Method for denitrifying NO by directly decomposing NO catalytically by using supported metal oxide catalyst
A catalyst and oxide technology, applied in the field of catalytic denitration, can solve the problems of complex process and low NO removal rate, and achieve the effects of simple process, low operating cost and low operating temperature
- Summary
- Abstract
- Description
- Claims
- Application Information
AI Technical Summary
Problems solved by technology
Method used
Image
Examples
Embodiment 1 and comparative example 1
[0019] The supported metal oxide catalyst was prepared by equal volume impregnation method. First, activated alumina was calcined at 500°C for 2 hours to obtain Al 2 o 3 carrier. Then Al 2 o 3 The carrier was mixed with equal volumes of metal nitrate solutions of different concentrations, ultrasonicated for 0.5h at room temperature, and then impregnated for 24h. The obtained impregnation mixture was then dried at 100 °C for 6 h. Then calcined at 500°C for 2h to prepare a series of Al 2 o 3 supported metal oxide catalysts. The loads of metal oxides are shown in Table 1.
[0020] Table 1
[0021]
Embodiment 2 and comparative example 2
[0023] The method of the invention includes filling catalysts in the reaction tube of the microwave catalytic reactor device to form a microwave catalytic reaction bed, and the gas to be treated undergoes gas-solid phase reaction for denitration treatment when passing through the microwave catalytic reaction bed. The catalyst is the metal oxide prepared in Example 1 and Comparative Example 1 supported on Al 2 o 3 On the carrier, the composition is CuO x / Al 2 o 3 , MnO x / Al 2 o 3 , NiO x / Al 2 o 3 , CuMnO x / Al 2 o 3 , CeCuO x / Al 2 o 3 , CeMnO x / Al 2 o 3 , CeNiO x / Al 2 o 3 and CeCuMnO x / Al 2 o 3 Catalyst; the catalyst is filled in the reaction tube of the microwave catalytic reactor device, when the gas to be treated passes through the microwave catalytic reaction bed, the NO in the gas is directly decomposed and reacted to generate environmentally friendly N 2 and O 2 , in order to achieve the purpose of direct denitrification.
[0024]In this e...
Embodiment 3 and comparative example 3
[0032] It is basically the same as Example 2 and Comparative Example 2, except that the content of oxygen in the intake air is changed to 0-10%.
[0033] The loading amount of the catalyst in Example 3 and Comparative Example 3 is 1.5 g respectively, and the mesh size is 40-60 mesh. The intake NO concentration is 1000ppm, the oxygen content in the intake air is changed to 0%, 5%, 7.5%, 10%, the residence time of the gas in the microwave catalytic reaction bed is 1s, and the reaction pressure is normal pressure. The microwave power was adjusted to maintain the temperature of the catalyst bed at 250°C, and the oxidation resistance of the catalyst in the microwave catalytic decomposition of NO was investigated. The results are shown in Table 3.
[0034] table 3
[0035]
[0036] In the presence of oxygen, the conversion rate of NO is not affected by the oxygen concentration on each catalyst, indicating that the supported metal oxide catalysts in the comparative examples and ...
PUM
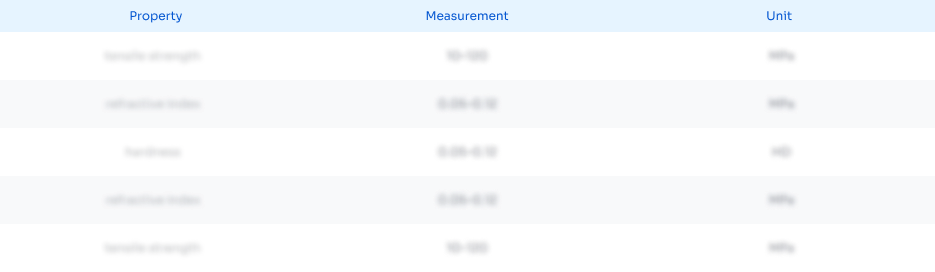
Abstract
Description
Claims
Application Information

- Generate Ideas
- Intellectual Property
- Life Sciences
- Materials
- Tech Scout
- Unparalleled Data Quality
- Higher Quality Content
- 60% Fewer Hallucinations
Browse by: Latest US Patents, China's latest patents, Technical Efficacy Thesaurus, Application Domain, Technology Topic, Popular Technical Reports.
© 2025 PatSnap. All rights reserved.Legal|Privacy policy|Modern Slavery Act Transparency Statement|Sitemap|About US| Contact US: help@patsnap.com