deoxidation. The reprocessing process of the alloy in step E is as follows: first, blank the alloy forged in step D, and then perform quenching treatment after blanking. The temperature during quenching is 850-900 ° C. Put the alloy at 500°C-5...
Embodiment 3
[0028] In the preparation of molten steel in step A, the weight percentages are: 0.01-0.03% nickel, 19.5-21% chromium, 0.02-0.03% cobalt, 0.01-1.5% niobium, 0.2-0.6% vanadium, 1.5-3.0% titanium %, S≤0.02, P≤0.02, and the balance is unavoidable impurities. The high temperature in step A is 2800°C-3000°C. In the process of removing impurities in the molten steel in step B, 2% by weight electrolytic aluminum and 0.005% by weight ferroboron are added for sufficient stirring. In step B, the deoxidation process in the removal of molten steel impurities is as follows: add 0.5-0.8% Mn and 1-2% Si by weight in molten steel to carry out pre-deoxidation, thin slag on the surface of molten steel After formation, charcoal powder is added for final deoxidation. The reprocessing process of the alloy in step E is as follows: firstly, the alloy forged in step D is blanked, and then quenched, the temperature during quenching is 850-900°C, and air-cooled for 3.5 hours after quenching, and Put...
PUM
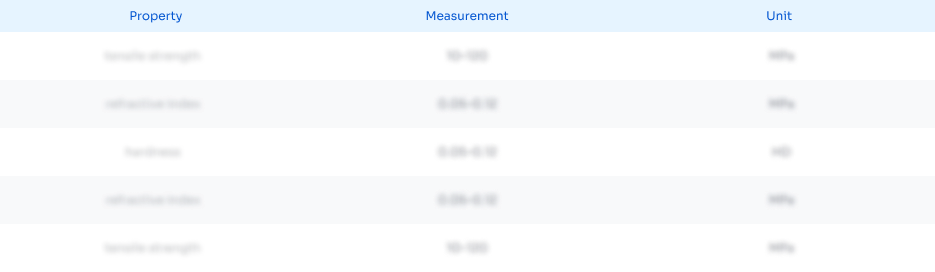
Abstract
Description
Claims
Application Information

- R&D
- Intellectual Property
- Life Sciences
- Materials
- Tech Scout
- Unparalleled Data Quality
- Higher Quality Content
- 60% Fewer Hallucinations
Browse by: Latest US Patents, China's latest patents, Technical Efficacy Thesaurus, Application Domain, Technology Topic, Popular Technical Reports.
© 2025 PatSnap. All rights reserved.Legal|Privacy policy|Modern Slavery Act Transparency Statement|Sitemap|About US| Contact US: help@patsnap.com