A kind of preparation method of composite titanium dioxide nanoparticles
A nanoparticle, titanium dioxide technology, applied in the direction of titanium dioxide, chemical instruments and methods, titanium oxide/hydroxide, etc., can solve the problems of limited photocatalytic activity and block irradiation, and achieve the effects of uniform size, easy operation and simple process
- Summary
- Abstract
- Description
- Claims
- Application Information
AI Technical Summary
Problems solved by technology
Method used
Examples
Embodiment 1
[0026] S1. Disperse 35 parts of ethyl titanate in 96 parts of organic solvent through ultrasonic oscillation equipment, add 3.6 parts of amine salt, stir evenly at room temperature, put the reaction solution in the reaction kettle, and react for 2 hours under the condition of 160°C , naturally cooled to room temperature, separated the solid phase, and obtained powder;
[0027] S2. Put the product obtained in step S1 into a mixing mixer, add 2 parts of flame retardant synergist, 5 parts of brominated flame retardant, and 0.1 part of heat stabilizer in sequence to obtain a mixed material;
[0028] S3. Put the mixed material obtained in step S2 into a twin-screw extruder, control the screw speed to 180rpm, fill the delivery pump with liquid carbon dioxide, control the delivery pressure to 7.4MPa, and heat the carbon dioxide to the critical temperature (31°C), After converting it into supercritical carbon dioxide, inject it into the third-fourth zone and fifth-eighth zone of the e...
Embodiment 2
[0034] S1. Disperse 38 parts of ethyl titanate in 110 parts of organic solvent through ultrasonic oscillation equipment, add 4.1 parts of amine salt, stir evenly at room temperature, put the reaction solution in a reaction kettle, and react for 3.5 hours at 280°C Afterwards, naturally cool to room temperature, separate the solid phase, and obtain powder;
[0035] S2. Put the product obtained in step S1 into a mixing mixer, add 6 parts of flame retardant synergist, 7 parts of brominated flame retardant, and 1 part of heat stabilizer in sequence to obtain a mixed material;
[0036] S3. Put the mixed material obtained in step S2 into a twin-screw extruder, control the screw speed to 600rpm, fill the delivery pump with liquid carbon dioxide, control the delivery pressure to 50MPa, and heat the carbon dioxide to the critical temperature (31°C), so that After it is converted into supercritical carbon dioxide, it is injected into the third-fourth zone and fifth-eighth zone of the ext...
Embodiment 3
[0042] S1. Disperse 36.5 parts of ethyl titanate in 103 parts of organic solvent through ultrasonic oscillation equipment, add 3.85 parts of amine salt, stir evenly at room temperature, put the reaction solution in a reaction kettle, and react for 2.75 hours at 220°C Afterwards, naturally cool to room temperature, separate the solid phase, and obtain powder;
[0043] S2. Put the product obtained in step S1 into a mixing mixer, add 4 parts of flame retardant synergist, 6 parts of brominated flame retardant, and 0.55 parts of heat stabilizer in sequence to obtain a mixed material;
[0044] S3. Put the mixed material obtained in step S2 into a twin-screw extruder, control the screw speed to 390rpm, fill the delivery pump with liquid carbon dioxide, control the delivery pressure to 28.7MPa, and heat the carbon dioxide to the critical temperature (31°C), After converting it into supercritical carbon dioxide, inject it into the third-fourth zone and fifth-eighth zone of the extruder...
PUM
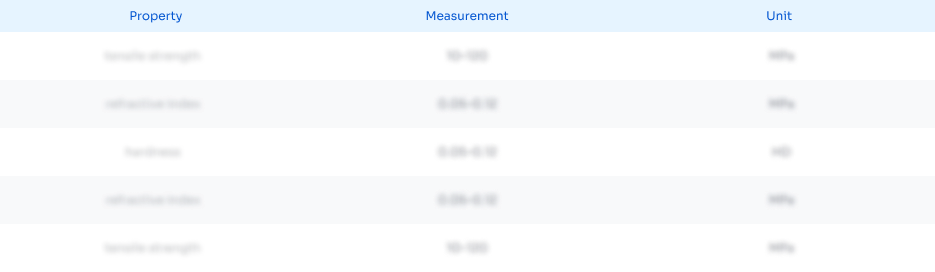
Abstract
Description
Claims
Application Information

- R&D
- Intellectual Property
- Life Sciences
- Materials
- Tech Scout
- Unparalleled Data Quality
- Higher Quality Content
- 60% Fewer Hallucinations
Browse by: Latest US Patents, China's latest patents, Technical Efficacy Thesaurus, Application Domain, Technology Topic, Popular Technical Reports.
© 2025 PatSnap. All rights reserved.Legal|Privacy policy|Modern Slavery Act Transparency Statement|Sitemap|About US| Contact US: help@patsnap.com