Polymer insulator with uniform hole distribution on surface and preparation method thereof
A polymer and insulator technology, applied in the directions of organic insulators, inorganic insulators, insulators, etc., can solve the problems of low surface breakdown voltage of polymer insulators, difficult to meet the insulation technical requirements of vacuum high-voltage devices, etc., to improve the surface breakdown voltage, The effect of improved mechanical properties and less influencing factors
- Summary
- Abstract
- Description
- Claims
- Application Information
AI Technical Summary
Problems solved by technology
Method used
Image
Examples
Embodiment 1
[0040] 1) At room temperature, mix evenly the nano fumed silica and styrene monomer of 1% by mass percent, then add 5% by mass percent of silica particles with an average particle diameter of 1 micron to the reaction system, and ultrasonically Stir evenly to obtain a uniformly dispersed stable oxide / monomer mixture;
[0041] 2) Polymerizing the oxide particle / styrene monomer mixture at 90°C to obtain a uniformly dispersed silica particle / polystyrene composite material;
[0042] 3) Processing composite materials into polymer insulators by mechanical processing;
[0043] 4) Use 15% hydrofluoric acid chemical etching to remove the silicon dioxide particles on the surface, and the silicon dioxide particles inside the insulator are protected from dissolution by the polymer;
[0044] 5) Take the insulator out of the acid solution, wash it with deionized water, and dry it, and finally obtain a polystyrene-based composite insulator with a uniform distribution of 1 micron-sized holes ...
Embodiment 2
[0046]1) At room temperature, the mass percentage is 2% of the nano fumed silicon dioxide and methyl methacrylate monomer mixed uniformly, and then adding 3% of the mass percentage of magnesium oxide particles with an average particle diameter of 0.5 microns to the reaction system , ultrasonically stirred evenly to obtain a uniformly dispersed stable magnesium oxide particle / methyl methacrylate monomer mixture;
[0047] 2) Polymerize the oxide particle / methyl methacrylate monomer mixture at 110°C to obtain a uniformly dispersed magnesium oxide particle / polymethyl methacrylate composite material;
[0048] 3) Processing composite materials into polymer insulators by mechanical processing;
[0049] 4) Using 20% hydrochloric acid to chemically corrode the magnesium oxide particles on the surface, and the magnesium oxide particles inside the insulator are protected from dissolution by the polymer;
[0050] 5) Take the insulator out of the acid solution, wash it with deionized wa...
Embodiment 3
[0052] 1) At room temperature, the mass percentage is 2% of nano fumed silica and bisphenol A epoxy resin (containing 2% methyltetrahydrophthalic anhydride curing agent) monomers are mixed uniformly, and then added to the reaction system Ferric oxide particles with an average particle size of 100 nanometers at a mass percentage of 3% are uniformly stirred by ultrasonic to obtain a uniformly dispersed stable oxide / monomer mixture;
[0053] 2) Polymerize the mixture of oxide particles / epoxy resin monomer at 100°C to obtain evenly dispersed ferric oxide particles / epoxy resin composite material;
[0054] 3) Processing composite materials into polymer insulators by mechanical processing;
[0055] 4) Using 20% hydrochloric acid chemical corrosion method to corrode and remove the ferric oxide particles on the surface, and the ferric oxide particles inside the insulator are prevented from being dissolved under the protection of the polymer;
[0056] 5) Take the insulator out of the...
PUM
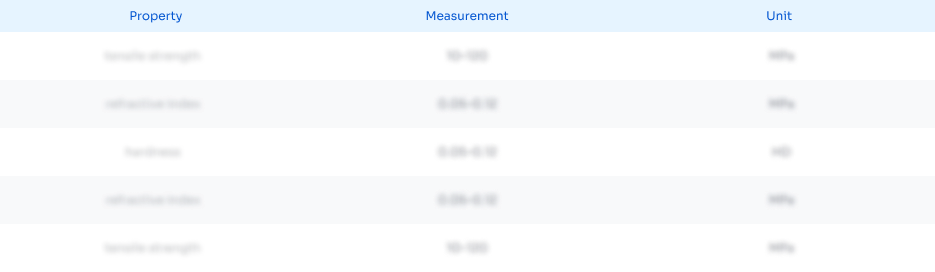
Abstract
Description
Claims
Application Information

- R&D
- Intellectual Property
- Life Sciences
- Materials
- Tech Scout
- Unparalleled Data Quality
- Higher Quality Content
- 60% Fewer Hallucinations
Browse by: Latest US Patents, China's latest patents, Technical Efficacy Thesaurus, Application Domain, Technology Topic, Popular Technical Reports.
© 2025 PatSnap. All rights reserved.Legal|Privacy policy|Modern Slavery Act Transparency Statement|Sitemap|About US| Contact US: help@patsnap.com