Heat-resisting high-toughness polystyrene resin foaming plastic
A polystyrene resin and foamed plastic technology, which is applied in the field of heat-resistant and high-toughness polystyrene resin foamed plastics, can solve the problem of insufficient toughness of foamed plastics, poor temperature resistance effect, and inability to support articles well, etc. problems, to achieve the effect of improving tensile properties and impact resistance, improving oxidation resistance and corrosion resistance, improving strength and surface smoothness
- Summary
- Abstract
- Description
- Claims
- Application Information
AI Technical Summary
Problems solved by technology
Method used
Examples
Embodiment 1
[0032] A heat-resistant and high-toughness polystyrene resin foamed plastic proposed by the present invention is composed of the following raw materials in parts by weight: 40 parts of polystyrene resin, potassium titanate fiber 2 parts, 11 parts of coconut fiber, 2 parts of polytetrafluoroethylene, 1 part of 3,5-tertiary butyl-4-hydroxyphenyl, 15 parts of talc powder, 6 parts of silicon carbide powder, 4 parts of kaolin, phthalate 1.2 parts of bis(2-ethylhexyl) formate, 1.1 parts of zinc stearate, 1 part of butyl p-hydroxybenzoate, 2 parts of foaming agent.
[0033] Its preparation method comprises the following steps:
[0034] S1, mix polystyrene resin and kaolin in proportion and put them into a mixer, the stirring rate is 15rpm, the stirring time is 5min, and the temperature in the mixer is raised to 100°C;
[0035] S2, mix talc powder, silicon carbide powder, bis(2-ethylhexyl) phthalate, and zinc stearate according to the ratio and then add them to the blender. The stirr...
Embodiment 2
[0040] A heat-resistant and high-toughness polystyrene resin foamed plastic proposed by the present invention, the heat-resistant high-toughness polystyrene resin foamed plastic is composed of the following raw materials in parts by weight: 43 parts of polystyrene resin, potassium titanate fiber 2.3 parts, 12 parts of coconut fiber, 2.5 parts of polytetrafluoroethylene, 1.1 parts of 3,5-tertiary butyl-4-hydroxyphenyl, 16 parts of talc powder, 7 parts of silicon carbide powder, 6 parts of kaolin, phthalate 1.3 parts of bis(2-ethylhexyl) formate, 1.2 parts of zinc stearate, 1.1 parts of butyl p-hydroxybenzoate, 2.5 parts of foaming agent.
[0041] Its preparation method comprises the following steps:
[0042] S1, mix the polystyrene resin and kaolin in proportion and put them into the mixer, the stirring rate is 20rpm, the stirring time is 7min, and the temperature in the mixer is raised to 105°C;
[0043] S2, mix talcum powder, silicon carbide powder, bis(2-ethylhexyl) phthala...
Embodiment 3
[0048] A heat-resistant and high-toughness polystyrene resin foamed plastic proposed by the present invention, the heat-resistant high-toughness polystyrene resin foamed plastic is composed of the following raw materials in parts by weight: 45 parts of polystyrene resin, potassium titanate fiber 2.5 parts, 13 parts of coconut fiber, 3 parts of polytetrafluoroethylene, 1.2 parts of 3,5-tertiary butyl-4-hydroxyphenyl, 18 parts of talc powder, 9 parts of silicon carbide powder, 8 parts of kaolin, phthalate 1.4 parts of bis(2-ethylhexyl) formate, 1.3 parts of zinc stearate, 1.2 parts of butyl p-hydroxybenzoate, 3 parts of foaming agent.
[0049] Its preparation method comprises the following steps:
[0050]S1, mix the polystyrene resin and kaolin in proportion and put them into the mixer, the stirring rate is 25rpm, the stirring time is 8min, and the temperature in the mixer is raised to 110°C;
[0051] S2, mix talcum powder, silicon carbide powder, bis(2-ethylhexyl) phthalate, a...
PUM
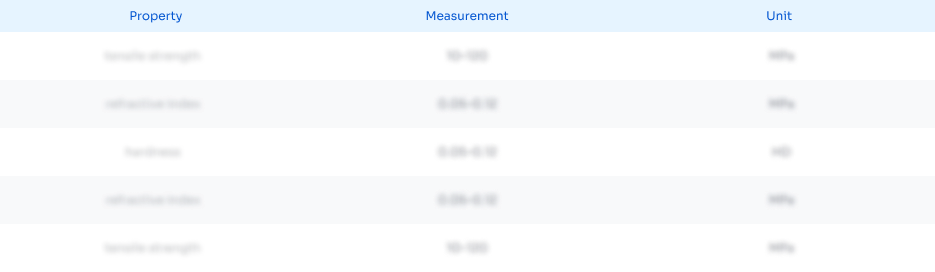
Abstract
Description
Claims
Application Information

- Generate Ideas
- Intellectual Property
- Life Sciences
- Materials
- Tech Scout
- Unparalleled Data Quality
- Higher Quality Content
- 60% Fewer Hallucinations
Browse by: Latest US Patents, China's latest patents, Technical Efficacy Thesaurus, Application Domain, Technology Topic, Popular Technical Reports.
© 2025 PatSnap. All rights reserved.Legal|Privacy policy|Modern Slavery Act Transparency Statement|Sitemap|About US| Contact US: help@patsnap.com