Composite-coating continuous casting crystallizer copper plate with long service life and manufacturing technology thereof
A continuous casting crystallizer and composite coating technology, which is applied in the direction of metal material coating process, coating, molten spraying, etc., can solve the problem of increasing the amount and frequency of crystallizer copper plate repair, restricting the normal operation of production, and the amount of steel passing in a single pass Large and other problems, to achieve the effect of continuous casting production efficiency and product quality improvement, superior anti-wear performance, low porosity
- Summary
- Abstract
- Description
- Claims
- Application Information
AI Technical Summary
Problems solved by technology
Method used
Image
Examples
Embodiment 1
[0038] Such as figure 1 As shown, a long-life composite plating continuous casting mold copper plate of the present invention includes a copper plate base 1 and a plating layer on the surface of the copper plate base 1. The plating layer includes an upper electroplating layer 2 and a lower spraying layer 3. The upper electroplating layer 2 is a high-temperature and corrosion-resistant low-cobalt nickel alloy coating, the mass percentage of cobalt in the low-cobalt nickel alloy coating is not more than 3%, and the lower sprayed layer 3 is a wear-resistant coating.
[0039] Wherein, the upper electroplating layer 2 is 0-100 mm away from the upper opening of the copper plate base; and the lower sprayed layer 3 is 100-900 mm away from the upper opening of the copper plate base.
[0040] The preparation process of the long-life composite coating continuous casting mold copper plate can be carried out according to the following steps:
[0041] A. Perform conventional pre-plating pretreatm...
Embodiment 2
[0060] Such as figure 1 As shown, a long-life composite plating continuous casting mold copper plate of the present invention includes a copper plate base 1 and a plating layer on the surface of the copper plate base 1. The plating layer includes an upper electroplating layer 2 and a lower spraying layer 3. The upper electroplating layer 2 is a low-cobalt nickel alloy coating with high temperature resistance and corrosion resistance, the mass percentage of cobalt in the low-cobalt nickel alloy coating is not more than 3%, and the lower sprayed layer 3 is a ceramic coating.
[0061] Wherein, the upper electroplating layer 2 is 0-200 mm away from the upper opening of the copper plate base; the lower sprayed layer 3 is 200-900 mm away from the upper opening of the copper plate base.
[0062] The preparation process of the long-life composite coating continuous casting mold copper plate can be carried out according to the following steps:
[0063] A. Perform conventional pre-plating pre...
Embodiment 3
[0081] Such as figure 1 As shown, a long-life composite plating continuous casting mold copper plate of the present invention includes a copper plate base 1 and a plating layer on the surface of the copper plate base 1. The plating layer includes an upper electroplating layer 2 and a lower spraying layer 3. The upper electroplating layer 2 is a high-temperature and corrosion-resistant pure nickel plating layer, and the lower sprayed layer 3 is a wear-resistant coating.
[0082] Wherein, the upper electroplating layer 2 is 0-300 mm away from the upper opening of the copper plate base; the lower sprayed layer 3 is 300-900 mm away from the upper opening of the copper plate base.
[0083] The preparation process of the long-life composite coating continuous casting mold copper plate can be carried out according to the following steps:
[0084] A. Perform conventional pre-plating pretreatment on the surface of the copper plate of the continuous casting mold, including machine tool proces...
PUM
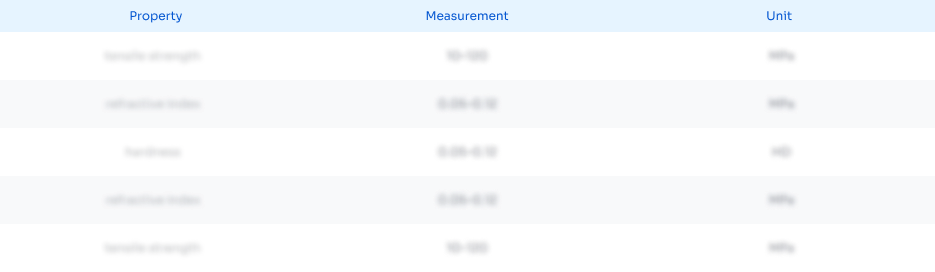
Abstract
Description
Claims
Application Information

- R&D
- Intellectual Property
- Life Sciences
- Materials
- Tech Scout
- Unparalleled Data Quality
- Higher Quality Content
- 60% Fewer Hallucinations
Browse by: Latest US Patents, China's latest patents, Technical Efficacy Thesaurus, Application Domain, Technology Topic, Popular Technical Reports.
© 2025 PatSnap. All rights reserved.Legal|Privacy policy|Modern Slavery Act Transparency Statement|Sitemap|About US| Contact US: help@patsnap.com