High magnetic-energy-product M type calcium series permanent magnetic ferrite material and preparation method thereof
A technology of permanent magnet ferrite and high magnetic energy product, applied in the field of high magnetic energy product M-type calcium series permanent magnet ferrite material and its preparation field, can solve the problems of inability to prepare ferrite devices, difficult to achieve, etc. The effect of miniaturization, energy saving and collapse prevention
- Summary
- Abstract
- Description
- Claims
- Application Information
AI Technical Summary
Problems solved by technology
Method used
Image
Examples
Embodiment 1
[0031] The main raw material is La2 o 3 , CaCO 3 , SrCO 3 , Fe 2 o 3 and Co 3 o 4 , with R 1-x-y Ca x La y O· n Fe (12-z) / n co z / n o 3 Preparation of Sr 0.74 Ca 0.10 La 0.16 O·5.95Fe 1.97 co 0.08 o 3 .
[0032] According to Sr 0.74 Ca 0.10 La 0.16 O·5.95Fe 1.97 co 0.08 o 3 For stoichiometry, add accounted for Sr 0.74 Ca 0.10 La 0.16 O·5.95Fe 1.97 co 0.08 o 3 0.2 of the weight wt %Al 2 o 3 , 0.3 wt %Cr 2 o 3 , 0.5 wt %B 2 o 3 , 0.2 wt % SiO 2 . Add the above mixed powder and water into a ball mill and mix for 3 hours to obtain a mixed material with a suspended particle size of 0.1-2.0 μm. After drying, pre-calcine in air at 1290°C for 3 hours, and XRD analysis determines that the phase is Contains 95 wt % M phase, while its main grain size is 9 μm.
[0033] Grind in a ball mill until the average particle size is less than or equal to 5.0 μm, and the specific surface area of the obtained grinding powder (obtained by BET method) ...
Embodiment 2
[0039] The main raw material is La 2 o 3 , SrCO 3 , CaO, Fe 2 o 3 and Co 3 o 4 , with R 1-x-y Ca x La y O· n Fe (12-z) / n co z / n o 3 Preparation of Sr 0.73 Ca 0.09 La 0.18 O·6.0Fe 1.93 co 0.09 o 3 .
[0040] According to Sr 0.73 Ca 0.09 La 0.18 O·6.0Fe 1.93 co 0.09 o 3 For stoichiometry, add accounted for Sr 0.73 Ca 0.09 La 0.18 O·6.0Fe 1.93 co 0.09 o 3 0.6 of wt %Al 2 o 3 , 0.3 wt %Cr 2 o 3 , 0.4 wt %B 2 o 3 , 0.2 wt % SiO 2 . Mix in a ball mill for 5 hours to obtain a mixture with a suspended particle size of 1.5 μm. Pre-fired at 1280°C for 2 hours in air atmosphere. XRD confirms that the phase usually contains 90 wt % M phase, and its main grain is 10 μm.
[0041] Grind in a ball mill until the average particle size becomes a powder less than or equal to 5.0 μm, and the specific surface area of the obtained grinding powder (obtained by BET method) is 9m 2 / g.
[0042] Carry out heat treatment in the air atmosphere, the te...
Embodiment 3
[0047] The main raw material is La 2 o 3 , CaCO 3 , SrCO 3 , CeO 2 , Fe 2 o 3 and Co 2 o 3 , with R 1-x-y Ca x La y O· n Fe (12-z) / n co z / n o 3 Preparation of Sr 0.3 Ce 0.410 Ca 0.13 La 0.16 O·6.1Fe 1.9 co 0.05 o 3 .
[0048] According to Sr 0.3 Ce 0.41 Ca 0.13 La 0.16 O·6.1Fe 1.9 co 0.05 o 3 For stoichiometry, add accounted for Sr 0.3 Ce 0.41 Ca 0.13 La 0.16 O·6.1Fe 1.9 co0.05 o 3 0.5 of wt %Al 2 o 3 , 0.3 wt %Cr 2 o 3 , 0.6 wt %B 2 o 3 , 0.3 wt % SiO 2 . Mix in a ball mill for 5 hours to obtain a mixed material with a suspended particle size of 1.5 μm. Pre-fired at 1200°C for 2 hours in an air atmosphere. XRD confirmed that the phase contained 95 wt % M phase, and its main grain is 10 μm.
[0049] Grind in a ball mill until the average particle size becomes a powder less than or equal to 5.0 μm, and the specific surface area of the obtained grinding powder (obtained by BET method) is 8m 2 / g.
[0050] Carry out heat ...
PUM
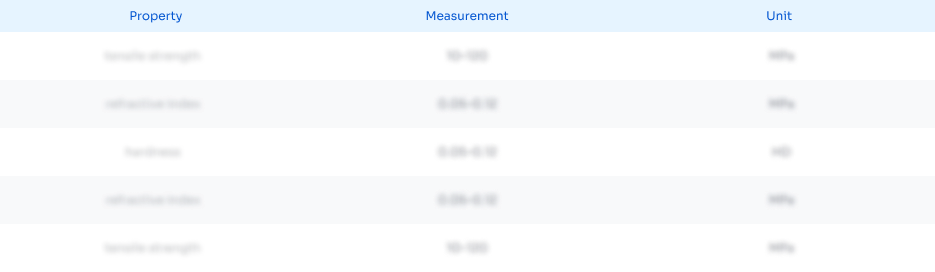
Abstract
Description
Claims
Application Information

- R&D
- Intellectual Property
- Life Sciences
- Materials
- Tech Scout
- Unparalleled Data Quality
- Higher Quality Content
- 60% Fewer Hallucinations
Browse by: Latest US Patents, China's latest patents, Technical Efficacy Thesaurus, Application Domain, Technology Topic, Popular Technical Reports.
© 2025 PatSnap. All rights reserved.Legal|Privacy policy|Modern Slavery Act Transparency Statement|Sitemap|About US| Contact US: help@patsnap.com