A kind of modified bagasse-plastic composite material and its preparation method and application
A composite material and technology of bagasse, which is applied in the field of preparation of modified bagasse-plastic composite materials, can solve the problems of complex physical modification methods, difficulty in industrial production, environmental pollution, etc., achieve remarkable modification effects, low production costs, and reliable good control effect
- Summary
- Abstract
- Description
- Claims
- Application Information
AI Technical Summary
Problems solved by technology
Method used
Image
Examples
Embodiment 1
[0030] (1) Bagasse is put into a blast drying oven, dried at 105° C. for 3 hours, then pulverized with a high-speed pulverizer for 3 minutes, and passed through a 100-mesh sieve (scanning electron microscope photo as shown in figure 1 Shown); use the mechanical activation method to modify the surface of the fiber: the mechanical activation treatment equipment adopts a ball mill, and the grinding ball medium and bagasse fiber are added to the grinding cylinder of the ball mill. Be 100min (the scanning electron micrograph of bagasse fiber when processing 60min is as figure 2 shown);
[0031] (2) According to maleic anhydride: acetone mass ratio = 1:2, maleic anhydride is dissolved in acetone to prepare a solution, then the bagasse activated by step (1) is dropped into the solution according to the solid-to-liquid ratio of 1:2 and stirred evenly Dry, the content of maleic anhydride is 5% of the bagasse fiber; then put the dried bagasse into the ball mill, add BPO accounting for...
Embodiment 2
[0039] (1) Put the bagasse into the blast drying box, dry it at 105° C. for 3 hours, pulverize it with a high-speed pulverizer for 3 minutes, and pass through a 100-mesh sieve; adopt the mechanical activation method to modify the surface of the fiber: the mechanical activation treatment equipment adopts a ball mill, Add grinding medium and bagasse fiber to the grinding cylinder of the ball mill, the speed of rotation is 60 rpm, the temperature is 40°C, and the surface modification time is 50 minutes;
[0040] (2) According to maleic anhydride: acetone mass ratio = 1:3, maleic anhydride is dissolved in acetone to prepare a solution, then the bagasse activated by step (1) is dropped into the solution according to the solid-to-liquid ratio of 1:3 and stirred evenly Dry in the air to ensure that the content of maleic anhydride is 6% of the bagasse fiber; then put the dried bagasse into the ball mill, add BPO accounting for 5% of the bagasse fiber at the same time, heat up to 80°C, ...
Embodiment 3
[0047] (1) Put the bagasse into the blast drying box, dry it at 105° C. for 3 hours, pulverize it with a high-speed pulverizer for 3 minutes, and pass through a 100-mesh sieve; adopt the mechanical activation method to modify the surface of the fiber: the mechanical activation treatment equipment adopts a ball mill, Add grinding media and bagasse fibers to the grinding cylinder of the ball mill, at a speed of 50 rpm and a temperature of 55°C, and the surface modification time is 10 minutes;
[0048] (2) According to maleic anhydride: acetone mass ratio = 1:4, maleic anhydride is dissolved in acetone to prepare a solution, and then the bagasse activated by step (1) is dropped into the solution according to the solid-to-liquid ratio of 1:3 and stirred evenly and then naturally Dry in the air to ensure that the content of maleic anhydride is 8% of the bagasse fiber; then put the dried bagasse into the ball mill, add BPO accounting for 8% of the bagasse fiber at the same time, heat...
PUM
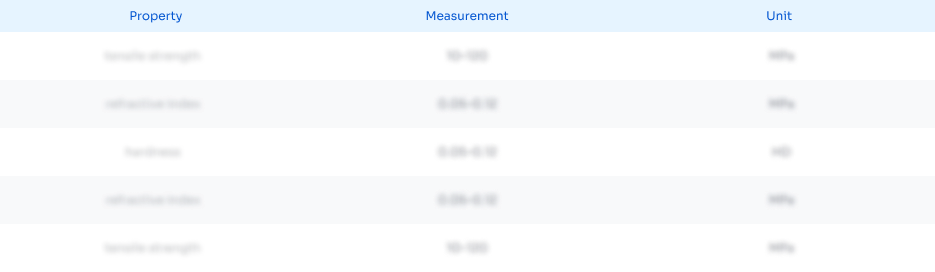
Abstract
Description
Claims
Application Information

- Generate Ideas
- Intellectual Property
- Life Sciences
- Materials
- Tech Scout
- Unparalleled Data Quality
- Higher Quality Content
- 60% Fewer Hallucinations
Browse by: Latest US Patents, China's latest patents, Technical Efficacy Thesaurus, Application Domain, Technology Topic, Popular Technical Reports.
© 2025 PatSnap. All rights reserved.Legal|Privacy policy|Modern Slavery Act Transparency Statement|Sitemap|About US| Contact US: help@patsnap.com