SMD diode preparation technology
A preparation process and technology for diodes, which are used in semiconductor/solid-state device manufacturing, electrical components, circuits, etc., can solve the problems of low curing temperature, affect diode performance, damage, etc., and achieve the effects of enhancing compactness, saving resources, and simplifying the process.
- Summary
- Abstract
- Description
- Claims
- Application Information
AI Technical Summary
Problems solved by technology
Method used
Image
Examples
Embodiment 1
[0049] The chip diode of this embodiment, such as Image 6 As shown, it includes a chip 15, the two ends of the chip are respectively welded with the upper lead 13 and the lower lead 14 by solder 16, and the chip connection end of the lower lead is provided with a pit 19 that can accommodate the chip, so that the inner sidewall of the pit 19 and the An annular gap surrounding the periphery of the chip 15 is formed between the side walls of the chip 15, and the chip sheath sealing glue 17 is filled in the annular gap; a plastic package 18 wrapping the chip 15 and the leads is formed outside the leads by plastic sealing.
[0050] In this embodiment, the process steps of preparing the chip diode with the above structure are as follows:
[0051] (1) Alloy: take the soldering sheet and diffusion sheet, stack them in the order of soldering sheet → diffusion sheet → soldering sheet, and then place the stacked soldering sheet and diffusion sheet in a high-frequency alloy furnace for a...
Embodiment 2
[0062] Compared with Embodiment 1, this embodiment, in order to form an annular gap around the periphery of the chip outside the chip before the glue filling process in step (6), by changing the structure of Embodiment 1, the soldered leads and the chip Placed in a plastic casing with an open upper end, the specific structure, such as Figure 7 As shown, it includes a chip 15, and the two ends of the chip are respectively welded with an upper lead 13 and a lower lead 14 by solder 16, and the welded chip 15 and the lead are placed in a plastic casing 20 with an upper end opening, so that the plastic casing 20 An annular gap is formed on the periphery of the chip 15 between the inner side wall of the chip 15 and the chip 15, and the chip sheathing glue 17 is filled in the annular gap; The plastic encapsulation structure 18 of the body 20.
[0063] In this embodiment, the process steps of preparing the chip diode with the above structure are as follows:
[0064] (1) Alloy: take...
Embodiment 3
[0074] Compared with Example 1, in order to form an annular gap around the periphery of the chip outside the chip before the glue filling process in step (6), by changing the structure of Example 1, a chip inner shell is prefabricated. The plastic-encapsulated shell of the chip, the soldered leads and the chip are placed in the chip inner shell, the specific structure, such as Figure 8As shown, it comprises a chip 15, and the two ends of the chip are welded with the upper lead 13 and the lower lead 14 respectively by solder 16, and the chip 15 and the lead after welding are placed in the chip inner shell 22, so that the inner side wall of the chip inner shell 22 and the An annular gap on the periphery of the chip 15 is formed between the side walls of the chip 15, and the chip inner shell 22 is arranged at the center of the bottom of a plastic casing 21 whose height is higher than the chip inner shell; and the chip sheath seal glue 17 is filled in the annular gap; And the epo...
PUM
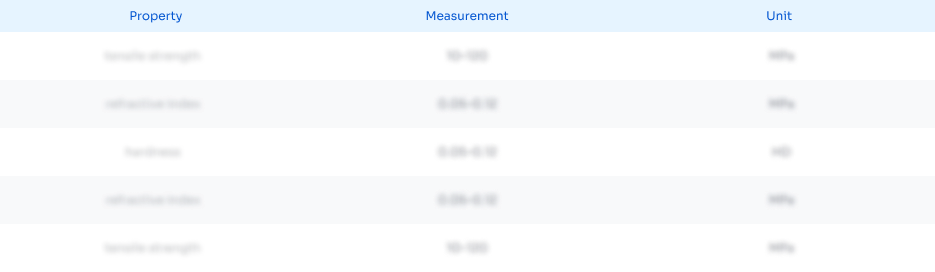
Abstract
Description
Claims
Application Information

- R&D Engineer
- R&D Manager
- IP Professional
- Industry Leading Data Capabilities
- Powerful AI technology
- Patent DNA Extraction
Browse by: Latest US Patents, China's latest patents, Technical Efficacy Thesaurus, Application Domain, Technology Topic, Popular Technical Reports.
© 2024 PatSnap. All rights reserved.Legal|Privacy policy|Modern Slavery Act Transparency Statement|Sitemap|About US| Contact US: help@patsnap.com