Forging forming process of heteromorphic transition section of super large pressure vessel
A pressure vessel and forging forming technology, which is applied in the field of forging technology, can solve the problems of increasing machining costs, large cutting volume, waste of raw materials, etc., and achieve the effects of improving pressure bearing capacity, reducing machining allowance, and reducing raw material consumption
- Summary
- Abstract
- Description
- Claims
- Application Information
AI Technical Summary
Problems solved by technology
Method used
Image
Examples
Embodiment 1
[0039] Before forming, the forging billet 6 is prepared using the existing technology, and the original billet is repeatedly upset and elongated by a hydraulic press to form a cylindrical forging billet 6 that meets the requirements of the forging ratio, and ensure that the metal streamline of the forging billet 6 is roughly the same. Axial parallel.
[0040] In order to reduce the heating times of the forging billet 6, reduce energy consumption, processing cycle, and heat consumption of the forging billet, all steps adopt hydraulic free forging. The specific process includes the following steps: 1), adopting the existing free forging and upsetting punching process to punch the forging blank 6; 2), as figure 2 As shown, the forging blank 6 after punching is axially elongated by using the existing free forging mandrel elongation process; image 3 As shown, the existing free forging mandrel horse frame reaming process is adopted to pre-expand the forged blank 6 after drawing; ...
PUM
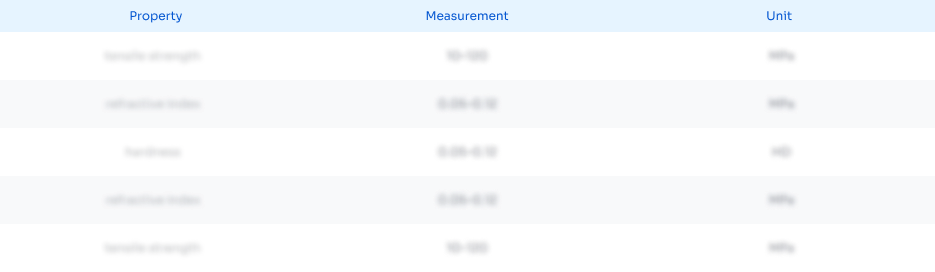
Abstract
Description
Claims
Application Information

- R&D
- Intellectual Property
- Life Sciences
- Materials
- Tech Scout
- Unparalleled Data Quality
- Higher Quality Content
- 60% Fewer Hallucinations
Browse by: Latest US Patents, China's latest patents, Technical Efficacy Thesaurus, Application Domain, Technology Topic, Popular Technical Reports.
© 2025 PatSnap. All rights reserved.Legal|Privacy policy|Modern Slavery Act Transparency Statement|Sitemap|About US| Contact US: help@patsnap.com