Method used for preparing higher aliphatic phthalates via ester exchange
A technology of phthalic acid and higher alcohol esters, which is applied in the preparation of carboxylic acid esters, chemical instruments and methods, and the preparation of organic compounds, can solve the problems of many side reactions, low raw material consumption, and few side reactions, and achieve The catalyst is less corrosive, the process is clean and energy-saving, and the effect of mild reaction conditions
- Summary
- Abstract
- Description
- Claims
- Application Information
AI Technical Summary
Problems solved by technology
Method used
Image
Examples
Embodiment 1
[0022] Add 19.4 grams of dimethyl phthalate (abbreviated as DMP, 0.1mol), 47.5 grams of 2-propylheptanol (0.3mol), and 0.2 grams of potassium titanium oxalate (1.0% of the mass of DMP) into 100ml of water separator In the two-necked round-bottomed flask of the device, the condenser was connected to the water separator, stirred evenly, and the temperature was raised to 200 ° C for 5 hours. After the reaction, the mixture was qualitatively analyzed by gas chromatography-mass spectrometry, and quantitatively analyzed by gas chromatography. DMP Both conversion rate and DPHP selectivity are above 99%.
Embodiment 2
[0024] Catalyst blank experiment: no catalyst was added, other conditions were the same as in Example 1, the conversion rate of DMP only reached 50%, and the selectivity of DPHP was only 5%.
Embodiment 3~21
[0026] The specific method of Examples 3-21 is similar to that of Example 1, and the specific reaction conditions and results are shown in Table 1.
[0027] It can be seen from the catalyst blank experiment that DMP and 2-propylheptanol were heated and reacted at 200° C. for 5 hours, and the conversion rate of DMP and the selectivity of DPHP were all very low (embodiment 2). Concentrated sulfuric acid has a good catalytic effect on the preparation of DPHP by the esterification reaction of 2-propylheptanol and phthalic anhydride, and the conversion rate of phthalic anhydride and the selectivity of DPHP can reach more than 99%. Yet, the vitriol oil is used to catalyze the transesterification reaction of DMP and 2-propylheptanol, although the DMP conversion rate can reach more than 99%, but the DPHP selectivity only has 80% (embodiment 3). Trying to use tin titanate as a catalyst, the reaction result under the same conditions is the same as that of the catalyst blank experiment (...
PUM
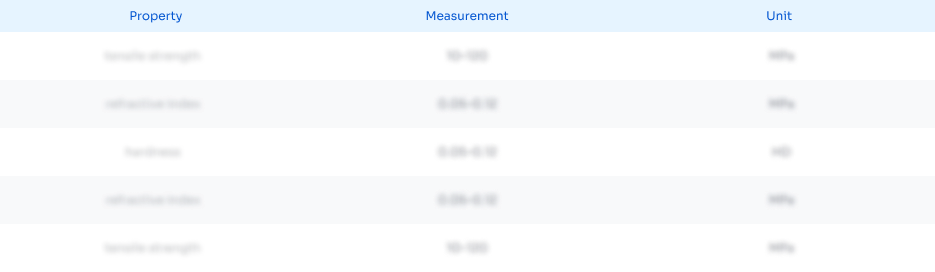
Abstract
Description
Claims
Application Information

- Generate Ideas
- Intellectual Property
- Life Sciences
- Materials
- Tech Scout
- Unparalleled Data Quality
- Higher Quality Content
- 60% Fewer Hallucinations
Browse by: Latest US Patents, China's latest patents, Technical Efficacy Thesaurus, Application Domain, Technology Topic, Popular Technical Reports.
© 2025 PatSnap. All rights reserved.Legal|Privacy policy|Modern Slavery Act Transparency Statement|Sitemap|About US| Contact US: help@patsnap.com