High-strength composite submersed nozzle combined with silicon carbide crystal whiskers and manufacturing method
A silicon carbide whisker, immersion technology, used in manufacturing tools, casting equipment, casting melt containers, etc., can solve the problems of low reactivity and separation, and achieve less impurities and defects on the whisker surface, uniform crystal composition, The effect of good high temperature strength
- Summary
- Abstract
- Description
- Claims
- Application Information
AI Technical Summary
Problems solved by technology
Method used
Image
Examples
Embodiment 1
[0024] Silicon carbide whiskers combined with high-strength composite submerged nozzles. Including the outer body, the outer slag line section, the inner layer, and the interface layer.
[0025] Outer body raw materials and their mass percentages: white corundum 20%, tabular corundum 40%, calcined alumina 10%, flake graphite 20%, silicon carbide 5%, metal silicon 3%, boron carbide 2%, additional raw materials Total 10% thermosetting phenolic resin.
[0026] The raw materials of the outer slag line section and their mass percentages: 80% fused stabilized zirconia, 12% flake graphite, 6% zircon mullite, 2% boron carbide, plus 8% thermosetting phenolic resin binder in the total amount of raw materials.
[0027] Inner layer raw materials and their mass percentages: 45% tabular corundum, 15% white corundum, 10% calcined alumina, 15% sialon, 15% silicon nitride, plus 8% aluminum sol binder.
[0028]Interface layer raw materials and their mass percentages: 60% tabular corundum, 10%...
Embodiment 2
[0036] Silicon carbide whiskers combined with high-strength composite submerged nozzles. Including the outer body, the outer slag line section, the inner layer, and the interface layer.
[0037] Outer body raw materials and their mass percentages: 60% tabular corundum, 8% calcined alumina, 20% flake graphite, 5% zircon mullite, 3% metal silicon, 2% boron carbide, 2% silicon carbide, The total amount of raw materials added is 9% thermosetting phenolic resin.
[0038] Raw materials of the outer slag line section and their mass percentages: 75% fused stabilized zirconia, 12% flake graphite, 8% zircon mullite, 3% silicon carbide, 2% metal silicon powder, and 9% of the total amount of additional raw materials. Thermosetting Phenolic resin binder.
[0039] Inner layer raw materials and their mass percentages: 15% tabular corundum, 45% white corundum, 10% calcined alumina, 15% sialon, 15% silicon nitride, plus 8% aluminum sol binder.
[0040] Interface layer raw materials and thei...
Embodiment 3
[0048] Silicon carbide whiskers combined with high-strength composite submerged nozzles. Including the outer body, the outer slag line section, the inner layer, and the interface layer.
[0049] Outer body raw materials and their mass percentages: 50% tabular corundum, 10% white corundum, 10% calcined alumina, 15% flake graphite, 5% silicon carbide, 3% metallic silicon, 2% boron carbide, additional raw materials Total 8% thermosetting phenolic resin.
[0050] The raw materials of the outer layer slag line section and their mass percentages: 80% fused stabilized zirconia, 10% graphite flakes, 8% zirconium mullite, 2% boron carbide, plus 8% thermosetting phenolic resin binder in the total amount of raw materials.
[0051] Inner layer raw materials and their mass percentages: 60% of white corundum, 8% of calcined alumina, 15% of sialon, 12% of aron, 5% of silicon nitride, and 7% of the total amount of raw materials plus aluminum sol binder.
[0052] Interface layer raw material...
PUM
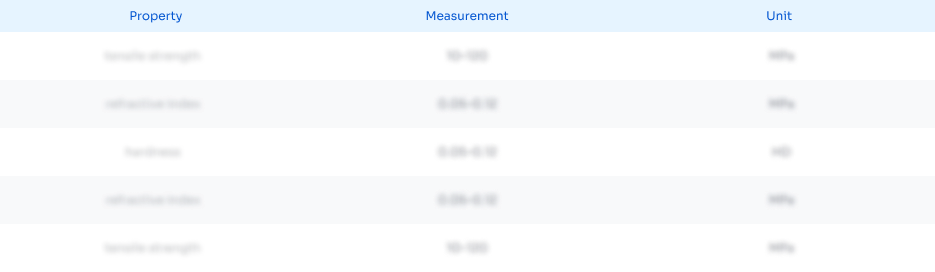
Abstract
Description
Claims
Application Information

- R&D
- Intellectual Property
- Life Sciences
- Materials
- Tech Scout
- Unparalleled Data Quality
- Higher Quality Content
- 60% Fewer Hallucinations
Browse by: Latest US Patents, China's latest patents, Technical Efficacy Thesaurus, Application Domain, Technology Topic, Popular Technical Reports.
© 2025 PatSnap. All rights reserved.Legal|Privacy policy|Modern Slavery Act Transparency Statement|Sitemap|About US| Contact US: help@patsnap.com