Controlled rolling method implemented by stably controlling low-temperature toughness of large-wall-thickness pipeline steel
A technology with stable control and low-temperature toughness, which is applied in the field of production of hot-rolled steel plates for large-diameter and large-wall-thickness pipeline steel. Solve the problems such as the tenite grain structure, achieve the effect of stabilizing the low-temperature drop hammer toughness, improving the uniformity of the grain structure, and the large deformation rate
- Summary
- Abstract
- Description
- Claims
- Application Information
AI Technical Summary
Problems solved by technology
Method used
Examples
Embodiment 1
[0011] The product is The low-temperature toughness of hot-rolled steel plates for pipeline steel requires Charpy impact toughness in the center of the thickness direction and low-temperature drop weight performance.
[0012] One, the production situation before the application of the present invention
[0013] The rolling is divided into two stages of rough rolling and finishing rolling. The rolling temperature of the final pass of rough rolling is 1010°C, and the pass is automatically split. The actual deformation rate of the final pass is 12%. The low-temperature toughness of the rolled steel plate is shown in Table 1. Show.
[0014] Table 1 Low temperature toughness of steel plate
[0015] Sample number
-20℃ Heart Charpy Impact Energy (J)
-15℃ full wall thickness drop weight DWTT(%)
1
282 / 266 / 189
52 / 56
2
293 / 175 / 124
38 / 35
3
131 / 92 / 97
32 / 33
[0016] Two, the production situation after the application o...
Embodiment 2
[0021] The product is The low-temperature toughness of hot-rolled steel plates for grade submarine pipeline steel requires Charpy impact toughness in the center of the thickness direction and low-temperature drop weight performance.
[0022] One, the production situation before the application of the present invention
[0023] The rolling is divided into two stages of rough rolling and finishing rolling. The rolling temperature of the final pass of rough rolling is 1000°C, and the pass is automatically split. The actual deformation rate of the final pass is 11%. The low-temperature toughness of the rolled steel plate is shown in Table 3. Show.
[0024] Table 3 Low temperature toughness of steel plate
[0025] Sample number
-20℃ Heart Charpy Impact Energy (J)
-15℃ full wall thickness drop weight DWTT(%)
1
172 / 256 / 269
42 / 45
2
263 / 235 / 144
35 / 38
3
102 / 137 / 124
32 / 34
[0026] Two, the production situation after...
Embodiment 3
[0031] The product is The low-temperature toughness of hot-rolled steel plates for grade acid-resistant pipeline steel requires Charpy impact toughness in the center of the thickness direction and low-temperature drop weight performance.
[0032] One, the production situation before the application of the present invention
[0033] The rolling is divided into two stages: rough rolling and finishing rolling. The rolling temperature of the final pass of rough rolling is 1020°C, and the pass is automatically split. The actual deformation rate of the final pass is 12.5%. The low-temperature toughness of the steel plate is shown in Table 5.
[0034] Table 5 Low temperature toughness of steel plate
[0035] Sample number
-20℃ Heart Charpy Impact Energy (J)
-15℃ full wall thickness drop weight DWTT(%)
1
185 / 167 / 249
57 / 59
2
178 / 165 / 203
46 / 48
[0036] 3
142 / 133 / 115
44 / 43
[0037] Two, the production situa...
PUM
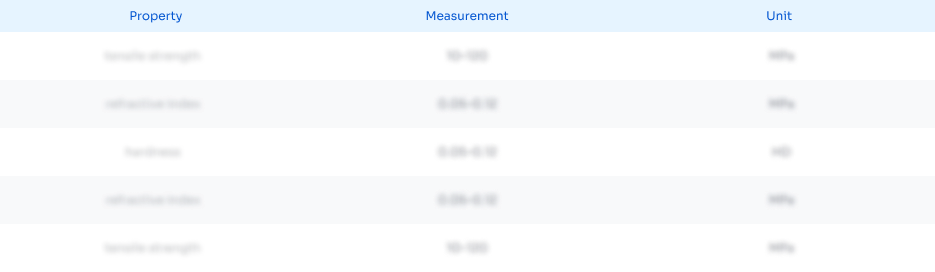
Abstract
Description
Claims
Application Information

- R&D Engineer
- R&D Manager
- IP Professional
- Industry Leading Data Capabilities
- Powerful AI technology
- Patent DNA Extraction
Browse by: Latest US Patents, China's latest patents, Technical Efficacy Thesaurus, Application Domain, Technology Topic, Popular Technical Reports.
© 2024 PatSnap. All rights reserved.Legal|Privacy policy|Modern Slavery Act Transparency Statement|Sitemap|About US| Contact US: help@patsnap.com