Heat-resistant wear-resistant tear-resistant modified polyurethane rubber cable material
A polyurethane rubber, tear-resistant technology, applied in circuits, electrical components, plastic/resin/wax insulators, etc., can solve the problems of unsatisfactory heat-resistant, wear-resistant and tear-resistant performance, poor heat-resistant aging performance, etc.
- Summary
- Abstract
- Description
- Claims
- Application Information
AI Technical Summary
Problems solved by technology
Method used
Examples
Embodiment 1
[0016] A heat-resistant, wear-resistant and tear-resistant modified polyurethane rubber cable material proposed by the present invention, its raw materials include: 100 parts of modified polyurethane elastomer, 40 parts of chloroprene rubber, 10 parts of butyl rubber, EPDM 4 parts of propylene rubber, 6 parts of epoxy resin, 3 parts of ethyl acetate, 4 parts of polytetrahydrofuran diol, 6 parts of trimethylolpropane, 6 parts of polytetrahydrofuran ether diol, 3 parts of hydroxyl-terminated polybutadiene, 4 parts of polycaprolactone diol, 3 parts of di-o-chlorodianiline methane, 4 parts of hydroxy-terminated nitrile rubber, 6 parts of dibutyltin dilaurate, 3 parts of ethyl triethoxysilane, 5 parts of fumed white carbon black 4.5 parts of aluminum silicate, 6 parts of stearic acid, 4 parts of molybdenum disulfide, 3 parts of quartz powder, 3.5 parts of bentonite, 6 parts of zinc oxide, 6 parts of sulfur, 4 parts of accelerator M, 2.5 parts of antioxidant D, 4.5 parts of magnesiu...
Embodiment 2
[0019] A heat-resistant, wear-resistant and tear-resistant modified polyurethane rubber cable material proposed by the present invention, its raw materials include by weight: 80 parts of modified polyurethane elastomer, 60 parts of neoprene rubber, 5 parts of butyl rubber, EPEM 6 parts of propylene rubber, 3 parts of epoxy resin, 5 parts of ethyl acetate, 2 parts of polytetrahydrofuran diol, 9 parts of trimethylolpropane, 4 parts of polytetrahydrofuran ether diol, 4 parts of hydroxyl-terminated polybutadiene, 3 parts of polycaprolactone diol, 5 parts of di-o-chlorodianiline methane, 2 parts of hydroxy-terminated nitrile rubber, 9 parts of dibutyltin dilaurate, 1 part of ethyltriethoxysilane, and 8 parts of fumed white carbon black 3 parts of aluminum silicate, 8 parts of stearic acid, 2 parts of molybdenum disulfide, 5 parts of quartz powder, 1 part of bentonite, 8 parts of zinc oxide, 3 parts of sulfur, 6 parts of accelerator M, 1 part of anti-aging agent D, magnesium oxide 6...
Embodiment 3
[0022]A heat-resistant, wear-resistant and tear-resistant modified polyurethane rubber cable material proposed by the present invention, its raw materials include: 120 parts of modified polyurethane elastomer, 20 parts of chloroprene rubber, 15 parts of butyl rubber, EPDM 2 parts of propylene rubber, 9 parts of epoxy resin, 1 part of ethyl acetate, 6 parts of polytetrahydrofuran diol, 3 parts of trimethylolpropane, 8 parts of polytetrahydrofuran ether diol, 2 parts of hydroxyl-terminated polybutadiene, 5 parts of polycaprolactone diol, 1 part of di-o-chlorodianiline methane, 6 parts of hydroxy-terminated nitrile rubber, 3 parts of dibutyltin dilaurate, 5 parts of ethyl triethoxysilane, 2 parts of fumed white carbon black 6 parts of aluminum silicate, 4 parts of stearic acid, 6 parts of molybdenum disulfide, 1 part of quartz powder, 6 parts of bentonite, 4 parts of zinc oxide, 9 parts of sulfur, 2 parts of accelerator M2, 4 parts of anti-aging agent D, magnesium oxide 3 parts, ...
PUM
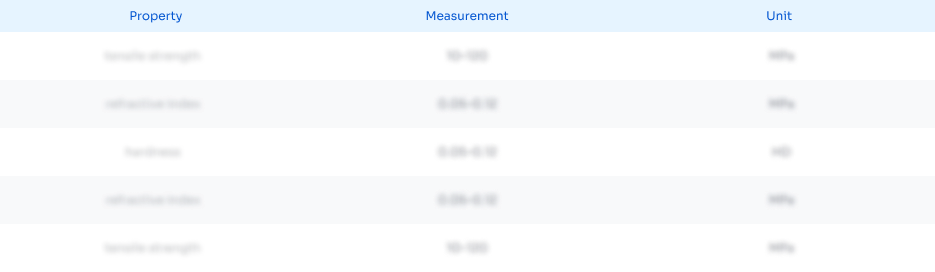
Abstract
Description
Claims
Application Information

- Generate Ideas
- Intellectual Property
- Life Sciences
- Materials
- Tech Scout
- Unparalleled Data Quality
- Higher Quality Content
- 60% Fewer Hallucinations
Browse by: Latest US Patents, China's latest patents, Technical Efficacy Thesaurus, Application Domain, Technology Topic, Popular Technical Reports.
© 2025 PatSnap. All rights reserved.Legal|Privacy policy|Modern Slavery Act Transparency Statement|Sitemap|About US| Contact US: help@patsnap.com