Waste glass powder sintered bricks and production method thereof
A technology of waste glass powder and sintered bricks, which is applied in the field of building materials, can solve problems such as large waste, and achieve the effects of enhancing flame retardancy, strong pressure bearing capacity, and saving clay resources
- Summary
- Abstract
- Description
- Claims
- Application Information
AI Technical Summary
Problems solved by technology
Method used
Examples
Embodiment 1
[0017] A waste glass powder sintered brick made from the following raw materials: 66 kg of waste glass powder, 5 kg of antimony trioxide, 10 kg of polyvinyl chloride resin, 8 kg of dioctyl sebacate, dimethyl terephthalate 12 kg of ester, 5 kg of antioxidant 616, 10 kg of tetrabromophthalic anhydride, 25 kg of polyvinyl chloride resin, 2 kg of nano-alumina, 10 kg of mesh soil, 8 kg of sea mud, 5 kg of polyvinyl acetate, 4 kg of tung oil, waste syrup 3kg, sodium lauroyl sarcosinate 1kg, fir gum 3kg, asbestos wool 4kg, additive 6kg, appropriate amount of water;
[0018] The additive is made of the following raw materials: 8 kg of garnet, 5 kg of fluorite slag, 10 kg of Yellow River silt, 3 kg of lithium carbonate, 4 kg of zirconium disilicide, 2 kg of hollow cerium oxide nanospheres, 4 kg of Turkish red oil, and 2 kg of tea dry powder; The preparation method is: mix garnet, fluorite slag, and Yellow River silt evenly, treat at 800°C for 3 hours, cool, crush, pass through a 10...
Embodiment 2
[0025] Waste glass powder 75 kg, antimony trioxide 10 kg, polyvinyl chloride resin 15 kg, dioctyl sebacate 12 kg, dimethyl terephthalate 15 kg, antioxidant 616 8 kg, tetrabromophthalic anhydride 15 kg kg, polyvinyl chloride resin 35 kg, nano-alumina 4 kg, mesh soil 12kg, sea mud 810kg, polyvinyl acetate 8kg, tung oil 5kg, waste syrup 4.5kg, sodium lauroyl sarcosinate 1.5kg, fir gum 4kg , 6kg of asbestos wool, 7kg of additives, appropriate amount of water;
[0026] The additive is made of the following raw materials: 10kg of garnet, 8kg of fluorite slag, 12kg of Yellow River silt, 3.5kg of lithium carbonate, 5kg of zirconium disilicide, 2.5kg of hollow cerium oxide nanospheres, 5kg of Turkish red oil, tea dry powder 3kg; the preparation method is: mix garnet, fluorite slag, and Yellow River silt evenly, treat at 900°C for 2.5h, cool, crush, pass through a 100-mesh sieve, add Turkish red oil and tea dry powder, grind evenly, and then Add the remaining raw materials, sti...
PUM
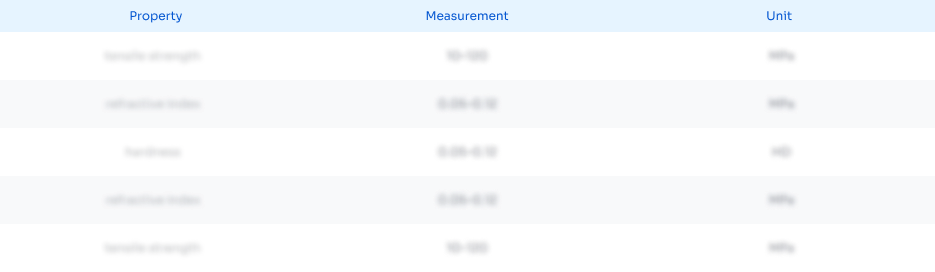
Abstract
Description
Claims
Application Information

- Generate Ideas
- Intellectual Property
- Life Sciences
- Materials
- Tech Scout
- Unparalleled Data Quality
- Higher Quality Content
- 60% Fewer Hallucinations
Browse by: Latest US Patents, China's latest patents, Technical Efficacy Thesaurus, Application Domain, Technology Topic, Popular Technical Reports.
© 2025 PatSnap. All rights reserved.Legal|Privacy policy|Modern Slavery Act Transparency Statement|Sitemap|About US| Contact US: help@patsnap.com